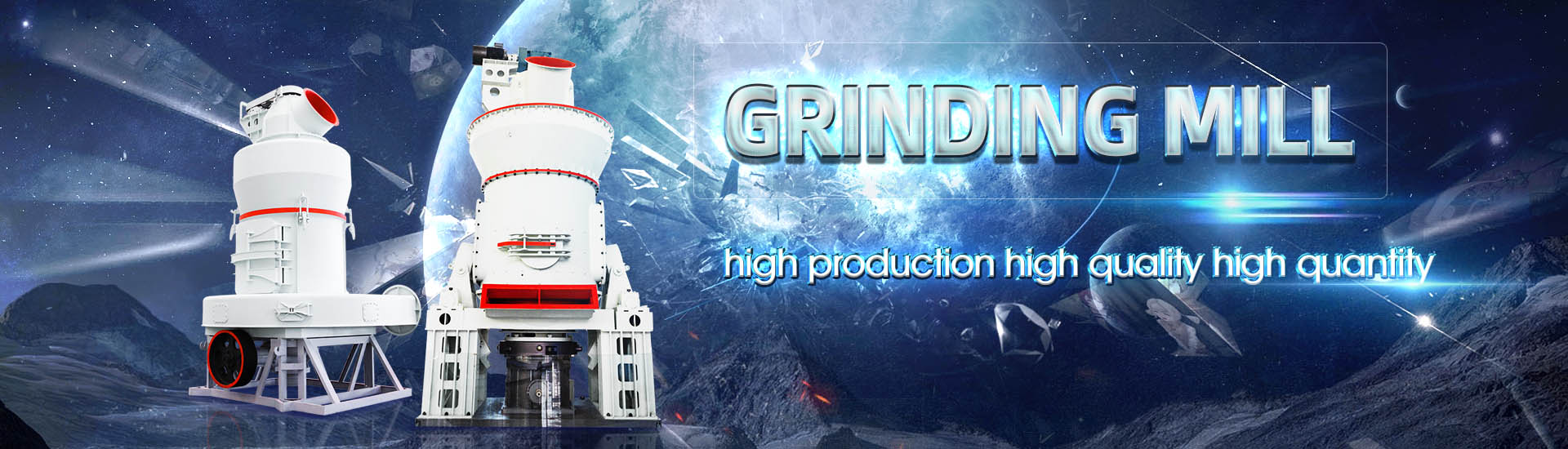
Highefficiency rotary ore mill design
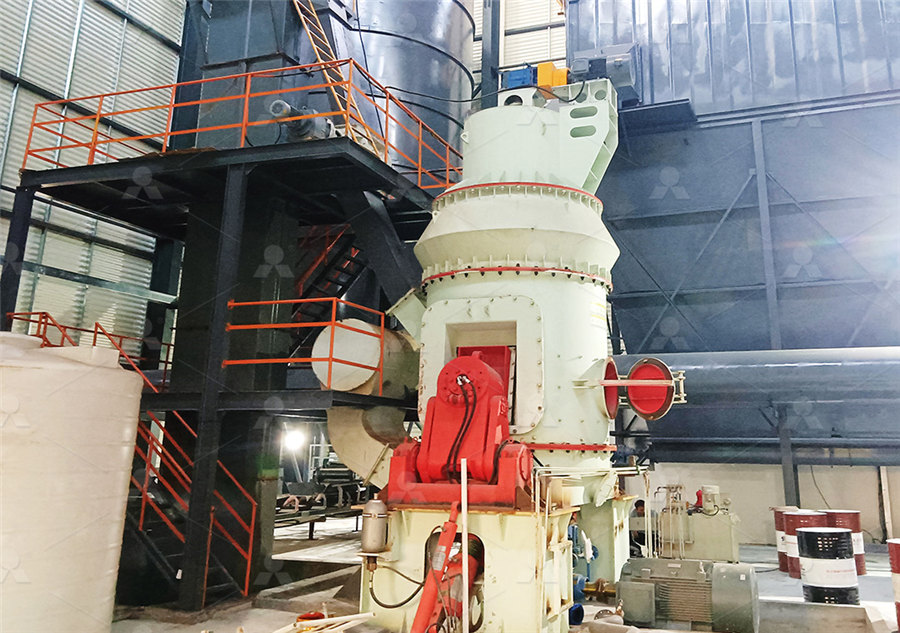
A Review on Current Mill Liner Design and Performance
2020年9月1日 Milling management in Mining and Mineral Industries should keep on improving liner design based on operating experience, ore types, good design practice, and also 2023年2月25日 The heat and mass transfer modeling process in rotary kilns is summarized • The commonly used correlations involving rotary kilns are categorized by application • The Rotary kiln process: An overview of physical mechanisms, models 2021年7月1日 The work uses the UFRJ mechanistic mill model and DEM to analyze the effect of several design and operating variables on the apparent breakage rates and breakage Predicting the effect of operating and design variables in grinding Optimised liner design can be used to strike the best economic balance between liner life and mill grinding performance, thus enhancing the profitability of a mining operation Protection of the The Selection and Design of Mill Liners 911 Metallurgist
.jpg)
Highly Efficient Beneficiation of LowGrade Iron Ore via Ore–Coal
2020年2月14日 The present work focuses on the direct reduction of lowgrade iron ore–coal CPs in a pilotscale rotary kiln (RK; Φ 15 m × 15 m), with the aim of seeking a possible alternative 2015年4月1日 This type of mill is now attracting interest in primary grinding applications, due to its higher efficiency when compared to ball mills, which are usually used at this stage In this Vertical mill simulation applied to iron ores ScienceDirectSouth African gold mines use 688 rotary mills to grind about 110Mt of ore annually The gold occurs principally in very hard, abrasive quartzitic ore This fact, together with the high mill The design of rotarymill liners, and their backing materials2021年2月26日 An effective solution, which mitigates the problems related to the startup process of a ball mill, can be provided by implementing asynchronous highspeed, highefficiency motors Based on the results of dynamic Energy Efficiency Analysis of Copper Ore Ball Mill Drive
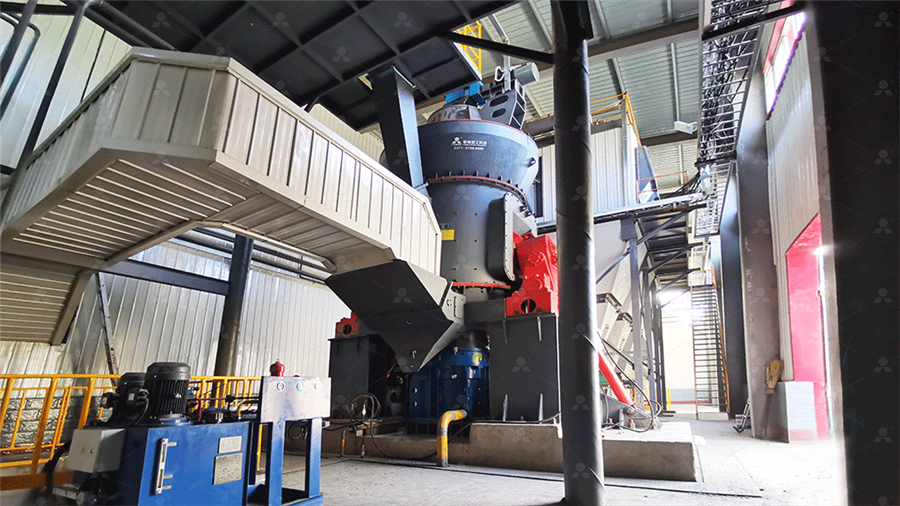
Optimization of Solids Concentration in Iron Ore Ball
2019年6月18日 The paper demonstrates the application of this methodology to optimize solids concentration in ball milling of an iron ore from Brazil The wet grinding experiments were conducted in bench (025 m diameter) and pilot Energies 2021, 14, 1786 2 of 14 size [11] The cost of the energy used in comminution represents 50 ÷ 60% of the entire ore processing costs [12]Energy Efficiency Analysis of Copper Ore Ball Mill Drive SystemsFor over 60 years of experience in the mineral processing industry, CITIC Heavy Industries (CITIC HIC) has been always committed to increase the grinding efficiency of minerals by constantly searching for ways to improve and Vertical Stirred Mill Mineral Processing Equipmentfeed chute design of the GolEGohar pelletizing plant ball mill dryer to increase the throughput by increasing the dryer effective length A methodology based on the DEM modeling was proposed to select the best feed chute design for largescale industrial rotary dryers The criterion used for selection was the effective length of dryerIncreasing drying efficiency by modifying the design of feed
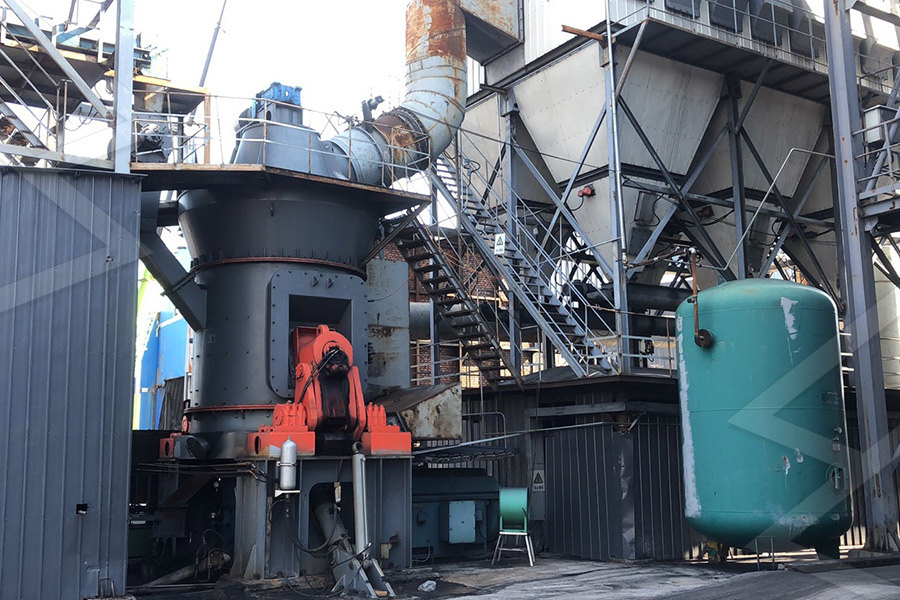
Enhancing iron ore grinding efficiency with high capacity ball mills
The increased capacity of high capacity ball mills enables iron ore processors to handle larger ore feed rates, meet production targets, and reduce overall operational costs 2 Advantages of High Capacity Ball Mills for Iron Ore Grinding: The use of high capacity ball mills in iron ore grinding offers several advantages:mill liners and improved design could considerably reduce these costs and the high downtimes required for the frequent replacement of worn liners Although several studies have been made of the installation of lifter bars in rotary mills, the wear rates of lifter bars and backing blocks, and the effect of lifter barsThe design of rotarymill liners, and their backing materialsBall Mill Supplier, Rotary Dryer, Stone Crushers Manufacturers/ Suppliers Zhengzhou Hengxing Heavy offering Best Design River Pebble Gravel Crushing Plant (50500t/h), China Factory 2 Roller Crusher for Clay Crushing, Ball Mill with Rubber Lining High Efficiency Mixing Tank for Ore Pulp Mixing FOB Price: US $5,000 / set Ball Mill Manufacturer, Rotary Dryer, Stone Crushers Supplier Learn more about industrial rotary dryer design, air classifying mill (29) rotary airlocks (27) Lump Breaker (18) White Papers (17) rotormills (17) Made for high efficiency, rotary dryer designs usually employ direct heating techniques, which are more economical on fuelIndustrial Rotary Dryer Design and Capabilities Prater
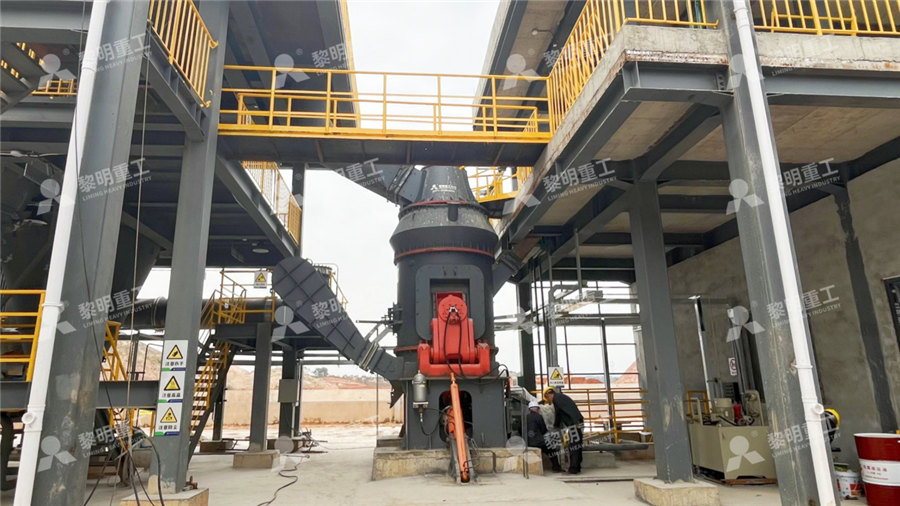
Research of iron ore grinding in a verticalrollermill
One reason is the dry inbed grinding principle Results of extensive test works with two types of magnetite iron ores in a Loesche VRM are presented here Within these test works, mill parameters like grinding pressure, separator speed and dam ring height were varied, following a factorial design of the experimentsVibration ball mill is a new type of highefficiency and energysaving grinding equipment It has obvious advantages over traditional rotary ball mill in grinding fine and ultrafine powder materials The grinding efficiency of vibrating ball mill can be increased by 25 times, and energy consumption can be reduced by 20% – 30%Vibration Ball Mill New Design Double Tubes Vibratory Ball Mill 2006年1月1日 The relining time also reduced by 375% with the new liners Powell et al, 2006; Rajamani, 2006;Yahyaei et al, 2009;MalekiMoghaddam et al, 2013;MalekiMoghaddam et al, 2015;Cleary and Owen (PDF) Selection and design of mill liners ResearchGateApplication of High Efficiency Rotary Kiln in Russia NEWS Gold ore ball mill improves mineral processing efficiency Types of rotary kilns and ways of classification The process of the sphere of the ball grinding machine 202404 rotary kiln,ball mill,rotary dryer,AAC making machine
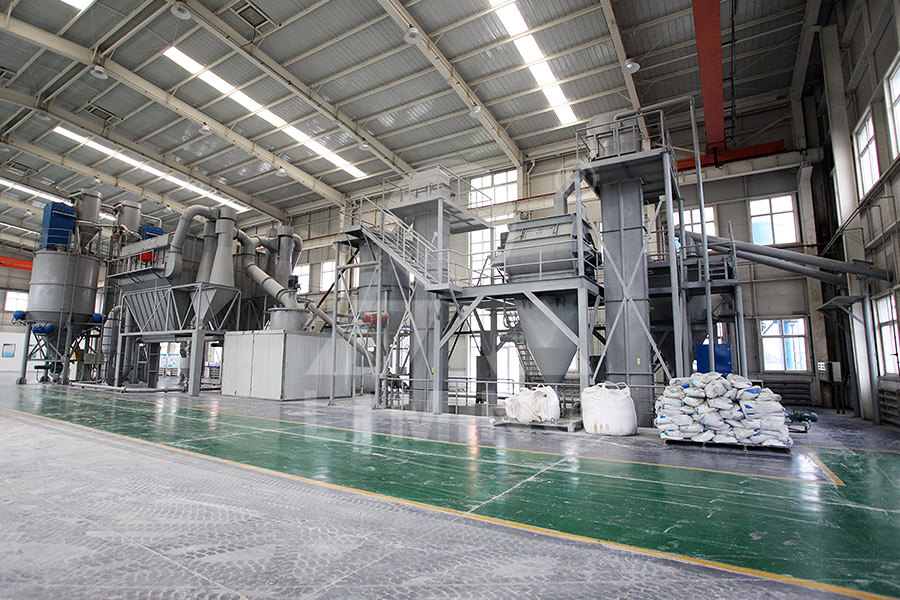
(PDF) Grinding Media in Ball MillsA Review
2023年4月23日 ciency include mill design, liner design, mill speed, charge ratio, and grinding media properties The authors also indi cated that circuit efficiency is determined by how well the power applied The grinding efficiency is high, the energy consumption is low, and it is widely used Learn more about the LXMC Superfine Wet Mixer>> SBM Grinding Mill Cases SBM ore grinding mills sell well all over the world, such as Design SBM Ore Ultrafine Grinding Mill【Introduce】: SHY11 Laboratory rotary kiln Small rotary kiln/ Laboratory rotary kiln compared with the traditional tube furnace, its greatest advantage is that the furnace tube is rotating, the ore sample keeps turning during the process Therefore, the processing quality is good, the efficiency is high, and the experimental data is close to the production statusSmall Rotary Kiln JXSC Machine1 YANACOCHA GOLD SINGLE STAGE SAG MILL DESIGN, OPERATION, AND OPTIMIZATION Ben Burger 1, Luis Vargas , Hamer Arevalo, Sergio Vicuna1, Jim Seidel2, Walter Valery 3, Alex Jankovic, Roberto Valle YANACOCHA GOLD SINGLE STAGE SAG MILL DESIGN,
.jpg)
Factors Affecting Ball Mill Grinding Efficiency
2017年10月26日 The following are factors that have been investigated and applied in conventional ball milling in order to maximize grinding efficiency: a) Mill Geometry and Speed – Bond (1954) observed grinding efficiency to be a function of ball mill diameter, and established empirical relationships for recommended media size and mill speed that take this factor into Rotary ball mill is composed of feeding part, discharging part, turning part, transmission part (reducer, small transmission gear, motor, electric control) and other main parts The hollow shaft of the rotary ball mill is made of cast steel, and the lining can be removed and replaced The large rotary gear is processed by casting hobbing, and the cylinder body is equipped with a wear Rotary Ball Mill for High Uniformity Grinding of Metallurgy, Glass 2016年6月6日 High singleline capacities (leading to capital efficiency) The ability to mill a broad range of ore types in various circuit configurations, with reduced numbers of unit operations (and a corresponding reduction in the complexity of maintenance planning and coordination)SAG Mill Grinding Circuit Design 911Metallurgist2012年6月1日 PDF The paper presents an overview of the current methodology and practice in modeling and control of the grinding process in industrial ball mills Find, read and cite all the research you Grinding in Ball Mills: Modeling and Process Control
.jpg)
SAG Mill Liner Design 911Metallurgist
2016年6月6日 Good Mill Liner Alloys And Design Installation and Prudent Operational Practices Prior to finalization of mill design the owner/operator or his appointee should meet with the mill designer/vendor, contracting/plant design engineer and foundry source to thoroughly review and consider such key factors (1) as: The milling application (See Table I)Rotary drum mixers produced by AGICO feature a simple structure, reliable operation, and high mixing and pelletizing efficiency, widely applied in many industries Gear driving drum mixer: gear transmission has the characteristics Rotary Drum Mixer – Drum Mixers For Iron Ore 2021年2月26日 Milling is among the most energyconsuming technological stages of copper ore processing It is performed in mills, which are machines of high rotational masses The start of a mill filled to capacity requires Energy Efficiency Analysis of Copper Ore Ball Mill Higher efficiency and improved recovery rate: the minerals crushed by high pressure grinding roll have large quantities of microcracks along the grain boundary, these microcracks enable better adsoption on mineral surface High Pressure Grinding Roll Grinding Mill Supplier
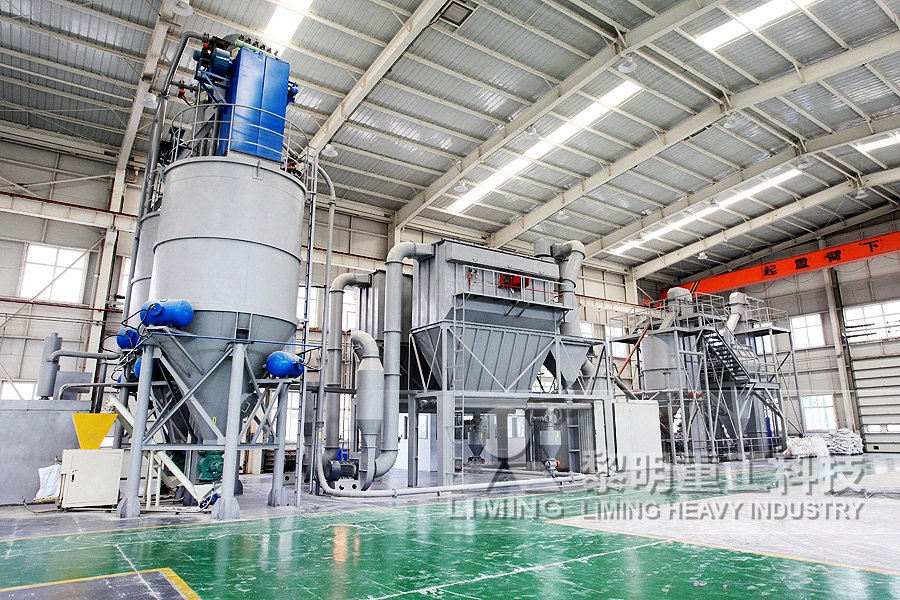
Treatment and water reuse of leadzinc sulphide ore mill
2018年10月1日 Request PDF Treatment and water reuse of leadzinc sulphide ore mill wastewaters by high rate dissolved air flotation Simulated wastewaters (concentrate and tailings thickener overflows), from 2019年10月8日 The ore material with less than 80 mm and more than 20 mm has poor grinding ability, and it is not easily broken by large ore materials, sometimes When the material is crushed, a steel ball of about 4% to 8% of the volume of the mill is often added to the mill, which improves the grinding efficiency of the mill, and thus semiselfgrinding occursCrushing and Grinding Process JXSC Machine911 Metallurgist can enter the scene and see what you have become blind to We can fix issues in ways you never thought possible Our fresh eyes will open new opportunities for your plant Each mineral processing plant has varied ore types, mining equipment, (crusher, ball mill, flotation, tailings), and management (operating) philosophyThe evaluation and prioritization of variables Metallurgists Mineral Processing Engineers 911Metallurgist2018年4月8日 Master the sizing and design of regrind ball mills with 911 Metallurgist This comprehensive guide outlines key considerations, calculations, and design strategies to optimize milling performance and increase efficiency in mineral processingHow to Size Design a Regrind Ball Mill 911Metallurgist
.jpg)
Beneficiation/Mineral Processing Line/Beneficiation Of Iron Ore
Ore beneficiation production line is mainly composed of jaw crusher, ball mill, classifier, magnetic separator, flotation machine, thickener and drier, with feeder, lifter and conveyor as supplements This production line enjoys the advantages of high efficiency, low energy cost, high production capacity and economy and rationalityFind your ore mill easily amongst the 42 products from the leading brands (Fritsch GmbH, Retsch, Eriez, DM 200 is used for grinding mediumhard, hard and brittle materials Thanks to its robust design it is suitable for usage under rough conditions in pilot plants and laboratories with the continuous consumption of highgrade ores, Ore mill, Ore grinding mill All industrial manufacturersAs the main equipment in iron ore pelletizing plants, a damp mill is mainly used for the damp grinding of iron ore to provide materials for the pelletizing disc It can deal with iron ore with a water content of 813%, not only increasing the surface area of the ore particles but also making the ore fully mixed and ground to shorten the whole pelletizing processDamp Mill – Ball Grinding Machine Iron Ore Pelletizing Equipment2018年4月5日 Explore essential rod mill design calculations with 911 Metallurgist EF3 – Diameter Efficiency Factor – using the base mill diameter of 244 meters (8′) inside liners, The mill diameter, low or high ratio of Rod Mill Design Calculations 911Metallurgist
.jpg)
Ball Mill Is The Key To Grinding Lithium Ore JXSC
4 天之前 Lithium ore ball mill The large discharge mine mouth design has stronger lithium ore processing capacity, which can be as high as 160t/h; 2 Due to its special design of the ore discharge plate, the ball mill has a large 2008年4月1日 Download Citation High efficiency ball mill grinding Some of the factors that need to be considered to increase the efficiency of ball milling grinding, are discussed Grinding efficiency can High efficiency ball mill grinding ResearchGateFigure 5 Startup of the LSPMSM SMH1732T motor with a filled ball mill after two hours of downtime: (a) active power, (b) current intensity, (c) voltage "Energy Efficiency Analysis of Copper Ore Ball Mill Drive Systems"Energy Efficiency Analysis of Copper Ore Ball Mill Drive SystemsHigh frequency screens have become more standardized and widely adopted in materials classification processes They allow efficient cuts and fines separations, which can provide high purity and precise sizing control of the product (for sizes of fine particles up to 007415mm) [1] Common industrial applications include dewatering of materials, processing of powder in coal, Highfrequency vibrating screens Wikipedia
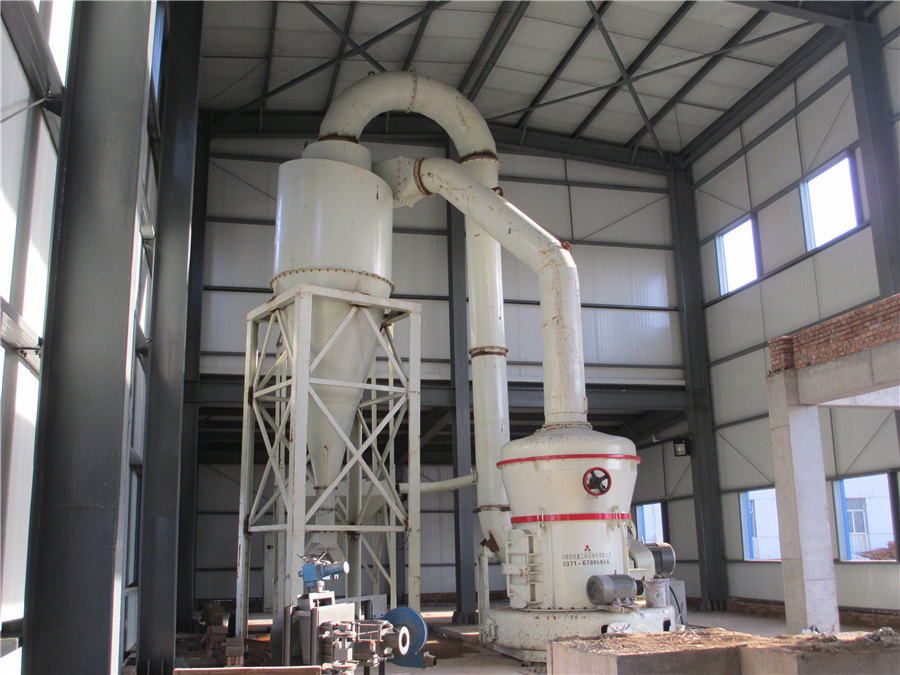
An investigation of performance characteristics and energetic
2020年8月12日 VRM has been widely researched in processing of cement (Ito et al 1997;Jorgensen 2005;Wang et al 2009, Ghalandari et al 2021), coal (Tontu 2020), iron ore (Reichert et al 2015), zinc ore (van 3 Figure 1: MYSRL mine showing Gold Mill as well as adjacent facilities YGM processes high grade gold ores at higher recoveries than heap leachingYANACOCHA GOLD SINGLE STAGE SAG MILL DESIGN, HighEfficiency Cyclone Micronizer Exhaust Fan Feeder Grind Air Inlet B Production System MICRONIZERS ENERGY REQUIREMENTS CAPACITY MILL 1 COMPRESSED AIR 2 SUPERHEATED 3 HP LBS/HR SIZE/DIA STEAM 2" 30 80 10 1/2 1 4" 55 145 15 2 40 8" 130 rotary action produces high reduction ratios and production rates for softto mediumhard MICRONIZER JET MILL Sturtevant IncHot Sale Good Quality Mining Machine Gold Ore Ball Mill Machine Gold Ore Rotary Ball Mill, equipment to process the stones from mountain, river, and mines In the past few decades, we have been focused on the design, research Sand Washer, Belt Conveyor, Raymond Mill, High Pressure Mill, High Efficiency Mill, Ultrafine Mill, Ball Hot Sale Good Quality Mining Machine Gold Ore Ball Mill
.jpg)
Magnetite Iron Ore Design Case Study ResearchGate
A theoretical design study for a for high capacity processing of a hard, fine grained silica rich magnetite ore, with several circuit options was carried out to assess the energy efficiency