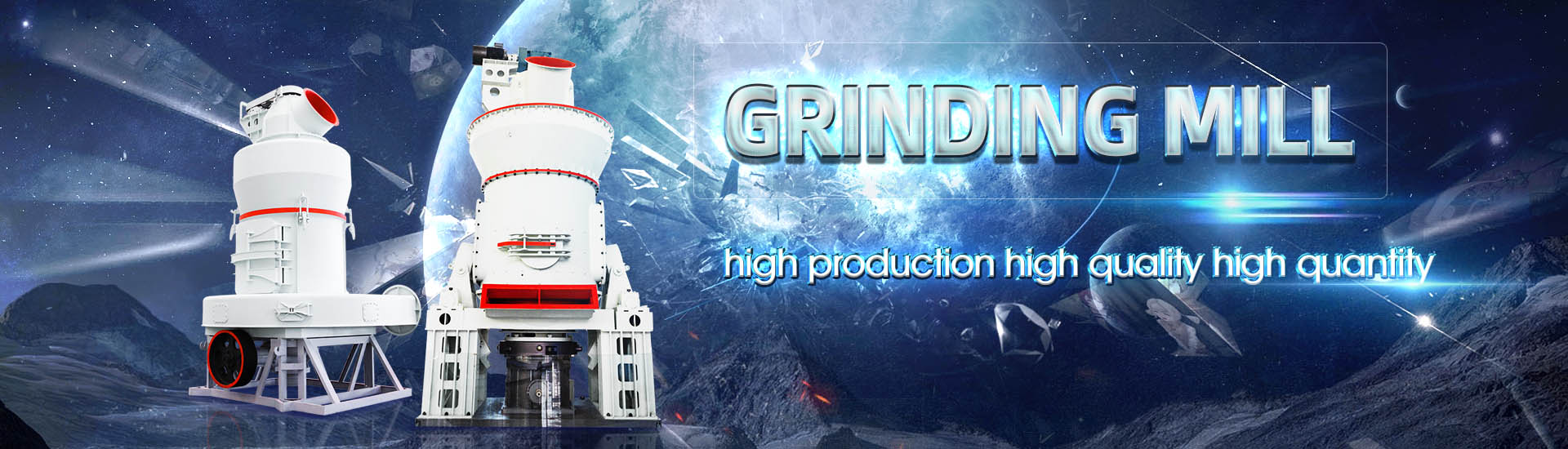
How much water slag does a 1.2 million ton iron smelting blast furnace produce every day
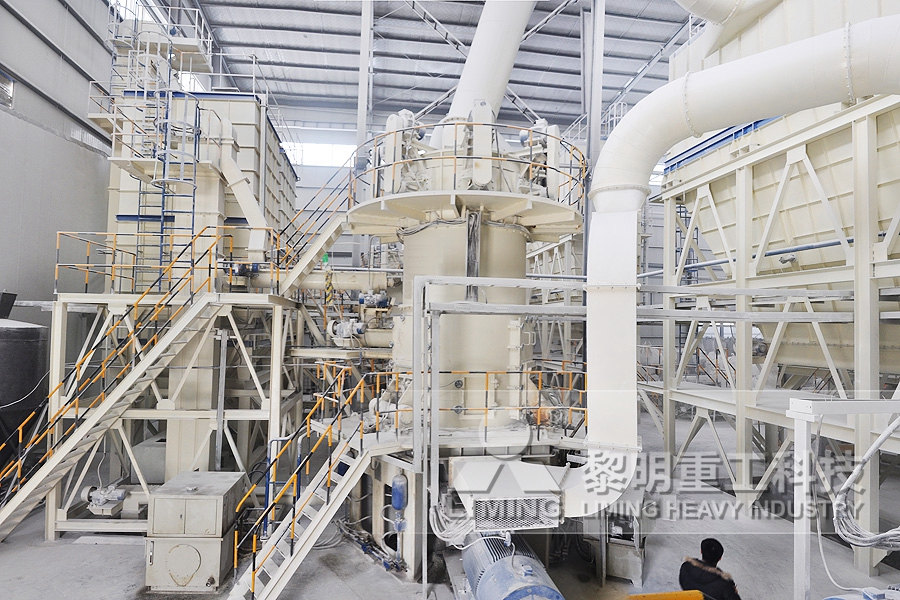
Blast Furnace Ironmaking SpringerLink
2023年10月6日 A large blast furnace has a slag content of 250–350 kg per ton of iron, and a small blast furnace has a slag content of 450–550 kg per ton of iron The main composition range of general blast furnace slag is: calcium oxide for 35–44%, silica for 32–42%, alumina for Flash smelting entails continuously blowing oxygen, air, dried particulate sulfide concentrate and silica flux into a 1300 °C furnace The principal objective of flash smelting is to produce molten Smelting Furnace an overview ScienceDirect Topics2023年7月21日 The specific heat capacity of slag is about 12 kJ/(kg°C), if the average value of the slag temperature is calculated at 1400°C, and the temperature of the recovered heat and Comprehensive utilisation of blast furnace slag Taylor Francis For typical iron ore grades (60% to 66%), a blast furnace will normally produce 025 to 030 metric ton (t) of slag per metric ton of crude or pig iron produced lowerthanaverage ore grades will 2018 Minerals Yearbook USGS Publications Warehouse
.jpg)
(PDF) Iron and Steel Slags ResearchGate
2017年3月5日 The physicochemical properties of four different types of iron and steel slags, including blast furnace slag, basic oxygen furnace slag, electric arc furnace slag, and ladle2022年10月20日 Iron and steel slags are rich in CaO, which can be used as CO2 adsorbents to achieve a maximum concentration of 04–05 kg CO 2/kg SS Blast furnace molten slag Application of iron and steel slags in mitigating greenhouse gas 2022年3月31日 Blast furnace slag (BFS) is produced in huge quantities by iron and steel companies, which pose a large major disposal challenge In 2013, global steel slag output was From waste to waste: iron blast furnace slag for heavy metal ions 2023年6月15日 For ironmaking blast furnaces less than 750 m 3, generally one iron notch is provided, and for large ironmaking blast furnaces, 2–4 iron notches are provided, and slag Ironmaking Blast Furnace SpringerLink
.jpg)
From Ore to Iron with Smelting and Direct Iron Reduction
2017年10月17日 While the blast furnace remains an important tool for ironmaking, newer technologies such as smelting and direct iron reduction are available to produce iron with Production of slag can be estimated based on typical slagtometal ratios, which are related to the chemistry of the ferrous feeds to the furnace For typical iron ore grades (60% to 66%), a blast 2019 Minerals Yearbook USGS Publications Warehouse2015年1月1日 Figure 173 and Table 171 show evolution of blast furnace dimensions from 1860 Between the years 1860 and 1960, the diameter of the furnace hearth increased from 09 to 8–9 m with production of 25 and 1500–2000 tons of hot metal per day, respectivelyFrom the 1960s to the 1980s, the hearth diameters have almost doubled, and the furnace volume and Recent developments in blast furnace ironmaking technologyModern blast furnaces produce more than 10,000 tonnes per day For general information about merchant pig iron, please visit the pig iron page Modern blast furnaces produce more than 10,000 tonnes per day Blast Furnace Process Pig iron blast furnace route International Iron
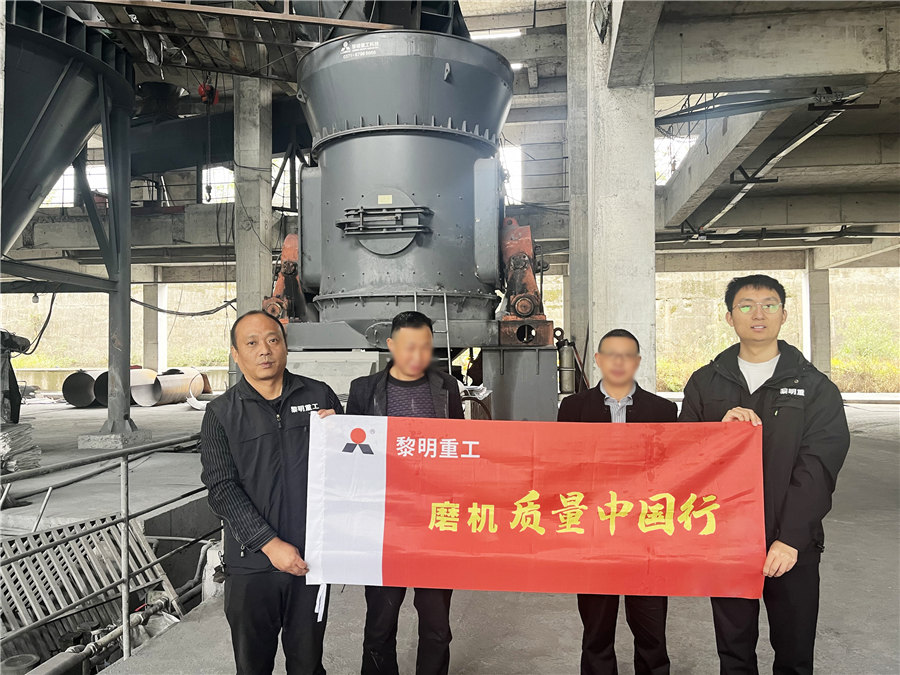
Application of iron and steel slags in mitigating greenhouse gas
2022年10月20日 Blast furnace slag (BFS) and SS account for 80 %–90 % of the total metallurgical slag Both are collectively called iron and steel slags (Wang et al, 2021c) In China, for every ton of pig iron and one ton of steel produced, about 06–08 t BFS and 015–025 t SS are manufactured, respectively (Zhang et al, 2020)2019年1月1日 In an integrated steel plant, wastes (including solid, liquid and gas) are generated for every ton of steel produced In India, almost 100 million tonnes of steel is produced every year, and along Recent trends in slag management utilization in the steel Iron ore consists of various oxides of iron (occurring as ironcontaining minerals) mixed with oxides of other metals (such as Al and Si) In the traditional route to produce steel, the ore is first ground and most of the noniron oxide minerals are removed through various means, a process referred to as beneficiationThe beneficiated ore is then made into various forms of prepared Overview of the Steel Production Process Springer2018年1月1日 Blast furnace slag (BFS) which is defined “as the nonmetallic product consisting essentially of silicates and alumina silicates of calcium and other bases, that is developed in a molten condition simultaneously with iron in a blast furnace” by ASTM C 12516 (2016) has been widely used in construction industry for more than 80 years When the mixture of ironore, Blastfurnace slag ScienceDirect
.jpg)
Sustainable and Comprehensive Utilization of Copper Slag: A
2023年4月21日 Annually more than 400 Mt of metallurgical slags are produced worldwide [1,2,3,4,5]From the annual Cu concentrate smelter production capacity, which is equal to around 21 Mt of copper metal in 2021, it can be estimated that more than 45 Mt of CUS were produced from primary sources assuming a slag to copper ratio of 22 [3, 4]Only 15% of the CUS cokemaking and iron ore preparation are described in Chapter 3 CO 2abatement from the different iron production routes, namely blast furnaces (BFs), direct reduction processes (which produce DRI) and the smelting reduction processes (which eliminate the need for coking and iron ore sinter plants) are covered in the following three chaptersCO 2 abatement in the iron and steel industry2021年11月16日 The article describes the concept of partially replacing the sinter in a blast furnace charge with extrusion briquettes to form the basis for sintering and briquetting synergy The comparability criteria for sinter and extrusion briquette (brex) properties and production parameters were analyzed along with a substantiation of the fundamental possibility of partially Sintering and Briquetting Synergy in Blast Furnace Smeltingtons, including 247 million tons of blast furnace slag and 101 million tons of converter slag [2] pressure water in contact with molten iron slag Slag disposal systems need to be shut down and dry pits installed to address slag discharge issues The mechanical granulation wheelComprehensive utilisation of blast furnace slag Taylor Francis
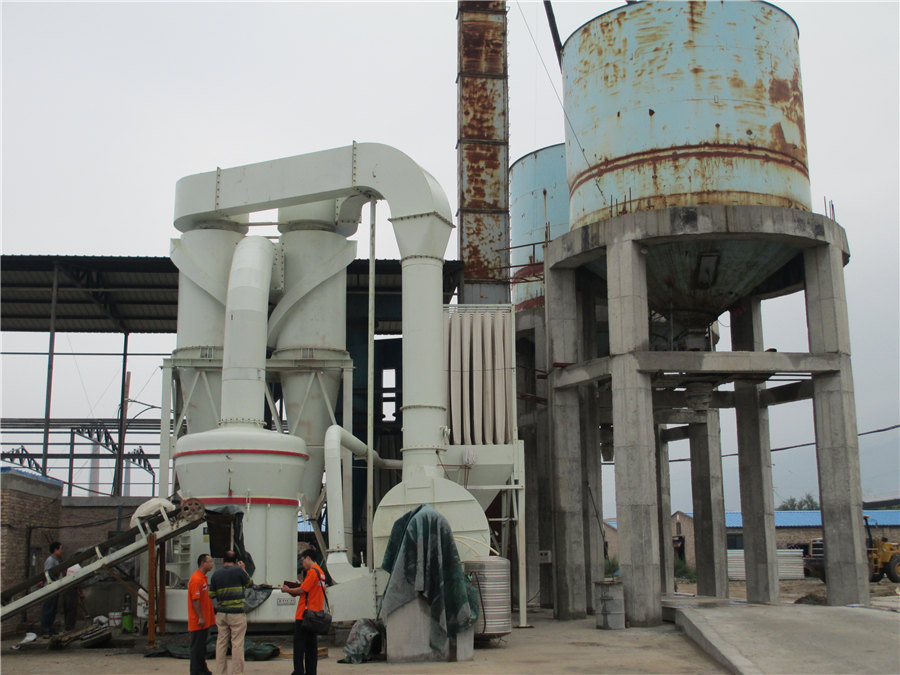
A Comprehensive Review on the Ground Granulated
2022年7月18日 Building manufacturing has played a significant part in the urbanization and industrialization that has occurred in recent decades Approximately 5–10% of global employment is provided by the construction 2021年12月20日 The majority of global steel is produced via the blast furnace–basic oxygen furnace (BFBOF) route, as shown in Fig 1, which reduces lump ore/agglomerates to pig iron using charged coke and injected fossil fuels in a blast furnace, and further converts pig iron to crude steel in a basic oxygen furnace The blast furnace ironmaking process is Hydrogen direct reduction (HDR) in steel industry—An 2017年10月17日 While the blast furnace remains an important tool for ironmaking, newer technologies such as smelting and direct iron reduction are available to produce iron with minimal byproduct generation and slagfree hot From Ore to Iron with Smelting and Direct Iron Steel is produced via two main routes: the blast furnacebasic oxygen furnace (BFBOF) route and electric arc furnace (EAF) route Variations and combinations of production routes also exist The BFBOF route produces steel using raw materials such as iron ore, coal, limestone and steel scrap About 75% of steel is produced using the BFBOF routeFact sheet Energy use in the steel industry
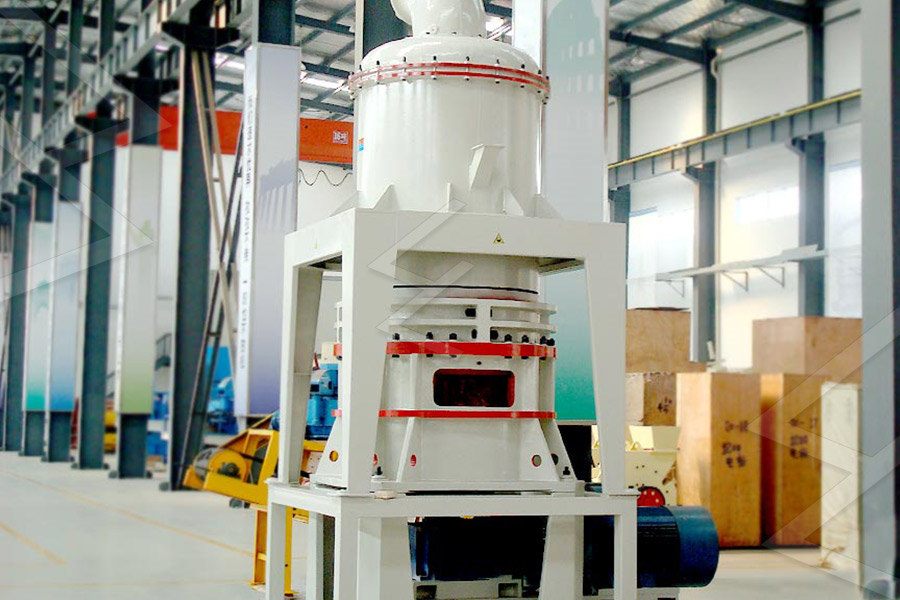
Guide to Modern Smelting Processes CED Engineering
Guide to Modern Smelting Processes – T09002 5 Iron Smelting: Iron smelting involves reducing iron ore, typically hematite or magnetite, in a furnace The high temperatures required (over 1500°C) posed significant challenges Early iron smelting was accomplished using charcoal fueled furnaces known as bloomeries2021年10月8日 BLAST FURNACE IRON MAKING (ANCIENT The blast furnace produces a slag resulting from the union of The present productivity of JSWS BF#1 is 35 Ton / m 3 / day with usage of max 62% BLAST FURNACE IRON MAKING (ANCIENT IRON MAKING) 2019年7月2日 Iron and steel making is one of the most intense energy consuming in the industrial sectors The intensive utilization of fossil carbon in the ironmaking blast furnace (BF) is related directly to Modern blast furnace ironmaking technology: potentials to 2017年10月10日 Figure 1 Drawing of an ironmaking blast furnace with hotblast stove Source: The German Steel Federation (WV Stahl) In order to make steel, iron must be extracted or won from iron ore Blast furnacing, smelting and direct iron Ironmaking 101 – From Ore to Iron with Blast Furnaces
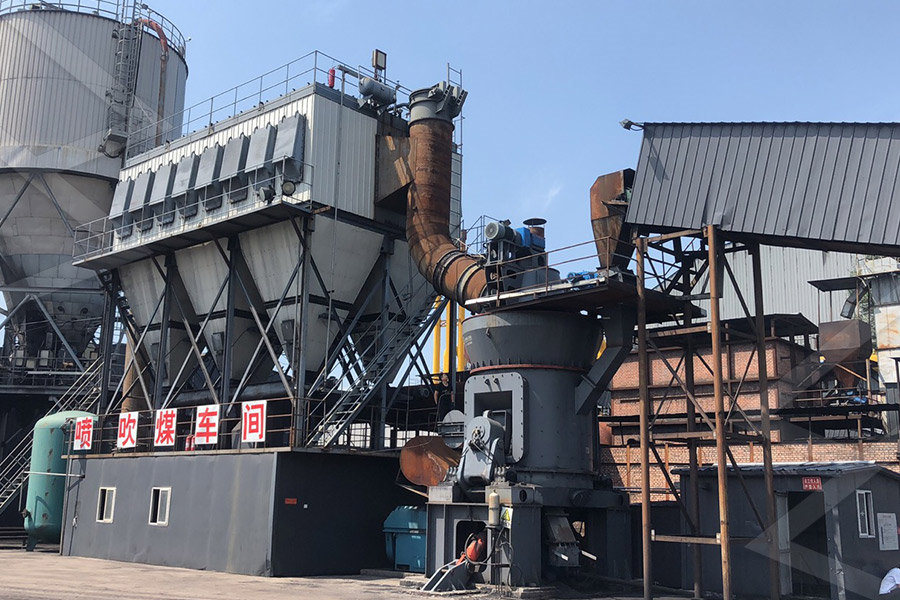
Blast Furnace Process an overview ScienceDirect Topics
Blast Furnace Slag (BFS) is a byproduct of the reduction stage, in which iron ore is converted into pig iron About 300 kg of BFS is produced per ton of pig iron [16] During the blast furnace process , limestone (CaCO 3 ) is added to removing impurities: silica (SiO 2 ), phosphorus pentoxide (P 2 O 5 ), calcium sulfide (CaS), magnesium oxide (MgO) and alumina (Al 2 O 3 ), Experience and lessons learned Michele Laraia, in Beyond Decommissioning, 2019 6224 Blast furnaces “A blast furnace is a large structure in which iron ore is heated under pressure so that it melts and pure iron metal separates out and can be collected “(Collins Dictionary) The heritage value of blast furnaces built before 1900 has been recognized already for a long time, and Blast Furnace an overview ScienceDirect TopicsThe use of groundgranulated blast furnace slag (GGBFS) or granulated blast furnace slag (GBFS) in concrete can be documented circa 1900 where slag was produced as “slag cement”; in the late 19th century and early 20th century, a significant portion of the cement in the United States sold as “portland cement” was actually “slag cement” (Eckel, 1902, 1905)Ground Granulated Blast Furnace Slag ScienceDirectCement additives Johannes Fink, in Petroleum Engineer's Guide to Oil Field Chemicals and Fluids (Third Edition), 2021 Furnace slag A furnace slag cement slurry can have a density of 15001600 kg m −3A combination of silica flour and furnace slag may be used to achieve service temperatures exceeding 200 °C [100]A gas may be suitable as a foaming agent [101]Furnace Slag an overview ScienceDirect Topics

What Are the Uses of Blast Furnace Slag (BFS)?
2019年12月12日 When pig iron is smelted in a blast furnace, the flux is added to the raw materials from the blast furnace in addition to iron ore and fuel (coke) When the furnace temperature reaches 14001600 ℃, the lime in the flux 2022年9月25日 Compared with other copper smelting slag treatment technologies such as acid leaching and smelting, microwave fluidization roasting technology does not produce greenhouse gases such as carbon dioxide, nor does it have the characteristics of chemical corrosion and high energy consumption, so it has the advantages of clean and efficient (Yuan et al, 2022)Extraction and separation of copper and iron from copper smelting slag Steelmaking slag, or steel slag, is a byproduct from the production of steel during the conversion of hot metal to crude steel in a basic oxygen furnace, or during the melting of scrap in an EAFThe slag is generated as a melt and is a complex solution of silicates and oxides that solidify upon cooling 11 Depending on the specific steel production process, three different types of steel Steelmaking Slag an overview ScienceDirect Topics2024年7月5日 For each ton of copper metal produced worldwide, about 22–30 tons of slag is produced, estimated to be approximately 40 million tons of slag generation annually (J P Wang Erdenebold, 2020), with the content of iron reaching 45%; the copper slag has potential to produce approximately 268 million tons of Fe annually (Heo et al, 2013)Copper Slag as a Source of Iron: An Overview SpringerLink
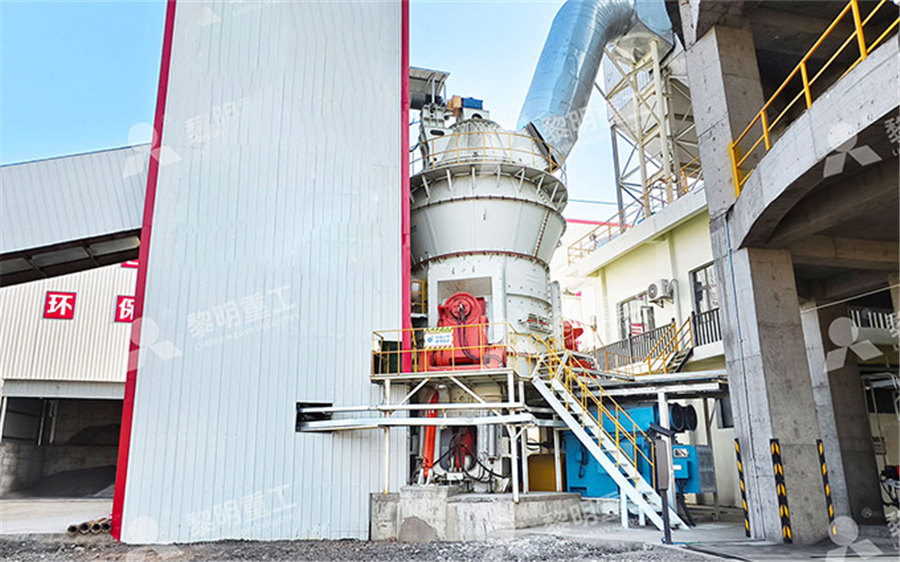
Critical review of applications of iron and steel slags for carbon
2019年1月8日 Carbon dioxide (CO 2) is considered the most common and abundant GHG in the atmosphere that is generated as a result of various natural and industrial processes (Figs 1, 2)Power plants and manufacturing plants are the major sources with steel industry accounting for 3–4% of the global GHG emissions (Yu and Wang 2011)The current CO 2 level in 2020年10月29日 The primary energy consumption and greenhouse gas emissions from nickel smelting products have been assessed through case studies using a process model based on mass and energy balance The required primary energy for producing nickel metal, nickel oxide, ferronickel, and nickel pig iron is 174 GJ/t alloy (174 GJ/t contained Ni), 369 GJ/t alloy (485 Energy Consumption and Greenhouse Gas Emissions of Nickel Carbon combines with the oxygen in the iron ore, producing metallic iron and a carbonrich process gas, according to the following simplified chemical reaction: 2Fe 2 O 3 + 3C > 4Fe + 3CO 2 It is also possible to reduce iron ore using hydrogen instead of carbon; in this case the waste gas produced is water, as per the following reactions:Fact sheet Hydrogen (H2)based ironmaking2020年4月1日 Iron and steel manufacturing is the most energy and carbonintensive industry in the world (Quader et al, 2015) as both the iron and steel making sectors have not yet attempted to fully incorporate renewable energy sources into their productionThey are highly dependent on fossil fuels and release substantial amounts of CO 2 during normal operations (Helle, Huitu, Basic oxygen furnace slag: Review of current and potential uses
.jpg)
Energy Use in US Steel Manufacturing
From the data in Table 1 and Fig 3 it is apparent that the production of hot metal or pig iron is the most energy intensive process for steel production at roughly 135 × 10 9 joules per ton (1000 Kg) of pig iron produced The basic oxygen combination of a blast furnace and basic oxygen furnace Some SRI processes can produce steel directly Direct Fig 1 Iron and steel production technologies [2] IRON PRODUCTION Blast Furnace (pig iron) – Blast furnace (Figure 2) is a process for producing liquid raw iron by smelting pellets or sinter in a reducing environment The end © IEA ETSAP Technology Brief I02 May 2010 etsap Iron 2022年1月17日 The power is consumed by the use of electricity, steam, oxygen, blast, water, etc The power consumption required for preparing 1 m 3 of O 2 is 03kWh and that required for 1 m 3 of CO 2 is 032kWh During the actual production data of the blast furnace, the CO 2 emission generated per ton of iron when \(f{\text{CO2}}\) = 0 is shown in Table 13CO2 Emission of CO2 Injection into Blast Furnace SpringerThe principal copper ore mineral is chalcopyrite (CuFeS 2), which is commonly smelted to yield a matte containing ∼50% copperIn the presence of silica flux, iron is selectively oxidized to a slag Figure 14 shows a PSD for the Cu–Fe–S–O system at 1 atm SO 2 as a function of temperature (Rosenqvist 1978)Unlike the system for lead, the copper and Cu 2 S melts are nearly Copper Smelting an overview ScienceDirect Topics
.jpg)
Chemistry of the Ironmaking by Blast Furnace Process
2013年11月22日 Chemistry of the Ironmaking by Blast Furnace Process satyendra; and 400 kgs of carbon react in this manner for every ton of hot metal produced This reaction is the main source of heat for the smelting There is an adjustment in the silica content of the slag, iron oxide can be reduced from it and it can absorb sulphur 2021年12月3日 Copper slag is generated when copper and nickel ores are recovered from their parent ores using a pyrometallurgical process, and these ores usually contain other elements which include iron Environmental and Socioeconomic Impact of Copper SlagA 2019年7月19日 Iron oxides are reduced in the blast furnace (Fig 41), and the resulting material is meltedBlast furnaces capacity is 100–5000 m 3 covering the 70% of the global steel production Iron ores, sinter or pellets, coke, and lime are introduced into the blast furnace from the top; the hot compressed air is fluxed from tuyeres at the lower section of the furnaceBlast Furnace: Most Efficient Technologies for Greenhouse CHAPTER ONE THE ROLE OF MATHEMATICAL MODELS IN THE ANALYSIS, CONTROL, AND MANAGEMENT OF BLAST FURNACE SMELTING 11 The use of mathematical modeling in the development and improvement of pyrometallurgical processes of Mathematical Modeling of the Blast Furnace Process
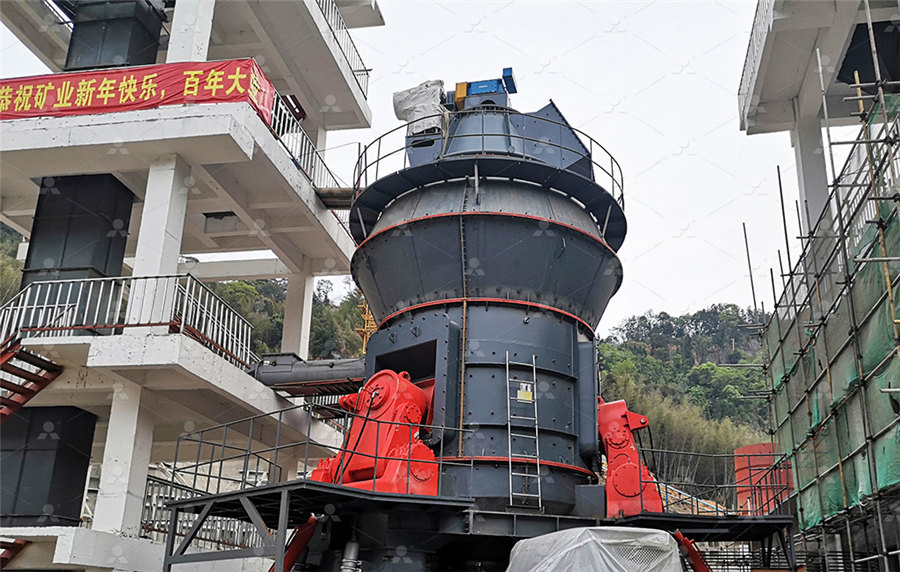
Steelmaking CO2 carbon dioxide emissions by process step
GHG emission levels in iron and steel production The main process steps that generate carbon dioxide in iron and steelmaking are the production of coke, and the production of hot metal in the blast furnace Ancillary facilities such as power plants also produce large volume of CO22020年3月3日 The hydrogen, which is formed by the reaction (), and any unreacted water vapour join the gas stream and pass upwards through the furnaceThe reaction is endothermic, and it may be thought that the presence of water vapour in the blast would be detrimental to the processAccording to the reaction (), one volume of oxygen produces two volumes of CO gas; Blast Furnace Reactions SpringerLink