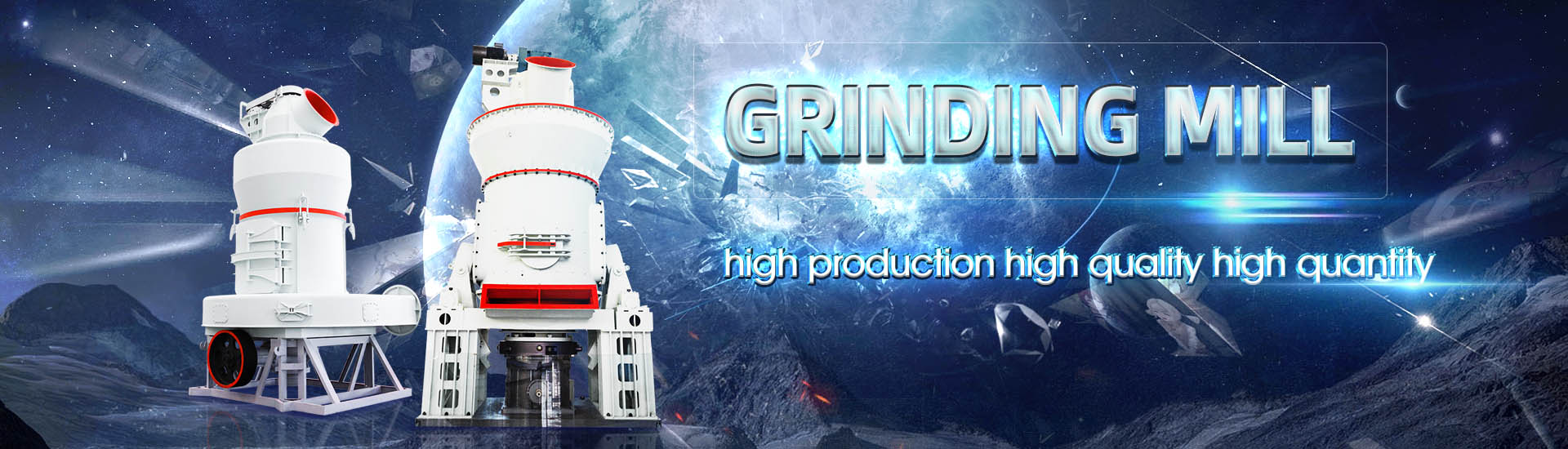
How many pieces does a 3400d raw material vertical mill grinding disc consist of
.jpg)
Vertical roller mill for raw Application p rocess materials
Vertical roller mills are adopted in 20 cement plants (44 mills) in Japan In the vertical roller mill which is widely used in the raw material grinding process, raw materials input grinding table are crushed and pulverized on it and transported to separator by kiln exit gas introduced into the There are two main layouts for a vertical roller mill (VRM) system, with product collection in cyclones or a filter The power consumption of a VRM is Vertical Mill Calculations PDF Mill (Grinding) Nozzle The core elements of these plants are the Loesche vertical mills for drygrinding the abovementioned grinding stock Loesche has developed and built the largest and most efficient PROCESS OPTIMISATION FOR LOESCHE GRINDING PLANTSThis document provides a technical agenda for optimizing the performance of vertical raw mills It aims to help plant teams manage mill performance through structured approaches, Lafarge TA Grinding VRM v1 (Final) PDF Mill (Grinding) Dam
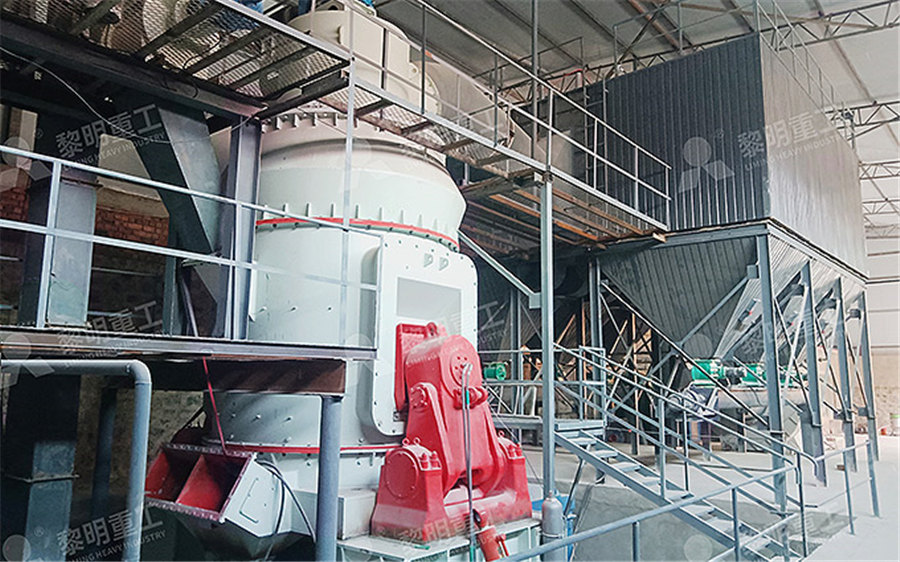
2 µm 5 µm Loesche
slag in roller grinding mills (vertical airswept grinding mills) is a technology introduced by Loesche The first use of a Loesche mill, with a grinding track diameter of only 11 metres, was used as We at Pfeiffer can provide the whole range of grinding, separating, and drying equipment as needed to make your cement line work economically: for example, with our proven vertical PFEIFFER MILLS FOR THE CEMENT INDUSTRYThe different grinding processes of vertical mills compared to tubular ball mills have led to the development of a new generation of Cement Grinding Additives These products have been Technical Notebook CEMENT ADDITIVES FOR VERTICAL MILLSMVR vertical roller mill from Gebr Pfeiffer with patented multiple drive system MultiDrive® for the highest throughput rates and permanent plant availabilityCement mills and raw mills for high throughput rates Gebr Pfeiffer
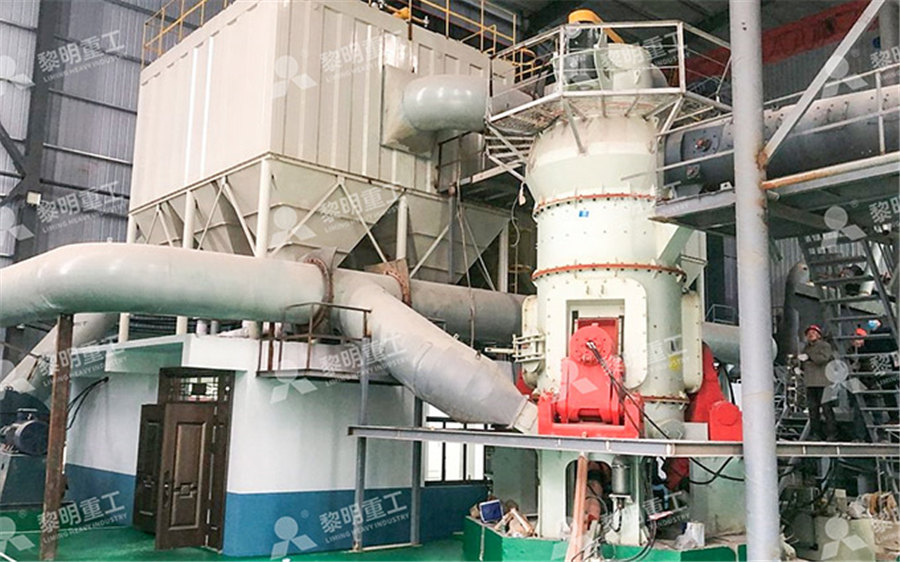
PFEIFFER VERTICAL MILL WITH MULTIDRIVE MORE POWER
Pfeiffer MVR mills with MultiDrive® // When grinding raw material, cement and granulated blastfurnace slag, what’s the point? Maximum throughput and utmost technical availability! This is The grinding of the finished cement consumes approximately one third of the total electrical energy of a cement plant Vertical Roller Mills (VRM) have a clearly higher energy efficiency SikaGrind® for vertical roller millsGrinding disc diameter(mm) Roller diameter(mm) Feeding size(mm) Production capacity(t/h) Main motor power(Kw) Disc rotation speed (r/min) Weight (t) LM mill: LM0806: 800: 600: the circulating material out of the vertical raw mill is fed Vertical raw mill Cement Plant2015年4月9日 Grinding Mills and Their Types satyendra; April 9, 2015; 12 Comments ; autogenous grinding, ball mill, grinding mills, hammer mill, rod mill, roller mill, SAG,; Grinding Mills and Their Types In various fields of the Grinding Mills and Their Types – IspatGuru
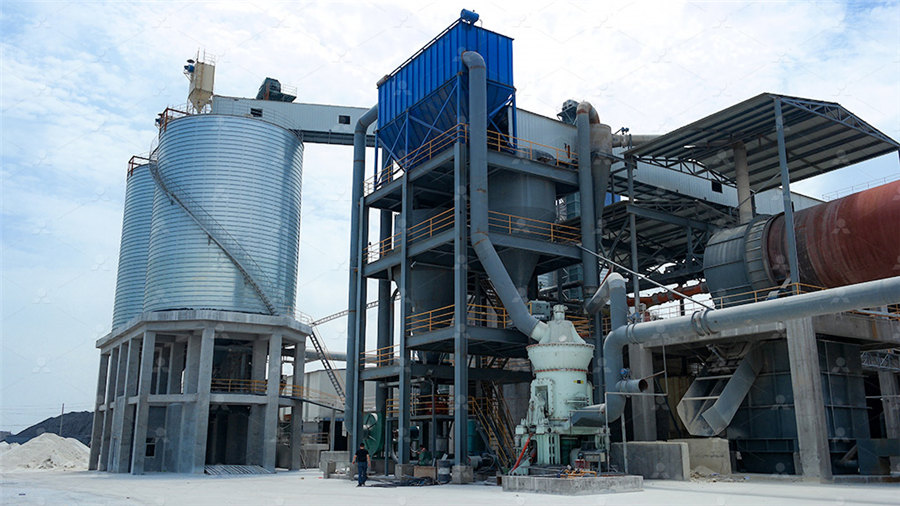
quadropol® thyssenkrupp Polysius Grinding
In addition, the raw material grinding process will be supported by a QMR² 48/24 For the 4,000 tons per day kiln line Shiva Cement Ltd contracted a quadropol® vertical roller mill for grinding pet coke with a QMK² 32/16 The same mill size 2016年9月1日 The results demonstrated that the VRM unit consumes around 81% (975 kWh/t of raw materials), and 36% (58 kWh/t of raw materials) more energy to grind raw material than the IBAT unit and domestic Operational parameters affecting the vertical roller mill 2021年1月1日 Stacking Reclaiming of Raw material: Swing type stacker Reclaimer: Limestone other raw material are stored in open area into a longitudinal storage unit called stockpile through Stacker These are then extracted transversely from the stockpile through reclaimer: 3: Raw Meal Grinding Homogenization: Grinding Mill Vertical Roller Mill Review on vertical roller mill in cement industry its For the cement industry the ball mill was really an epochmaking breakthrough as for almost 80 years it was the predominant mill for grinding of raw materials and coal, and still today is the most used mill for cement grinding Over the last three decades the vertical roller mill has become the preferred mill for grinding of raw materialsCement grinding Vertical roller mills VS ball mills
.jpg)
A Survey and Analysis on Electricity Consumption of Raw Material Mill
2021年1月22日 In the whole process of cement production, the electricity consumption of a raw material mill accounts for about 24% of the total Based on the statistics of the electricity consumption of the raw 2020年6月14日 Identify your raw material and its source If your metal grinding vendor has to provide the raw material for your parts, that increases their costs and, in turn, your quoted price However, if you can provide the raw material, that puts you in control of the sourcing and how much you want to spendPrecision Metal Grinding Metal Cutting CorporationWet Grinding: Open circuit Ball mill or closed circuit Ball mill Dry Grinding: Open circuit Ball mill, closed circuit Ball mill, vertical roller mill, Roll Press or Roll press in circuit with ball mill However, it would be seen that the most significant process and types used for raw material grinding operations in modern cement industry are Raw Material DryingGrinding Cement Plant OptimizationRead this indepth blog to learn about the working principle of Vertical Grinding Mill, its application, and its advantages +91 226796 9655 These mill crushers consist of a reducing rotating mill for size reduction The grounded raw material is then carried through the air from the blower into the Analyzer Machine for screeningVertical Grinding Mill: How it Works, Application And Advantages
.jpg)
Cement Vertical Mill Vertical Grinding Mill
What Is Cement Vertical Mill The cement vertical mill is a type of grinding equipment that merges fine crushing, drying, grinding, and powder separating into a single, which simplifies the production process and has many irreplaceable Low energy, the powder consumption of vertical mill is 20%30% less than that of ball mill With the incensement of moisture of the raw material, the powder consumption will decrease obviously The vertical mill saves 30%40% of Vertical Cement Mill2017年9月11日 Due to the compact design and material transportation system of vertical roller mills (VRM), some important streams (total mill feed and discharge, dynamic separator feed and reject) remain in the Performance Evaluation of Vertical Roller Mill in The document discusses optimization and operation of vertical roller mills (VRMs) Key points include: 1) Continuously monitor and adjust process parameters to find the optimum operating conditions of highest capacity and lowest power consumption 2) Relevant process parameters to monitor include product rate, fineness, classifier speed, grinding force, power consumption, air Optimization of Vertical Raw Mill Operation PDF
.jpg)
Energysaving and Efficient Vertical Roller Mill Fote Machinery
A vertical roller mill, also known as a vertical grinding mill or vertical mill, is a comprehensive grinding equipment integrating crushing, drying, grinding, grading, and conveying Vertical grinding mills can be widely used in electric power, metallurgy, construction, chemical industry, and other industries to make powder, especially for materials such as cement clinker, coal 2016年10月5日 1 Introduction Cement is an energyintensive industry in which the grinding circuits use more than 60 % of the total electrical energy consumed and account for most of the manufacturing cost []The requirements for the cement industry in the future are to reduce the use of energy in grinding and the emission of CO 2 from the kilns In recent years, the production EnergyEfficient Technologies in Cement Grinding IntechOpenStep 9: Hire feed mill workers and other personnel You will need to hire and train feed mill workers The workers will be responsible for the daytoday operations of the business To manage the feed mill, you will need to hire and train managers who will be responsible for the daily operations of the feed millA Beginner's Guide to Setting Up a Feed Mill Livestocking2017年6月2日 Autogenous grinding (AG) and semiautogenous grinding (SAG) mills use the material to be ground as the grinding media Autogenous grinding mills use larger rocks to impact and break smaller rocks as the mill rotates Semiautogenous mills are basically the same autogenous mills, but with the addition of balls, similar to those in ball millsHow it Works: Crushers, Grinding Mills and Pulverizers

A comparison of wear rates of ball mill grinding media
2016年1月1日 One of the most popular milling machines is the cement mill, which is used to crush raw materials such as lime, silicate, alumina and iron oxide using grinding balls [3]2014年5月1日 The specific energy consumptions of the grinding equipment and the standard bond work indexes, used 100μm screen, of raw materials are given belowCircuitBond work index (kWh/t)Specific energy (PDF) Matrix Model Simulation of a Vertical Roller Mill After the cement raw material is crushed, it will be sent into the raw mill for further grinding until a certain degree of fineness is reached, and then enter the clinker calcination process From the production experience of many cement plants, Raw Mill – Raw Mill In Cement Plant AGICO Cement 04 Vertical Roller Mills Free download as Powerpoint Presentation (ppt), PDF File (pdf), Text File (txt) or view presentation slides online The document discusses vertical roller mills (VRM) which are used to grind raw meal in the 04 Vertical Roller Mills PDF Mill (Grinding) Turbine
.jpg)
OK™ Raw and Cement Mill
The OK™ Mill was originally designed for cement grinding In 2017 we released the OK™ vertical roller mill for raw materials grinding The OK™ Mill’s modular design comes with unique flexibility, showcasing parts commonality, where spare parts can be shared between vertical roller mills regardless of size and applicationpage 07 3 principles of vertical grinding systems page 07 31 vertical mill components page 07 32 how does a vertical mill work? page 08 4 a new generation of grinding additives: maga/vm and mape/vm page 08 41 mill output increase page 09 42 quality and water demand optimisation page 09 5 the mapei dosing lance page 11 6 productsTechnical Notebook CEMENT ADDITIVES FOR VERTICAL MILLSVertical Roller Mill Summary Free download as Powerpoint Presentation (ppt / pptx), PDF File (pdf), Text File (txt) or view presentation slides online Ball mill vs vertical mill Operations Structure of a vertical mill Working Process Components Dam Ring Armour Ring Louver Ring Grinding Table Rollers Separators Maintenance Performance ImprovementVertical Roller Mill Summary PDF Mill (Grinding) Scribd2012年6月1日 The feed material is typically composed of the BFRs and the catalyst, both in powder form As the cylinder starts to rotate, the grinding balls inside the cylinder crush and grind the feed Grinding in Ball Mills: Modeling and Process Control
.jpg)
Grinding Process Optimization Featuring Case Studies and
raw material grinding, a modular vertical roller mill with 5 m table diameter and 4 rollers was added The existing kiln systems were partly modernized, one kiln system was replaced by new system 2020年7月1日 There are two main categories of milling machines in a common machine shop: vertical mill and horizontal mill, designed in different structures and for a variety of production use In this article, follow us to learn about the horizontal milling machine definition, features, construction, and workingHorizontal Milling Machine Basics: Definition, Features, 2024年3月16日 A vertical coal mill is a type of industrial milling equipment used to crush and grind coal into powder for use in thermal power plants and the cement industry, including power consumption, grinding efficiency, and material fineness, How Does a Raw Mill Work in a Cement Industry February 23, 2024 How Does a Vertical Coal Mill Work Coal Grinding Mill In 2021年1月16日 Disk Surface Grinding Machine Double Disc Surface Grinding Machine 1 Horizontal Spindle Surface Grinder (with Reciprocating Table) Your Horizontal Spindle Surface Grinding Machine consists of a base on which a Surface Grinder Types of Grinders How They Work
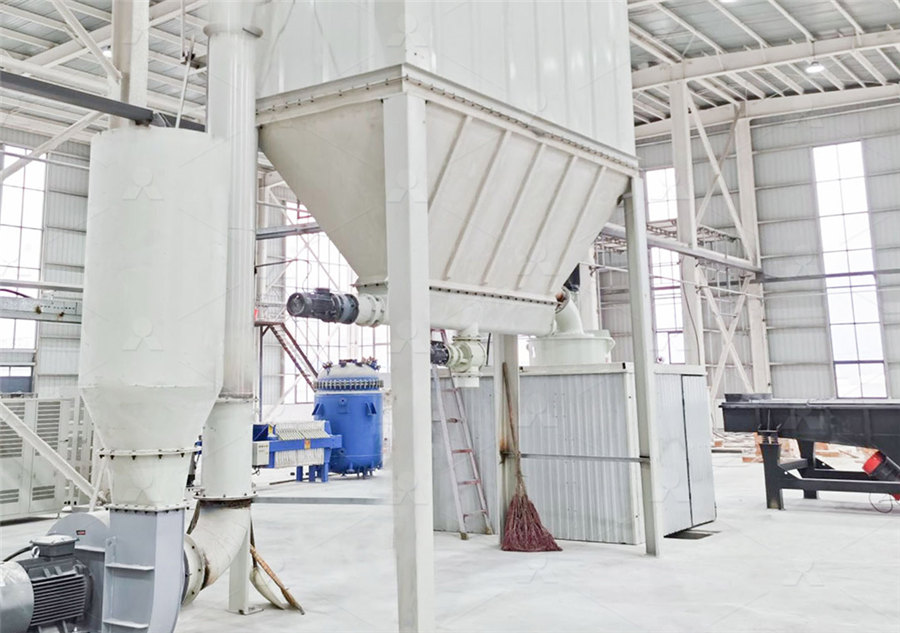
Vertical Roller Mill Summary PDF Mill (Grinding) Scribd
Vertical Roller Mill Summary Free download as PDF File (pdf), Text File (txt) or view presentation slides online Ball mill vs vertical mill Operations Structure of a vertical mill Working Process Components Dam Ring Armour Ring Louver Ring Grinding Table Rollers Separators Maintenance Performance ImprovementVertical raw mill is important equipment widely used in the cement raw meal (cement raw materials) grinding section of the cement production process in cement plantBecause the vertical raw mill is the use of roller grinding principle Vertical Raw Mill for Cement Raw Meal Grinding in Vertical roller mill for cement grinding [13] VRM shown in Figure1 uses hydraulically hard Product transport volume Grinding aid injection Composition of raw material Temperature after the mill Hot gas Grinding roller wear Mill vibrations Fresh air Figure2 VRM control classification [42]PROCESS CONTROL FOR CEMENT GRINDING IN VERTICAL ROLLER MILL 2022年6月24日 Ni J, Yang Y, Wu C Assessment of waterbased fluids with additives in grinding disc cutting process J Clean Prod 2019; 212: 593–601 Crossref Imyim A, et al Coprocessing of grinding sludge as alternative raw material in portland cement clinker production J Appl Sci 2010; 10(15): 1525–1535 Crossref Google Scholar 211A comprehensive review on the grinding process: Advancements
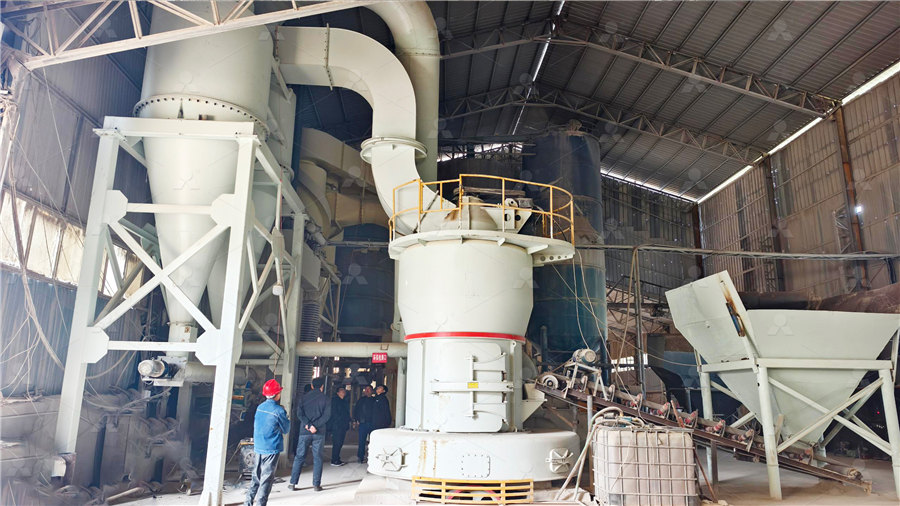
2 µm 5 µm Loesche
a Loesche mill, with a grinding track diameter of only 11 metres, was used as long ago as 1935 However, the breakthrough in grinding this type of material on the vertical roller mill did not take place until the beginning of the 1990’s 1935 The first Loesche mill for grinding cement clinker, an LM 11, was commissioned in Joao Pessao, BrazilRaw material: crushing, jaw crushing, hammer crushing, etc Raw material conveying: hoists, belt scales, buffer bins, starshaped feeding valves, screw conveyors, etc Superfine grinding and classification: Superfine vertical grinding mill main machine and multirotor powder separator: Finished product collection: Air box pulse bag filterCLUM Ultrafine Vertical Grinding Mill2022年5月31日 The rotating speed of the millstone is 60 rpm and the raw material is limestone Table 1 The geometrical and operational parameters used in the experiments Parameter Value; Research of iron ore grinding in a vertical rollermill Miner Eng, 73 (2015), pp 109115 View PDF View article View in Scopus Google Scholar Analysis of vertical roller mill performance with changes in material 2024年1月11日 Verticalspindle (wheelface) grinders: Utilizing the wheel’s face for grinding round, flat surfaces 3 Disc grinders: Employ a larger contact area between the disc and workpiece, suitable for metallic and nonmetallic substances 4 Doubledisc grinders: These doubledisc grinders work simultaneously on both sides of a workpieceSurface Grinding: A Guide to the Process and Precision okdor
.jpg)
(PDF) CEMENT RAW MATERIAL GRINDING ; VERTICAL ROLLER MILL OPERATION
2018 In this chapter an introduction of widely applied energyefficient grinding technologies in cement grinding and description of the operating principles of the related equip‐ ments and comparisons over each other in terms of grinding efficiency, specific energy consumption, production capacity and cement quality are given