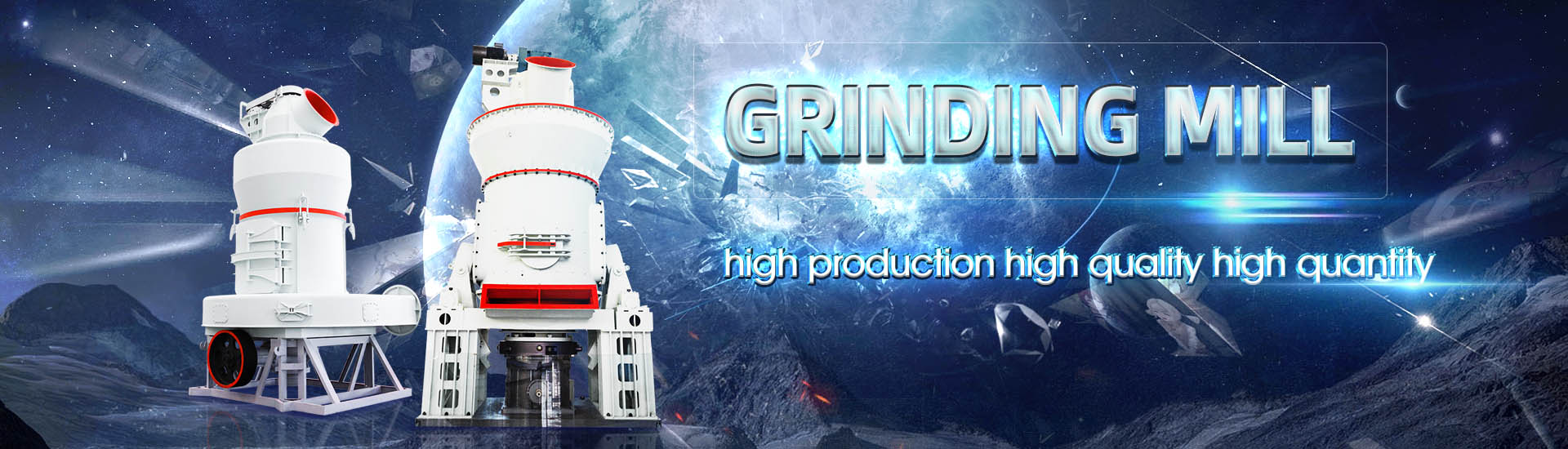
How much is the smelting waste slag of one cubic meter of limestone crusher
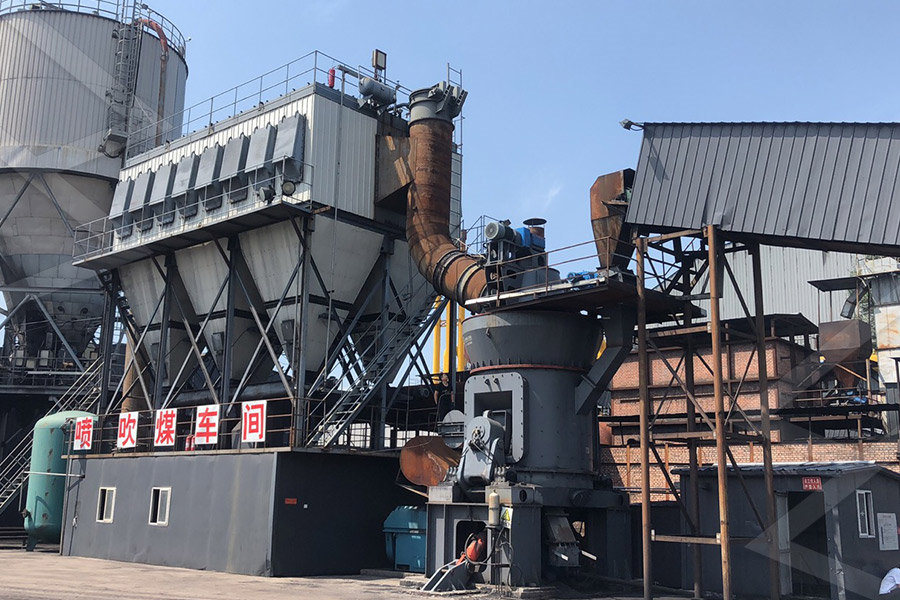
(PDF) Recycling and environmental issues of
2004年1月1日 The activity coefficient of SbO15 (1) in the basic slag of high sodaratio varies from 1 to 0001 depending on oxygen potential2023年4月21日 Annually more than 400 Mt of metallurgical slags are produced worldwide [1, 2, 3, 4, 5] From the annual Cu concentrate smelter production capacity, which is equal to around Sustainable and Comprehensive Utilization of Copper Slag: A2023年8月1日 Usually, the production of 1 ton of Cu is associated with the generation of around 22 t of slag [75] The global production of copper slag from the smelters is about 211 Million A comprehensive review on the recovery of copper values from 2022年4月1日 Copper slag waste is considered a potential world resource owing to the huge amounts being produced annually worldwide which contain significant amounts of valuable The potential for copper slag waste as a resource for a circular
.jpg)
Environmental and Socioeconomic Impact of Copper
2021年12月3日 It is estimated that 22–3 tons of copper slag is generated per ton of copper produced, and this waste is mostly disposed of near smelter sites [5, 6]2021年8月4日 The most recent European statistics for 2018 indicate that 192 Mt of BF slag and 157 Mt of slag from steel production were produced in Europe 3 For nonferrous metal CHAPTER 1: Introduction: Metallurgical Slags Royal Society of 2016年7月29日 One of the most important goals of copper slag metallurgy is to minimize copper losses to slag from entrained Cu droplets during the smelting of copper concentrate, 3 often Slag Metallurgy and Metallurgical Waste Recycling JOMConsidering the overall slag forming system and reaction temperature, CaO, SiO 2 and Al 2 O 3 are the major components in the waste slag so only the iron oxides would be reduced After modifying the chemical composition of the slag, their approximate positions of various slags present in the CaO SiO 2Al 2 O 3Characterization and Recovery of Valuables from Waste Copper Smelting Slag
%3C1PGHL[2}HK_]YT.jpg)
Basics of slag production Article on the slag industry from Global Slag
2011年10月27日 Slag from the production of ferrochrome is also included here; this material is produced in substantial tonnages and the main use of ferrochrome is in the steel industry Slags also arise from other processes, particularly the smelting of nonferrous metals, but these materials can be very different and each needs to be studied individually2020年8月19日 The adiabatic reaction to be considered in this zone of the blast furnace (Fig 611), where the smelting of the ferric charge, the direct reduction reactions (with coke) with the corresponding mass transfer from the slag to the metal, and the partial combustion of the carboncoke to carbon monoxide take place, will be the next one (volumetric composition of the air: Production of Iron in the Blast Furnace SpringerLink2021年5月1日 Slag 1: Flash smelting slag from Almalyk coppersmelting plant, Uzbekistan (Starodub et al, 2016); Slag 2: cleaning of electric furnace slag from Tongling Nonferrous Metals Group Holding Co, Ltd, China (Guo et al, 2016b); Slag 3: Converter slag from Tongling Nonferrous Metals Group Holding Co, Ltd, China (Guo et al, 2018a); Slag 4: Slowcooled slag Comprehensive review on metallurgical recycling and cleaning of copper slag2006年4月27日 In addition, according to Tsaimou et al [27], the presence of fayalite implies the commonly used direct smelting method operated at more than 1100°C [8](PDF) Regional variation in bloomery smelting slag of
.jpg)
The role of slag modifiers on the selective recovery of cobalt and
2002年11月1日 The effect of TiO 2 on cobalt, iron and copper recoveries (graphite addition) Molten slag is carried outside and poured into a dump The general term slag may be a byproduct or coproduct of smelting (pyrometallurgical) ores and recycled metals depending on the type of material being produced [1] Slag is mainly a mixture of metal oxides and silicon dioxideBroadly, it can be classified as ferrous (coproducts of processing iron and steel), Slag Wikipedia2021年2月8日 Although zinc smelting activity was completely stopped in 2004 An enormous amount of waste slag produced during the smelting was stacked in many slag sites In 2012, a governance measure with the selected plant, such as sophora japonica, sycamore tree, and ryegrass, was used to revegetate the Zn slag waste siteEffects of Zinc Smelting Waste Slag Treated with Root Organic Acids 2021年12月3日 All content in this area was uploaded by Gwiranai Danha on Dec 03, 2021Environmental and Socioeconomic Impact of Copper SlagA
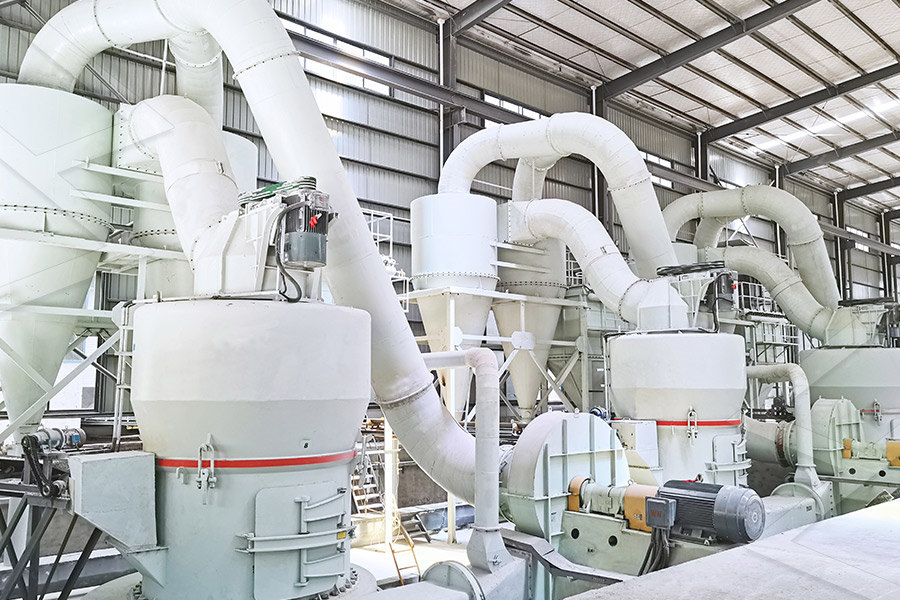
Characterization and Recovery of Copper from Converter Copper Slag
2018年8月1日 Characterization of Copper Slag From Table I, the contents of copper (Cu) and sulfur (S) are 449 and 053 pct, respectively, with a Cu/S ratio of 847This value does not match the Cu/S ratio of the matte (Cu 2 S: 396), suggesting that most of the copper contained in the slag is not in the form of entrained matte In addition, the magnetite (Fe 3 O 4) content in the 2018年2月5日 Piles of steel slag, a solid waste generated from the iron and steel industry, could be seen due to no utility found for the past century Steel slag has now gained much attention because of its new applications The properties of slag greatly influence its use and thus had got varied applications The chemical composition of steel slag varies as the mineral composition Review on the innovative uses of steel slag for waste minimization2022年5月11日 Cement and steel slag powder from literature The cement used was conventional Portland cement OPC type 1 that met ASTM C 150 specifications In terms of specific gravity, the cement content ranged between 3040 and 3100 cm 2 /g The cement content varied between 23735 and 550 kg/m 3Based on collected data from the literature, the Electrical conductivity, microstructures, chemical compositions, 2023年6月28日 In addition to the desired metal, a byproduct is also produced, termed slag Slag is an impurity extracted from the metal ore itself A brief history Smelting has been used to make key tools and weapons as far back as ancient history The technique dates back to 5000 BCE, when the first metal, copper, was smelted in the Middle EastSmelting Metal: How It Works Metal Supermarkets UK
.jpg)
Copper Smelting Slag Cleaning in an Electric Furnace by Using Waste
2020年10月16日 For the lower slag layer (Figure 4(b)), the content of magnetite is 102 wt pct Fayalitebased copper slag has a certain solubility to magnetite, thereby avoiding the formation of foaming slag and reducing the copper content in the slag significantly (w Cu = 389 wt pct)2024年2月7日 Reduction The reduction process for copper slag is typically followed by magnetic separation []Depending on the temperature and intensity of reduction, it can be classified as direct reduction, deep reduction, and smelting reduction []Commonly used reducing agents include coke, biomass carbon, and natural gas [31, 32]The reduction process converts Resource Utilization of Copper Slag with a Focus on Springer2020年10月29日 The primary energy consumption and greenhouse gas emissions from nickel smelting products have been assessed through case studies using a process model based on mass and energy balance The required primary energy for producing nickel metal, nickel oxide, ferronickel, and nickel pig iron is 174 GJ/t alloy (174 GJ/t contained Ni), 369 GJ/t alloy (485 Energy Consumption and Greenhouse Gas Emissions of Nickel 2022年10月10日 The nonferrous metal smelting industry is an important sector for promoting world industrial development Since the twentyfirst century, China has become the largest producer of nonferrous metal products in the world, and its annual output accounts for approximately 40% of the world’s total output (Liao et al 2020)China’s total output of zinc, an Environmental impact of typical zinc smelting that implements
.jpg)
Evaluation of TitaniaRich Slag Produced from Titaniferous
2020年8月3日 The remaining oxides are proportionally concentrated in the slag, including the titania, resulting in slag typically containing > 80% TiO 2, but ranging from about 75–85% TiO 218 The slag composition is dependent on the starting concentrations of the various oxides in the feedstock, the degree of iron reduction and the contribution of contaminants introduced during 2023年5月15日 Steel slag is the main solid waste generated in the steelmaking process, accounting for 15 to 20% of crude steel output [1]China's crude steel output in 2021 was 1035 billion tons [2], more than half of the global crude steel output (19505 billion tons) [3], and the steel slag output exceeded 120 million tonsIn contrast, the comprehensive utilization rate of Comprehensive utilization of steel slag: A review ScienceDirect2005年2月1日 Steelmaking slag, an important metallurgical byproduct, is composed of a large amount of valuable components, including CaO, Fe t O, MnO, and MgO, all of which are required in the steelmaking (PDF) Industrial uses of slag The use and reuse of Although the Romans built furnaces with a pit into which slag could be run off, little change in ironmaking methods occurred until medieval times By the 15th century, many bloomeries used low shaft furnaces with water power to drive Iron processing Definition, History, Steps, Uses,
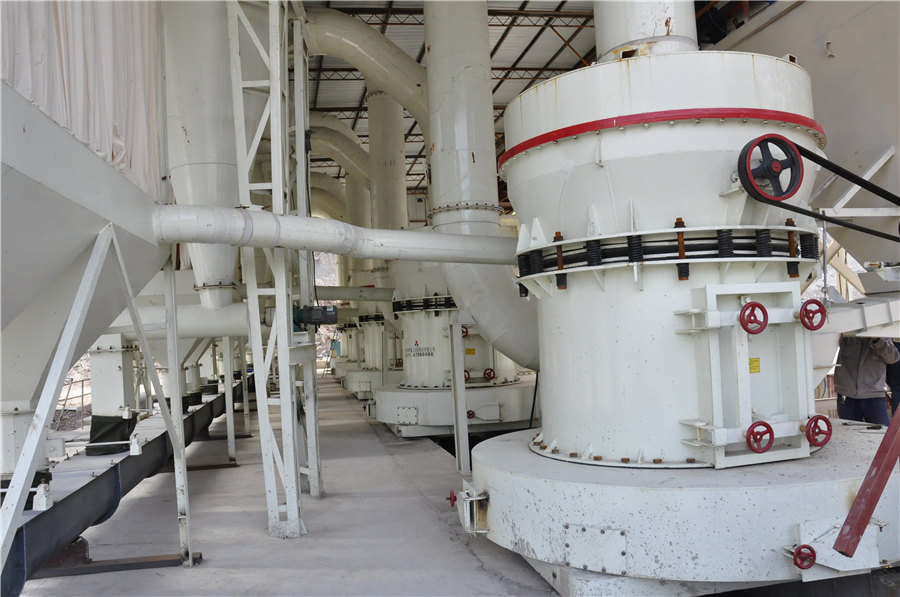
Ground Slag Properties, Characterisation and Uses
‘slag’ generally refers to ground, granulated, iron blast furnace slag – with the descriptors to be explained and developed in this technical note In a general sense, the term ‘slag’ refers to a waste material separated from metals during the smelting or refining of an ore in a blast furnace ‘Slags’ are formed during the smelting or2023年3月3日 Shamsi et al [] studied the effect of copper slag particle size on the flotation effect, the highest copper recovery efficiency of 7989%was achieved when the grinding time was 80 min and the grinding size was 48 μm []Sibanda et al [] controlled the size of copper slag and flotation reagents to improve copper recovery by 16% when the particle size of copper slag Review on Comprehensive Recovery Valuable Metals and 2018年11月7日 Steelmaking plants continuously strive to reduce the environmental load in the steelmaking process, resulting in the recycling of energy, water, and other byproducts In this chapter, techniques for the treatment and recycling of metallurgical slags are described Metallurgical slags are considered secondary raw materials and are used or added during the Treatments and Recycling of Metallurgical Slags IntechOpen2016年2月29日 In general, slag from smelting process arises from extraneous materials such as rust and oxides; oxidation of elements in the charge (eg iron, copper, zinc); residues from fuels; fluxes employed in the process (silica, borax, sodium nitrate, sodium carbonate, fluorspar); crucible erosion Then, slag can vary in appearance and chemical Gold Smelting Refining Process 911Metallurgist
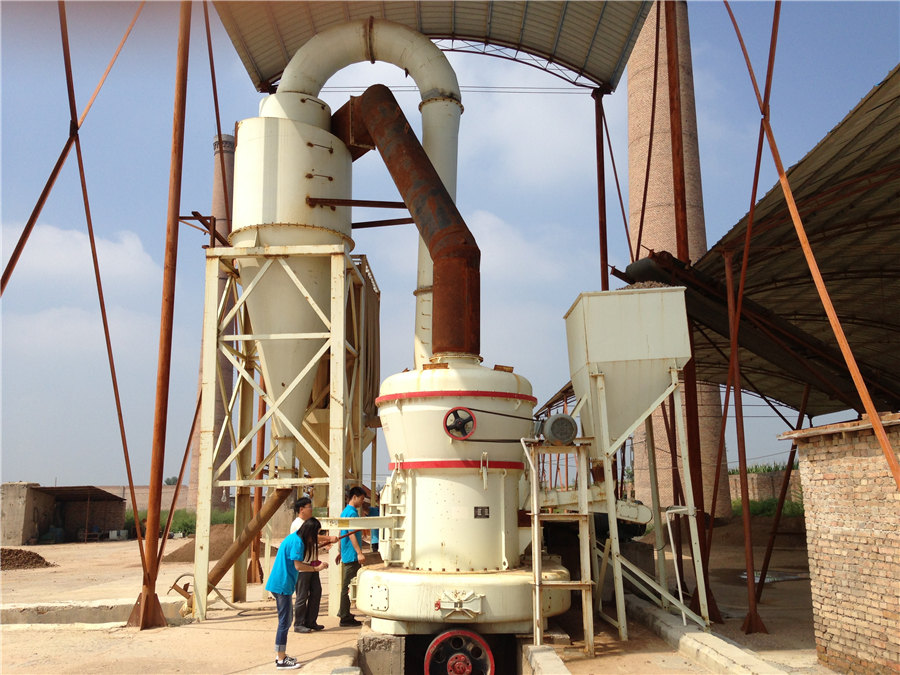
Utilization of steel slag waste as construction material: A review
2023年1月1日 All content in this area was uploaded by Pradeep Kumar on Feb 15, 年2月22日 Sulfidation treatment of copper smelting slag In the sulfidation experiment, the particle size of the synthesized slag was controlled below 80 mesh (178 µm)The mixture of CaSO 4 and anthracite was pelletized at a pressure of 10 MPa in a Ø 4 mm pressing tool, and the weight of every pellet was roughly controlled to be 004 g Then the smelting slag and CaSO 4 The Phase Transition and Element Distribution of Copper Smelting Slag 2017年2月8日 Materials The smelting slag used in this study was obtained from a copper plant in China Mineralogical analysis, performed using scanning electron microscope (SEM) and energy dispersive Xray spectroscope (EDS), polarizing microscope and Xray diffraction (XRD), indicated that fayalite (Fe 2 SiO 4) and magnetite (Fe 3 O 4) phases were major components The Recovery of Copper from Smelting Slag by Flotation Process2024年4月15日 In pyrometallurgy process involving drying, calcination and reductive smelting steps, Saprolite ore is subjected in an electric arc furnace to produce Fe–Ni alloy and Ni matte To optimize the nickel smelting step, the slag consisted of MgO–SiO2–FeO and having a lower viscosity and high fluidity is required In this study, a number of new slag samples with varied Artificial Slags with Modulated Properties for Controlled Nickel
.jpg)
Slag: From Byproduct to Valuable Construction
2014年7月29日 Slag is a byproduct of the metallurgical smelting process Slag has a double role: it permits removal of impurities, known as gangue, (The ore beneficiation process at a mine is designed to remove as much waste and 2023年8月1日 The increasing demand for copper and the depletion of primary resources have urged researchers and industrialists to explore secondary resources, copper slag being one of them Generally, copper is mined from ores containing 04–08% Cu [47] Copper metal is produced from these ores following a pyrometallurgical route of smelting or convertingA comprehensive review on the recovery of copper values from copper slagIron processing Smelting, Refining, Alloying: The primary objective of iron making is to release iron from chemical combination with oxygen, and, since the blast furnace is much the most efficient process, it receives the most attention Iron processing Smelting, Refining, Alloying Britannicabecause when it ends up in the slag it can lead to failure of the TCLP Barium produces a deep green flame over the slag and matte, a stony appearance, and a large amount of matte Too much alkaline earths or too much zinc can “freeze” a blast furnace [2] A low silica highlime slag is a dangerous sign that the furnace is about to freezeA REVIEW OF SLAG CHEMISTRY IN LEAD RECYCLING
.jpg)
THE QUANTITIES OF MATERIALS IN ONE CUBIC METER OF
2019年1月21日 THE QUANTITIES OF MATERIALS IN ONE CUBIC METER OF CONCRETE USING DIFFERENT MIX RATIOS January 2019; DOI:10 The use of waste materials with pozzolanic products in concrete production is 2021年3月16日 By Alton Tabereaux, Contributing Editor Spent potlining (SPL) disposal is one of the largest environmental waste management challenges confronting worldwide primary aluminum smelters due to its toxicity The International Aluminium Institute (IAI) asserts that 16 million tons of SPL were generated from primary aluminum production in 2019,1 making it the The SPL Waste Management Challenge in Primary Aluminum2021年12月23日 This paper presents observations and analyses on seven slag pieces from two thirdmillennium cal BC (Late Copper Age/Early Bronze Age) rock shelters in the Trentino, northeastern Italy: La Vela di Valbusa and the Riparo di Monte Terlago We review previous work on contemporary slags from the region and show that the smelting did not follow the wellknown The smelting of copper in the third millennium cal BC Trentino, 2024年5月26日 When figuring out the weight of crushed stone, consider its density The density changes with the stone type, size, and how compacted it is For instance, a cubic meter of crushed limestone might weigh about 1,600 kg Crushed gravel could be around 1,400 kg per cubic meter To find out how much stone you need, measure the area and calculate its Crushed Stone Weight Calculator calculattor
.jpg)
How Much Does Crushed Limestone Cost? The Pricer
2021年8月27日 Always overestimate required amounts by 1020% for compaction, smoothing, and waste Crushed Limestone vs Other Aggregates Crushed Limestone: $28$80 per ton or cubic yard; Crushed Granite: $35$75 per ton or cubic yard; Pea Gravel: $30$50 per ton or cubic yard; River Rock Boulders: $45$150 per ton or cubic yardReferences 1 T Annunziata Branca, V Colla: Possible Uses of Steelmaking Slag in Agriculture: An Overview, Material Recycling Trends and Perspectives, Dr Dimitris Achilias (Ed), 2012, ISBN: 9789535103271, InTech, Accessed April 2020; 2 Xmi You, Nchuan Yang, W Ling, D Jiang: The Second International Conference on Mining Engineering and Metallurgical more metal less waste the zero slag process Total Materia