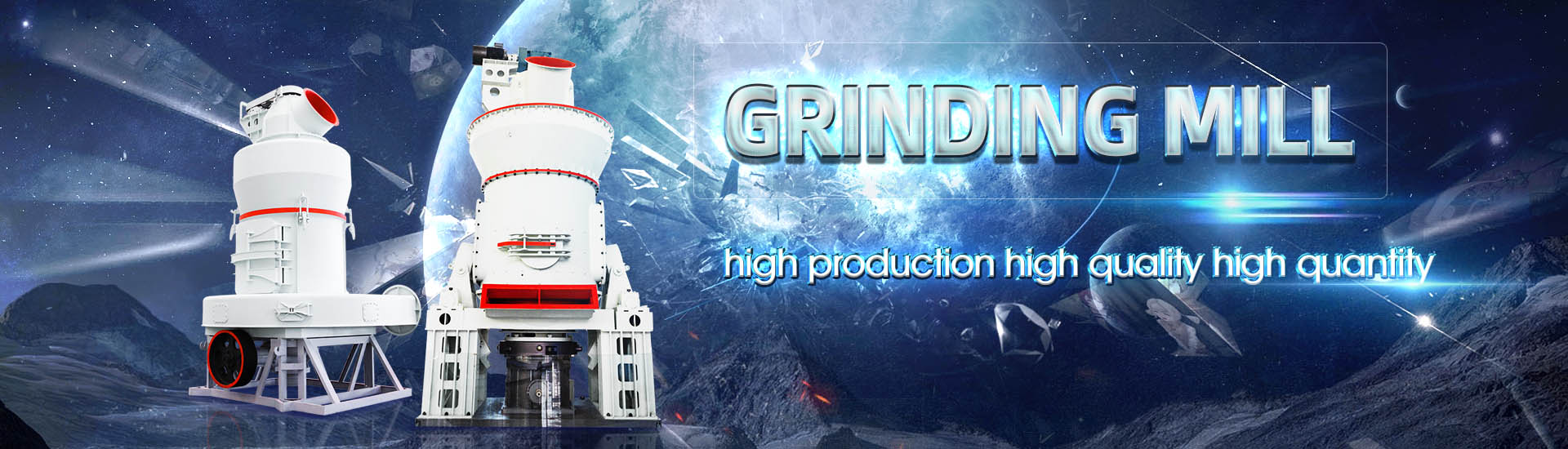
PCF efficiency energysaving twoinone ore mill crushing price
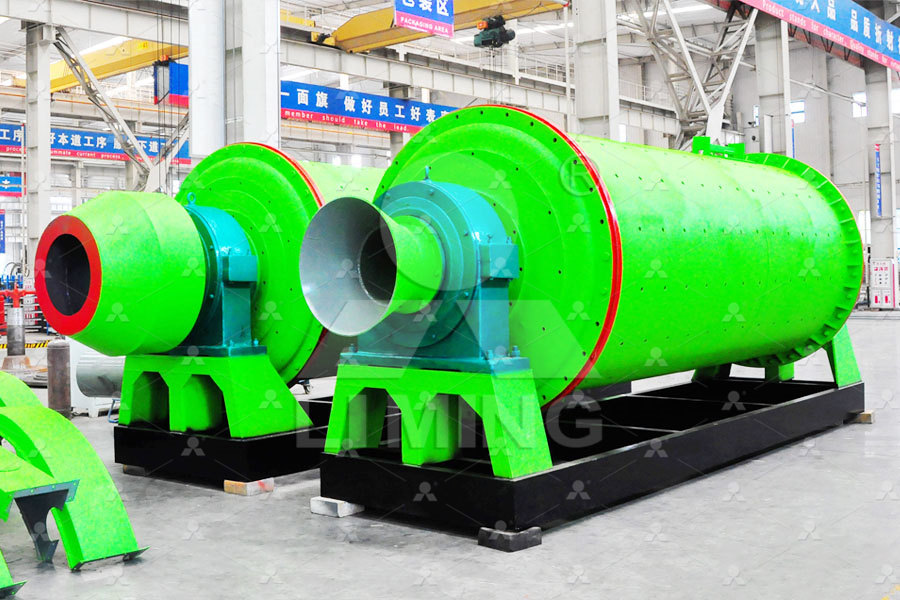
Modeling and Improving the Efficiency of Crushing
2023年5月16日 This article presents a systematic review of the task of improving the energy efficiency of crushing units This is achieved by studying modelling methods and results, the automation of crushing and grinding 2016年1月15日 These four control variables are optimally coordinated in order to improve the operation energy efficiency of the VSI crushing process Simulation results based on a Optimal energy control of a crushing process based on vertical 2014年1月1日 This paper presents factors affecting the overall performance of the Çayeli mine crushing plant operation by addressing the critical design parameters as well as the Factors affecting the performance of crushing plant operations2014年4月15日 Large ore pass capacity leads to more cost saving and better switching profile This paper develops two optimal control models for the energy management of a mining Optimal energy management for a jaw crushing process in deep
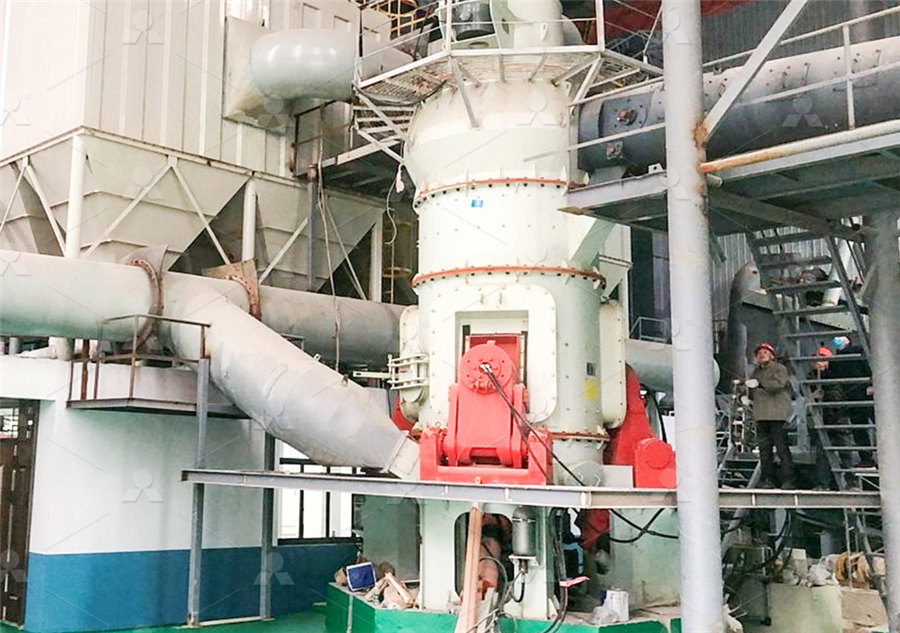
Energy considerations in compressive and impact crushing of rock
2008年8月1日 This measure suggests that a VSI can save 2–14% of the energy consumed in grinding, depending on the energy model used and the final product size This estimate is in 2021年6月10日 Comminution Circuits Are The Single Biggest Energy Consumer At Mines Improving Energy Efficiency Here Is Therefore A Key Part In Improving The LongTerm Crushing Energy Efficiency North American Mining MagazineThe paper presents investigations on grinding energy consumption, size distribution and microfracturing of HPGR products, which affect the efficiency of the whole comminution and Quantification of HPGR energy efficiency effects on downstream 2013年12月18日 Optimization of grinding media size and quality, as well as of other operational factors, can reduce energy use by a factor of two or more The stirred mills used to perform Energy Use of Fine Grinding in Mineral Processing
.jpg)
Plant Automation for EnergyEfficient Mineral Processing
2017年11月2日 Mineral processing is one of the most energyintensive stages of the overall mining beneficiation chain, with an increasing share of the industry footprint This chapter 2024年6月28日 The results demonstrate that the crushing efficiencies of ore crushing particles, raw material crushing particles, and cement crushing particles can respectively reach 807%, 7015%, and 8027% Energy Efficiency Measurement of Mechanical Crushing Based 2023年6月30日 in energy prices over the last few years, most mining companies are focused on reducing energy consumption in order to cut the cost of the final product [ 3 ] The crushing process is widely used Modeling and Improving the Efficiency of Crushing 2019年10月8日 With the adoption of largescale carrying equipment, the crushing mill’s ore feeding size has reached 12 to 2 m, which has promoted the development of the jaw crusher to largescale The compound pendulum Crushing and Grinding Process JXSC Machine
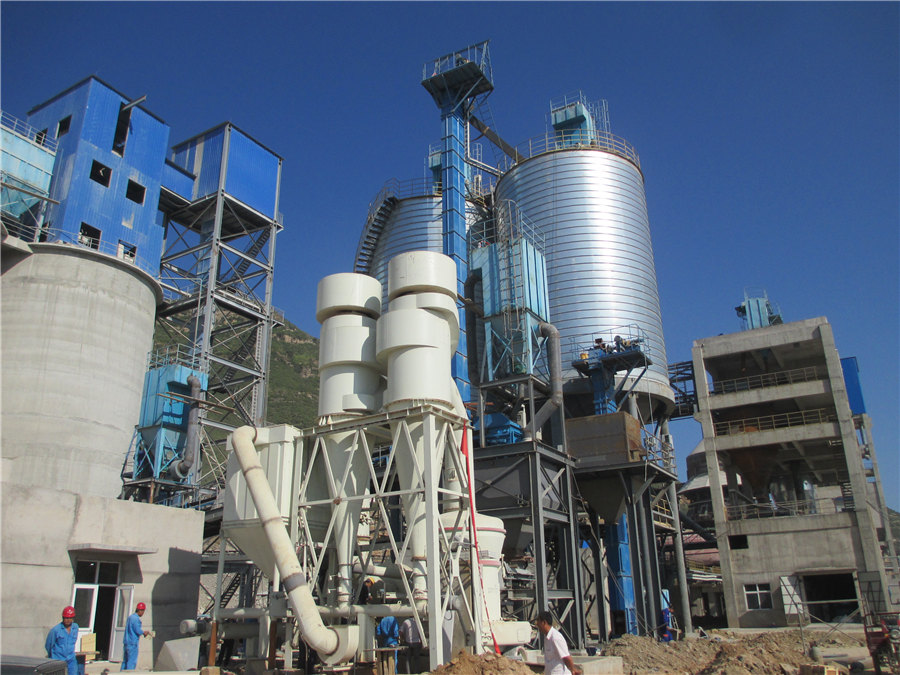
Peak crushing force (PCF) and mean crushing force (MCF) surface
HS EA box structure, AHS energy absorption box structure, PS energy absorption box structure, and APS energy absorption box structure are 1142%, 117%, 1092%, and 1162% higher than traditional 2014年9月1日 Power consumption and therefore efficiency of crushing equipment are becoming increasingly important mainly due to the continuous and rapid increase of energy costs and efforts to minimise CO 2 Assessing the energy efficiency of a jaw crusher Request PDF2014年1月1日 This estimate is in agreement with an energy saving of 118% observed in an iron ore application where VSI’s were introduced as a crushing step preceding the grinding circuit View Show abstractFactors affecting the performance of crushing plant operations2016年3月5日 All that Rittinger himself really said on the laws of crushing, in his famous book on oredressing, fills barely two out of about 600 pages, and in these two pages be says clearly: ‘the increase of the surfaces exposed is directly proportional to the force required for reducing’ (These words are also in the original text printed in italics)Crushing Energy Work of Crushing Machines 911Metallurgist
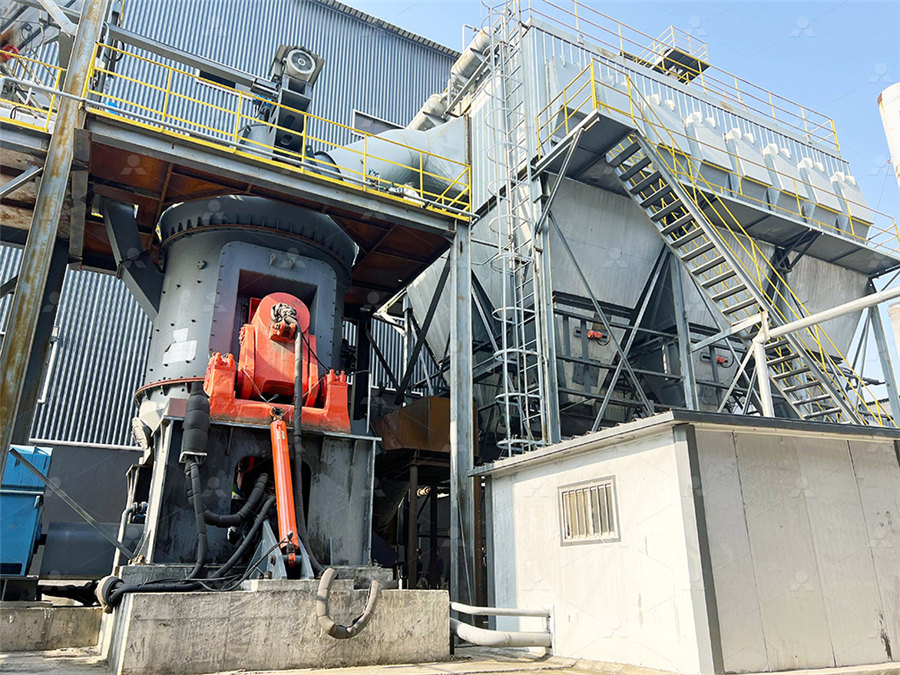
How to ensure energy efficiency in mining
2018年12月18日 Some designers prefer having two smaller mills instead of one larger mill The thinking is that when one mill goes down, the other is still operating and you still have 50% or more plant throughput But having one large piece of equipment means a lot of cost saving at every stage of the operation less civil and structural costs (concrete and 2012年6月1日 As the cylinder starts to rotate, the grinding balls inside the cylinder crush and grind the feed material, generating mechanical energy that aids in breaking bonds, activating the catalyst, and Grinding in Ball Mills: Modeling and Process Control2002年11月1日 Instead of defining comminution efficiency in terms of the surface free energy of the solid, we propose that it be defined as a relation between the specific energy to produce the given amount of new surface in singleparticle comminution with that required for the comminution device under consideration: (1) Energy efficiency =[E m (SP)/E m (Mill) to produce same The energy efficiency of ball milling in comminution2015年9月4日 Sugar cane mills are energy intensive industries and also have a large potential of providing surplus energy in terms of heat or power Identification of heat and mechanical losses in sugar mills is one approach in indicating Assessing the potential of energy saving in a
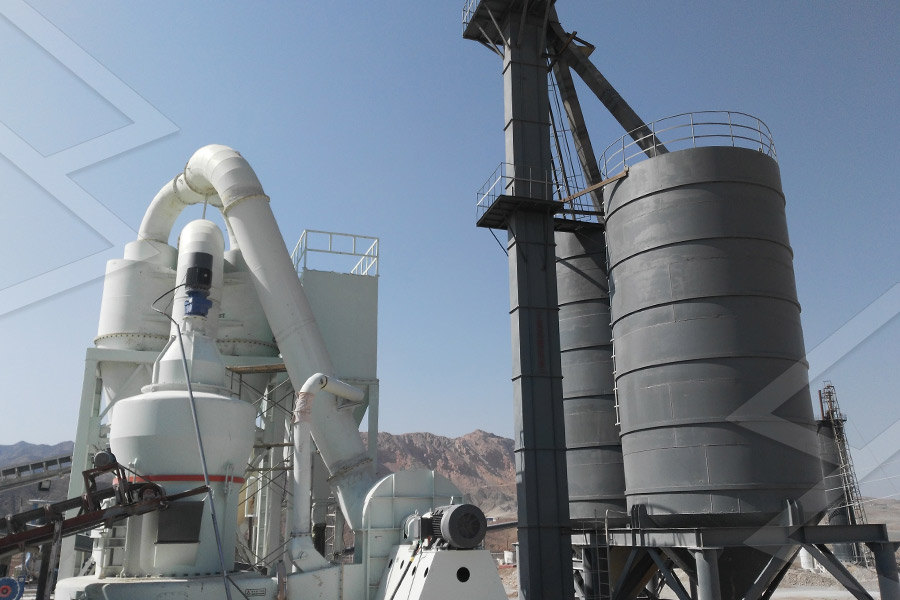
Energy efficiency at the paper mill—dilemma of improvement
2016年10月18日 The paper industry is heavily using energy during all the phases of the manufacturing process This is especially the case in Nordic mills where pressure ground wood is the source of fiber The purpose of this case study is to show how energy consumption behaves on a monthly basis in a Finnish paper mill that has several paper machine lines The research 2021年6月10日 Ciutina, S and Soriano, RJ, “Curved Pulp Lifters – Can They Save Energy”, Proceedings of the 12th AUSIMM Mill Operators’ Conference 2014 (AUSIMM; 2014), pp109116, cited by LynchWatson, “How to Ensure Energy Crushing Energy Efficiency North American Mining The net decrease in energy cost is $0294 per ton For a mine crushing 40 million tons of ore per year, the savings are $118 million per year This is a very worthwhile reduction in cost One observes in figure 2 that the decrease in sizing energy cost flattens as the work index decreases and the increase in powder factor acceleratesThe Effects of Blasting on Crushing and Grinding Efficiency and Energy 2013年1月1日 The return of 100400% of the ore mass to the mill typically reduces the retention time of the material inside the mill increasing the grinding capacity, improving the energy efficiency, resulting THE BENEFITS OF HIGH CLASSIFICATION EFFICIENCY IN CLOSED BALL MILL
.jpg)
Energy Efficiency Analysis of Copper Ore Ball Mill Drive Systems
Energies 2021, 14, 1786 3 of 14 ring gear is engaged with a pinion gear In versions with lowspeed motors, the pinion is set on a shaft directly connected to the motor, and in versions with highspeed motors thewith fine screens for the tertiary crushing stage provides maximum energy efficiency For hard ore the secondary crushing product should be screened before feeding the HPGR to avoid oversize material damaging the rolls (Morley, 2006) Figure 1 shows the simplified flowsheets for the two types of circuits used in this research The SABC circuit isA structured approach to the evaluation of the energy 2014年4月1日 This paper develops two optimal control models for the energy management of a mining crushing process based on jaw crushers The performance index for both models is defined as the energy cost to Optimal energy management for a jaw crushing process in deep mines2016年3月11日 As the need for finer crushing increases, consideration must be given to the achievement of maximum crushing and screening efficiency The majority of crushing plants recently constructed have accomplished this desired efficiency by optimizing plant design, crusher design and automation By improved efficiency a decrease in energy consumption Crushing Plant Flowsheet DesignLayout 911Metallurgist
.jpg)
Creating energy efficiency from pit to plant Metso
offer energyefficiency opportunities HPGRs use two counterrotating tires – one fixed and one floating – studded with tungsten carbide nodules to instantaneously crush ore The feed is introduced to the crushing zone, where high pressure is applied to the bed of material in a controlled manner This creates microcracks withinanalysis of the results shows that taking into account energy consumption, it is better to use twostage crushing process For given materials energy consumption in the twostage crushing process was reduced by 30% Key words: rock crushing, jaw crusher, crushing efficiency, two stage crushing process 1 INTRODUCTION The main aim of processing ANALYSIS OF ENERGY CONSUMPTION OF CRUSHING 2010年1月1日 Comparative high pressure grinding rolls (HPGR) and cone crusher pilotscale tests were conducted using Upper Group 2 (UG2) platinumbearing ore in order to determine the impact of microcracks in Efficiency, economics, energy and emissions Energy Consumption in Crushing and Grinding The energy input to size ore fragments is large Overall reduction, performed in a series of stages may be from an eighty percent feed size passing of 40 cm (158 inches) to a final product size of 270 to 325 mesh (053 to 045 mm) A lot of energy is expended to accomplish this, andThe Effects of Blasting on Crushing and Grinding Efficiency and Energy
.jpg)
Copper Ore Grinding in a Mobile Vertical Roller Mill Pilot Plant
2014年10月1日 In a test performed in the Loesche test center in Germany, copper slag grinding saved 229% energy in an airswept model and 344% energy in an overflow model [13,14]Request PDF On Mar 15, 2015, Mathis Reichert and others published Research of iron ore grinding in a verticalrollermill Find, read and cite all the research you need on ResearchGateResearch of iron ore grinding in a verticalrollermillPDF On Aug 1, 2013, Ernst Worrell and others published Energy Efficiency Improvement and Cost Saving Opportunities for Cement Making An ENERGY STAR® Guide for Energy and Plant Managers Find (PDF) Energy Efficiency Improvement and Cost Saving Opportunities with fine screens for the tertiary crushing stage provides maximum energy efficiency For hard ore the secondary crushing product should be screened before feeding the HPGR to avoid oversize material damaging the rolls (Morley, 2006) Figure 1 shows the simplified flowsheets for the two types of circuits used in this research The SABC circuit isA structured approach to the evaluation of the energy
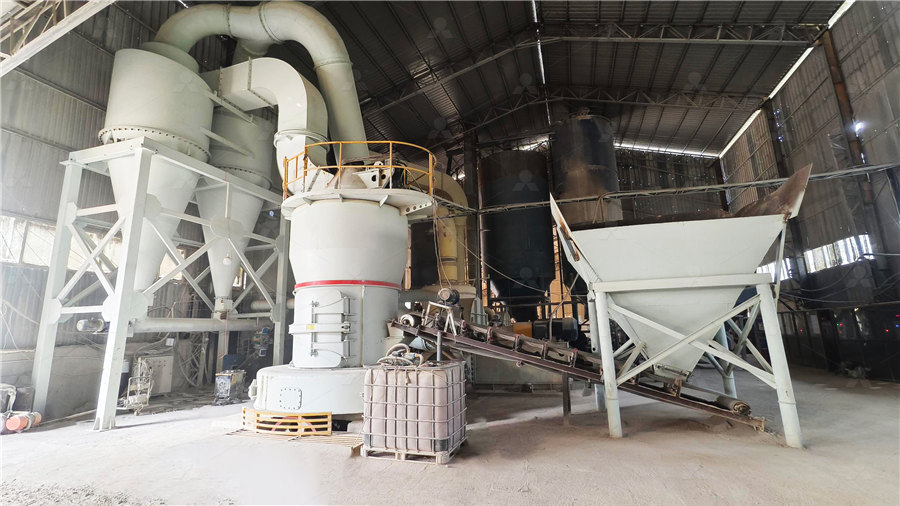
Energy considerations in compressive and impact crushing of rock
This measure suggests that a VSI can save 2–14% of the energy consumed in grinding, depending on the energy model used and the final product size This estimate is in agreement with an energy saving of 118% observed in an iron ore application where VSI’s were introduced as a crushing step preceding the grinding minution, Energy Efficiency, Crushing, Cone Crusher, Sustainability, CH865 IMPC 2016: XXVIII International Mineral Processing Congress Proceedings ISBN: 9781292 Page 1 of 12IMPC 2016: XXVIII International Mineral Processing ResearchGate2024年5月3日 As energy conservation and consumption reduction become the key tasks for the sustainable development of mineral processing plants, taking effective measures to improve production efficiency and reduce energy consumption has become an important issue in current mine mineral processing In the entire mineral processing process, crushing and grinding More Crushing and Less Grinding, A Wise Way to Saving Energy 2015年9月8日 As outlined in part I of this study, the cane sugar industry has been seen as one of the most attractive agroindustries with significant potential for producing surplus electric power that can be sold to the national grid, as well as saving excess bagasse through implementation of energy efficiency measures [1, 2]The most widely practised method of yielding surplus electric Upgrading of a traditional sugar cane mill to a modern mill and
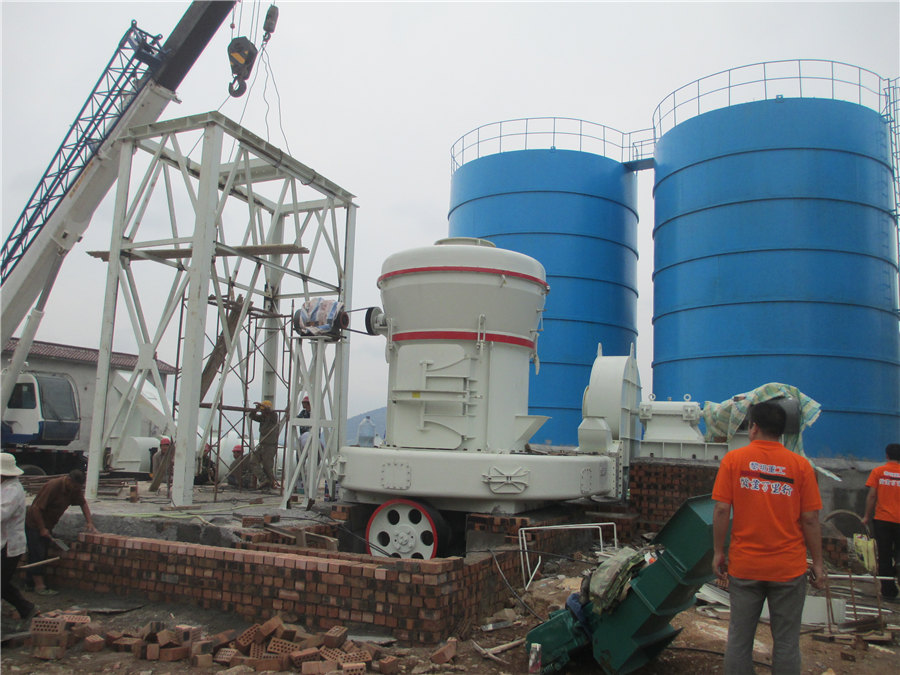
EnergyEfficient Technologies in Cement Grinding
2016年10月5日 In this chapter an introduction of widely applied energyefficient grinding technologies in cement grinding and description of the operating principles of the related equipments and comparisons over each other in Startup of the LSPMSM SMH1732T motor with a filled ball mill after two hours of downtime: (a) active power active power, (b) current intensity, (c) voltage "Energy Efficiency Analysis of Copper Ore Ball Mill Drive Systems" Skip to search form Skip to main Review of Linear Electric Motor Hammers—An EnergySaving and EcoFriendly Energy Efficiency Analysis of Copper Ore Ball Mill Drive Systems2024年9月1日 This paper presents a novel approach aimed at optimizing underground mine bench blasting practices to minimize energy consumption in downstream comminution processes The proposed methodology integrates multivariate regression analysis modeling of blastinduced particle size distributions with the Work Index calculation, offering a comprehensive framework Integrating Underground Blast Fragmentation Modeling for with fine screens for the tertiary crushing stage provides maximum energy efficiency For hard ore the secondary crushing product should be screened before feeding the HPGR to avoid oversize material damaging the rolls (Morley, 2006) Figure 1 shows the simplified flowsheets for the two types of circuits used in this research The SABC circuit isA structured approach to the evaluation of the energy
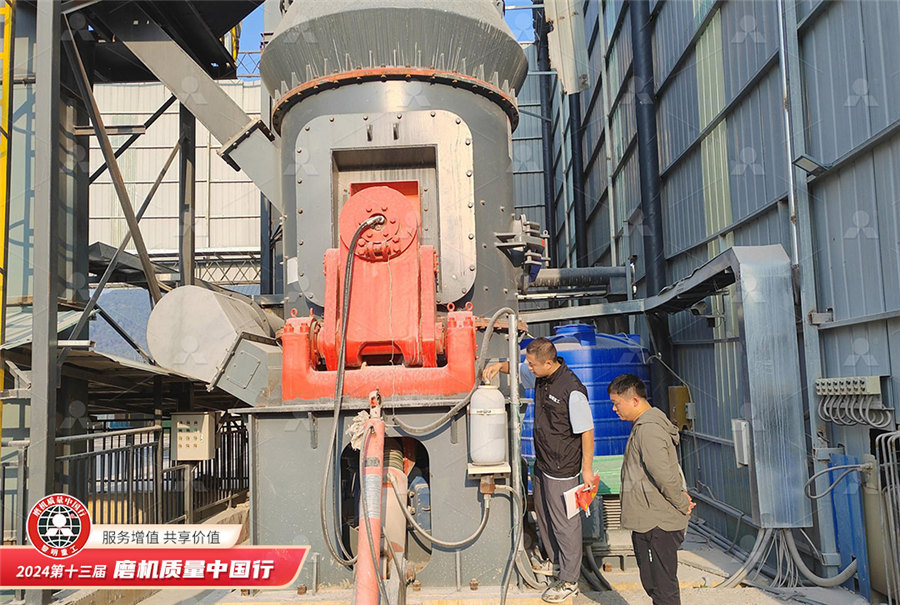
Reduction of Fragment Size from Mining to Mineral Processing: A
2022年10月4日 A notable fact is that the energy efficiency of conventional milling is only about 1%, as mentioned in Sect 1 An earlier experimental study indicated that about 80–90% of the energy input of a ball mill was used in heating the material (Schellinger 1951, 1952), and a recent study showed that over 75% of the electrical energy was used to heat the slurry (Bouchard et 2023年7月22日 The ore crushing process includes four types: ore coarse crushing, ore medium crushing, ore fine crushing, and ore superfine crushing Ore coarse crushing is a process of crushing ore blocks with a feeding particle size of 500–1500 mm to 125–400 mm The maximum crushing ratio of coarse crushing is about three The main force in the coarse Ore Crushing SpringerLink2020年12月21日 Energy saving potential for various energyintensive processes in mining [3] 1 Btu (British thermal unit) ≈ 1055 Joule Increasing Energy Efficiency and Productivity of the 2021年2月26日 Milling is among the most energyconsuming technological stages of copper ore processing It is performed in mills, which are machines of high rotational masses The start of a mill filled to capacity requires appropriate solutions that mitigate the overloading One method for increasing the energy efficiency of ball mills is to optimize their drive systems This article Energy Efficiency Analysis of Copper Ore Ball Mill Drive
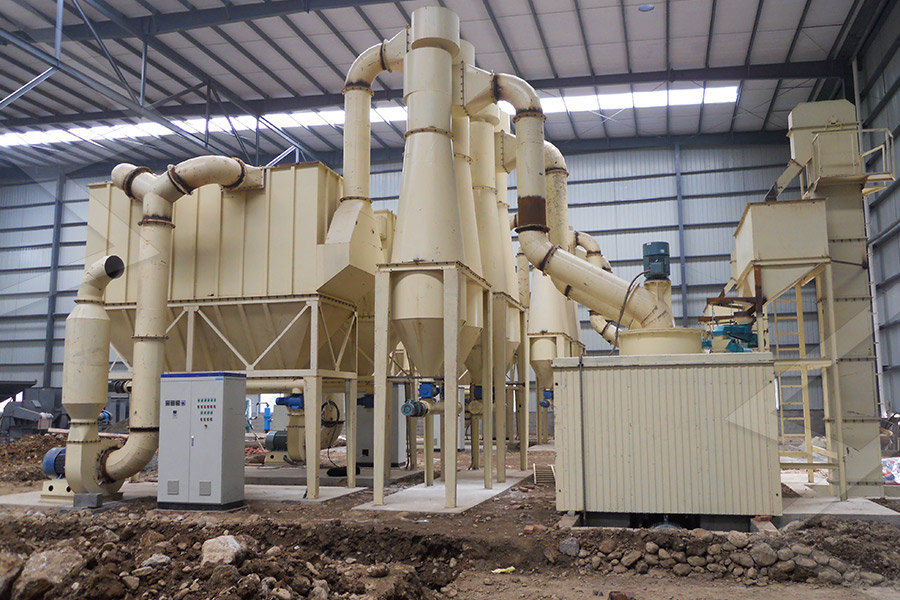
Energy Efficiency Analysis of Copper Ore Ball Mill Drive Systems
Milling is among the most energyconsuming technological stages of copper ore processing It is performed in mills, which are machines of high rotational masses The start of a mill filled to capacity requires appropriate solutions that mitigate the overloading One method for increasing the energy efficiency of ball mills is to optimize their drive systems This article looks at two