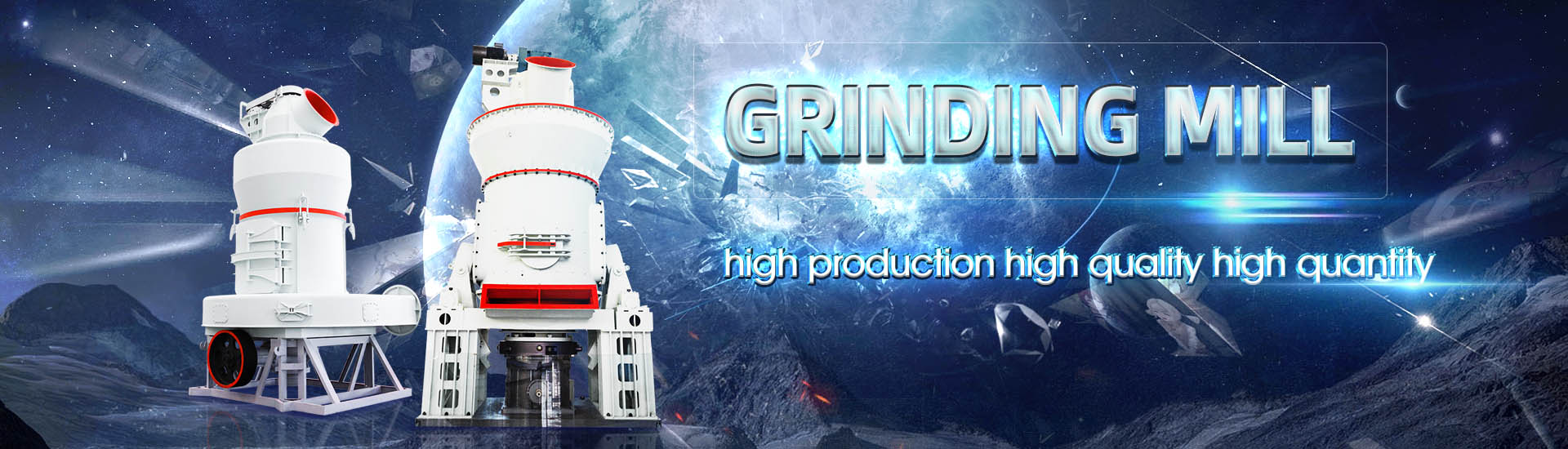
Why grinding and fixed cone wear of grinding production line are different
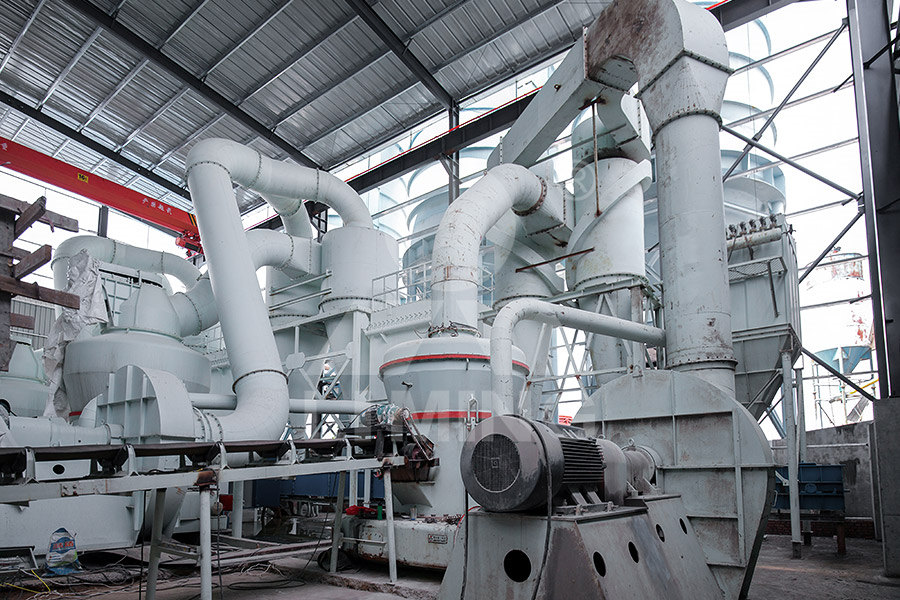
A comprehensive review on the grinding process: Advancements,
2022年6月24日 Grinding is a manufacturing process which significantly contributes in producing high precision and durable components required in numerous applications such as aerospace, defence and2016年11月22日 However, the wear of an individual grit on the surface of grinding wheel may not have a large effect on the grinding wheel Effect of different parameters on grinding efficiency 2011年1月1日 Due to increasing wear during grinding, conditioning is necessary according to specific toollife criteria Embedding conditioning into the grinding process gives rise to Conditioning and monitoring of grinding wheels ScienceDirect2021年7月3日 Grinding process control balances these three interactions to achieve the desired parameters These interactions feed into three major commercial grinding processes: rough Machining 101: What is Grinding? Modern Machine Shop

Research on the Wear of Groove Structured Grinding Wheel Based
2024年3月4日 Understanding the laws of abrasive wear evolution and the influence of various factors on it is essential for rational planning of grinding parameters, optimization of grinding 2018年2月14日 In previous studies, a dressing model was successfully developed which predicts the dressing force in the dressing process as well as the workpiece roughness and Influence of different grinding wheel and dressing roller 2013年5月1日 The present paper elaborates the dependencies of different parameters like grain size, grain type, type of bond, mode of grinding, depth of cut, feed, wheel wear, coolants and Influence of Process Parameters on Grinding A Reviewinferring wear resistance Factors influencing grinding performance include media size selec tions , sha pe considerations, and media quality Grinding performance is measured in terms of Wear ofgrinding media in the mineral processing industry: An
.jpg)
Highspeed grinding – Knowledge and References – Taylor Francis
Highspeed grinding is a highperformance grinding technology that uses adapted grinding wheel specifications to machine materials such as steels, tungsten carbides, plastics, and ceramics 2018年2月6日 Grinding is the material removal and a surface finish process in which the material is removed from the work surface in the phase of small chips by process of tiny A Review of Cylindrical Grinding Process parameters by using 2020年6月29日 Grinding machines have advanced in design, construction, rigidity and application far more in the last decade than any other standard machine tool in the manufacturing industry Grinding machines fall into five Chapter 17: Grinding Methods and Machines2011年1月1日 Generally, the interaction between the workpiece and the surface of the grinding wheel defines the grinding process Viewed from this aspect, the grinding wheels are composed of three elements, the abrasive grit for material contact and – removal, the intergranular space for the storage of removed material and the coolant flow, and the bond to retain the grit on the wheelConditioning and monitoring of grinding wheels ScienceDirect
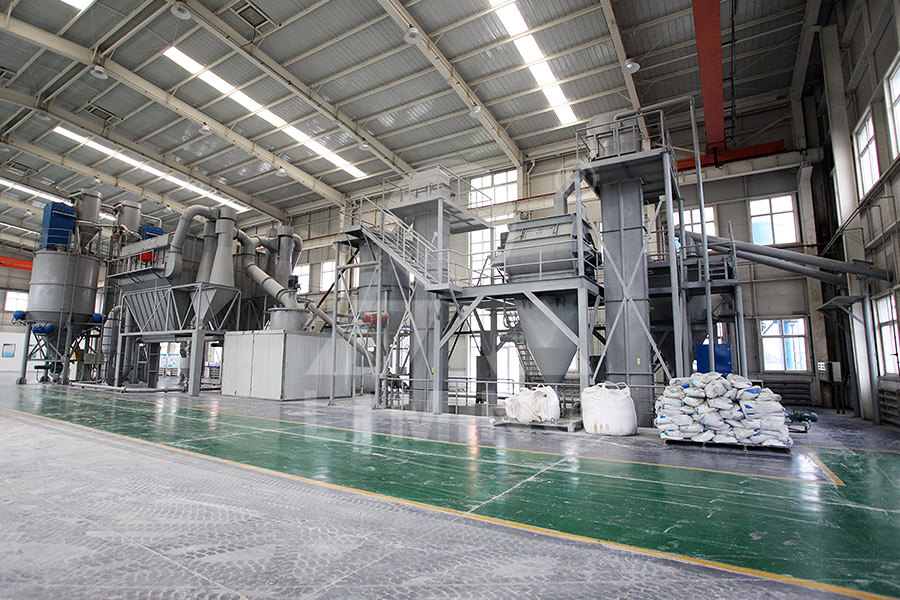
(PDF) Analysis of Relation between Grinding Wheel
2016年12月31日 This paper builds upon the existing grinding literature by studying the relationships between wheel wear and grinding forces for different depths of cut when surface grinding mild steel with an 2021年5月5日 A grinding machine is a production machine tool used in the manufacturing industry in which the grinding wheel is attached in the tool post and the workpiece is fixed to the work table and when the operation starts it removes the unwanted material to get the desired surface finish, correct size, and accurate shape of the workpieceGrinding Machine: Definition, Parts, Working Principle, Operation 2022年8月5日 In order to study the friction and wear properties of cast iron in free grinding environment under the condition of line contact This paper presented a new method to calculate the friction Study on friction and wear properties of cast iron material in line 2018年2月14日 Finally, in order to assess the tool with two different wheel speci cations, the effect of grain size has on the wear evolution and grinding process was analysed in the last batchInfluence of different grinding wheel and dressing roller
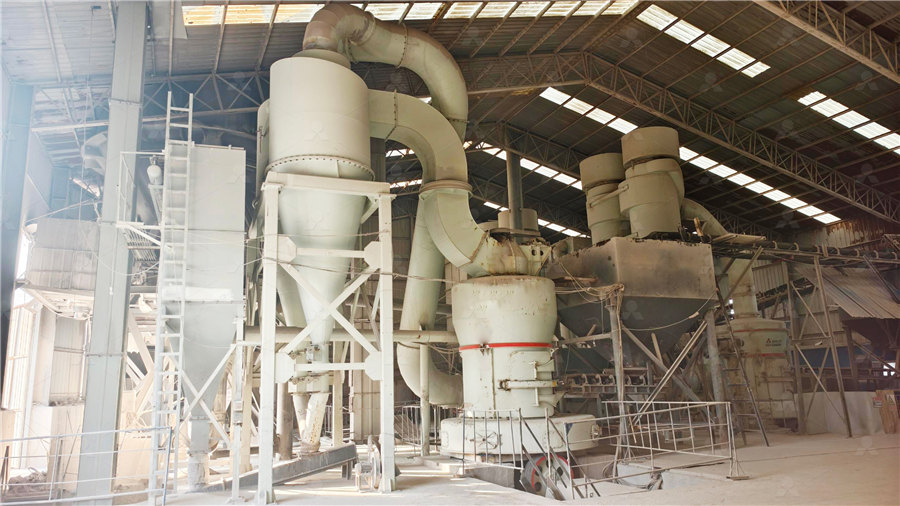
Common Grinding Problems : Causes and Methods of Correction
9 most common grinding problems and how to fix them Most Common Grinding Process Related Problem – Chatter Grinding is a crucial process in manufacturing and it is important to ensure that it is done accurately and efficiently However, there are a number of potential faults that can occur during grinding, such as feed lines or spirals on the workpiece, scratching, burning, and 2019年4月8日 Cutting tools and machine tools are the two main factors to achieve removal Based on the needs of processing technology in the movement requirement of the tool, the machine tool can achieve the tool’s trajectory and then achieve removal, and the cutting tools in contact with the workpiece can remove the workpiece material directly (Altintas 2012)Design of Tools, Grinding Wheels, and Precision Spindles2023年8月2日 The Application of Precision Grinding in Different Industries Precision grinding is crucial in various industries because it can produce parts to exact specifications and finishes Automotive Industry: Precision grinding is extensively used in the automotive industry for parts like pistons, cylinder rods, bushings, gears, and other componentsThe Details of Accurate Grinding: A Practical Guide ProleanTech2015年8月6日 There are two other factors that the liner design must accommodate other than the degree of lift The TYPE of grinding media and the SIZE of the media To do this, there have been developed different liner profiles, RIPPLE LINERS, WAVE LINERS, SINGLE STEP LINERS, DOUBLE STEP LINERS, SHIPLAP LINERS and LIFTER BARSGrinding Mill Liners 911Metallurgist
.jpg)
Machining 101: What is Grinding? Modern Machine
2021年7月3日 Made in the USA Season 2 Episode 6: Why, and How, Hardinge is Reshoring Machine Tool Production In this episode of Made in the USA, several executives and senior staff at Hardinge give their firstperson 2024年2月26日 Oxidised pellets have become an indispensable highquality charge for blast furnaces Nevertheless, highquality pellet feeds are becoming scarcer and scarcer To broaden the range of sources of pellet feeds and Grinding of Australian and Brazilian Iron Ore Fines for 2024年7月10日 Dry Grinding: Grinding without any coolant or lubricant Suitable for materials sensitive to liquids or when heat is not a major issue May cause increased wheel wear Vibration Grinding: Placing workpieces and abrasive What is Grinding: Definition, Types, Uses, and Working 2022年12月23日 In order to study the friction and wear properties of cast iron in free grinding environment under the condition of line contact, this paper presented a new method to calculate the friction coefficient by measuring the friction torque Through the selfdeveloped free abrasive grinding experimental device in line contact condition, this work carried out friction and wear Study on friction and wear properties of cast iron material in line
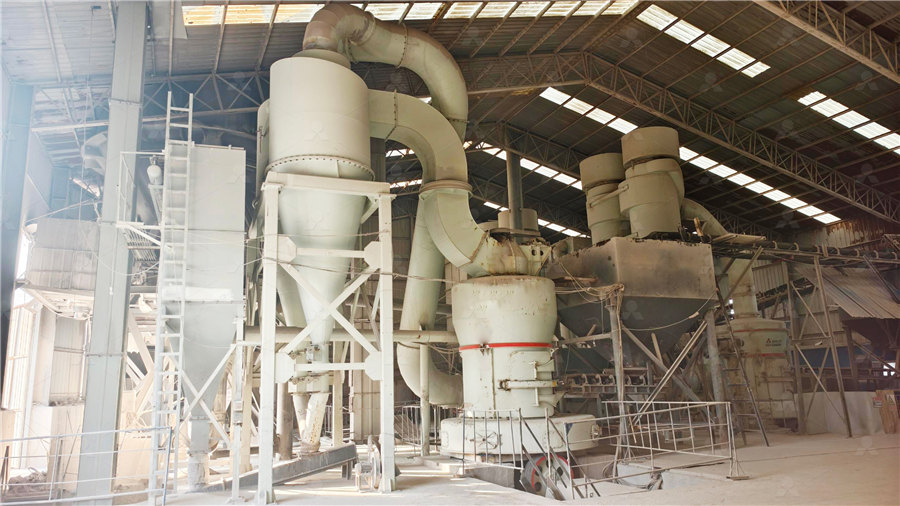
Analysis of grinding mechanics and improved grinding force
2023年7月1日 The establishment and numerical analysis of grinding force prediction models have consistently been a research hotspot Modeling methods are mainly divided into two categories: empirical and theoretical modeling 5 At the early stage, due to randomized grain characteristics on the grinding wheel surface, theoretical research on grinding force has 2018年4月30日 The wear behavior of grinding balls can be mathematically represented by the wear law equation: dw/dt = KDn; The wear rate exponent, n, is essentially equal to 2 for conventional ball milling When n = 2, the production wear rate is directly proportional to the wear speed, as determined by MBWT, according to the equation: WR = R(WS) (CW)/(DR) (TpH)List Factors Affecting Grinding Ball / Media Wear RatePrecision grinding is the process of removing metal from a workpiece to achieve a specific size, shape, or surface finish Surface grinding is a type of precision grinding that is used to create flat surfaces on metal workpieces This process involves using a grinding wheel to remove tiny bits of material from the surface of the workpiece until it is smooth and flatThe Ultimate Guide to Surface Grinding: Techniques, Applications, 2021年11月15日 Polishing is the final step, or steps, in producing a deformationfree surface that is flat, scratch free, and mirrorlike in appearance Such a surface is necessary to observe the true microstructure for subsequent interpretation, testing or Grinding and Polishing Guide Buehler Metallography
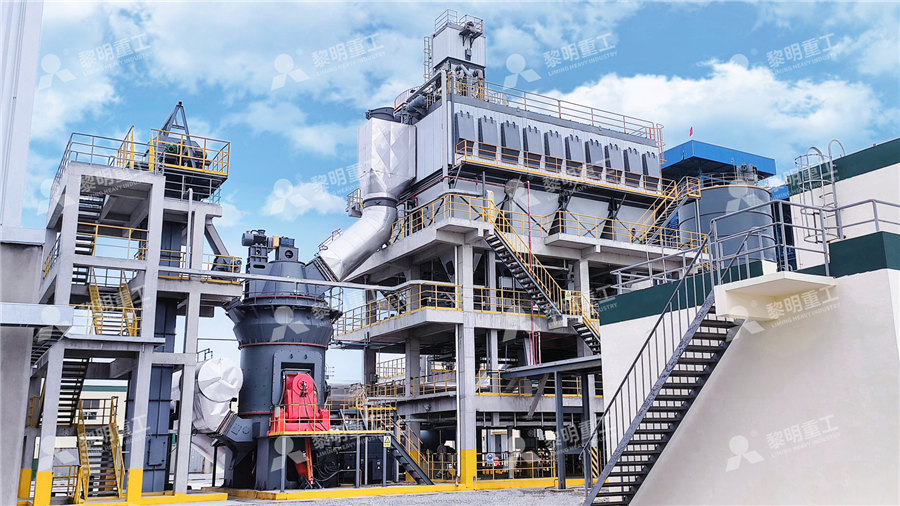
Numerical calculation of grinding wheel wear for spiral groove grinding
2022年3月4日 Due to its good cutting performance in titanium alloy machining, integral end mills are more and more used in machining aeroengine impeller blades The tool spiral groove plays the role of chip acceptor and chip removal, and the accuracy of its parameters has an important effect on the cutting performance In the grinding process of the spiral groove, the grinding 2015年9月7日 It is also crucial that the user has knowledge about the process, and potential changes in the plant that can cause process drift For example, liner wear can greatly affect SAG mill performance Understanding the effects of liner wear on SAG mill performance2021年2月23日 A centerless grinding machine is mainly used for all kinds of cylindrical parts, ring parts through grinding, as well as cone parts cutting grinding Grinder structure Cylindrical grinder is composed of bed and The difference between cylindrical grinding and 2018年2月6日 Grinding is the material removal and a surface finish process in which the material is removed from the work surface in the phase of small chips by process of tiny abrasive particles of grinding (PDF) A Review of Cylindrical Grinding Process
.jpg)
Wear of Electroplated CBN Grinding Wheels ResearchGate
2006年2月1日 An investigation is reported on the wear of singlelayer electroplated cubic boron nitride (CBN) grinding wheels and how, the wear process affects the wheel topography and grinding behavior2020年9月29日 Different from the microstructured CGDE and FGDMB tools, the wear form of the microstructured CVDD grinding tool was the coating shed at the edge of the microstructure, while the (PDF) Grinding wheel wear and material removal mechanisms 2022年3月1日 Since single crystal silicon is a typically hardbrittle and difficulttomachine material, the most commonly used method for silicon wafer thinning in 3D integration at present is backgrinding followed by chemical mechanical polishing (CMP) or etching (Jourdain et al, 2018), as shown in Fig 2Backgrinding is an abrasive machining process that uses sintered diamond An experimental investigation of silicon wafer thinning by Presence of Liquid: The most apparent difference is the use of liquid in the wet method Heat Generation: Dry method can produce more heat Particle Size: Wet method often results in finer particles Equipment Wear: Wet technique can be more abrasive, leading to faster wear and tearDifferences Between Wet and Dry grinding: Why Choose Wet
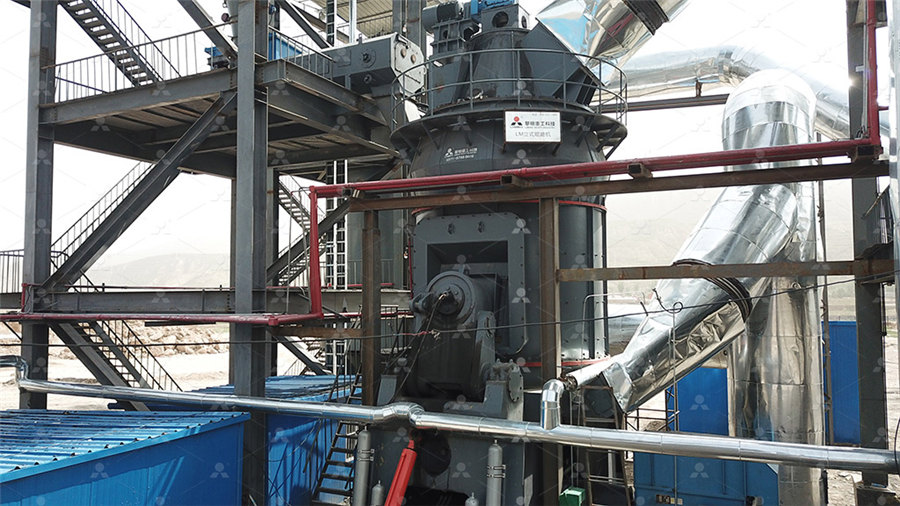
(PDF) Morphology and wear of high chromium and
2021年11月1日 Grinding wear behaviour of ADI was assessed during wet grinding at different pH of the mineral slurry The wear resistance of ADI was compared with that of forged En 31 steel balls under similar the stationary grinding wheel radial wear began, in which the radial wear increased linearly In this phase, the courses of the grinding wheel radial wear differed only slightly from one another at different dressing overlap ratios U d [12] 32 Quantitative model of grinding wheel wear Figure 3 shows the radial wear of the grinding wheel forInfluence of different grinding wheel and dressing roller 2023年5月8日 The external, watercooled grinding spindle is oriented at a fixed 12 degrees to the workpiece spindle to enable angular, infeed grinding and endface machining with peripheral grinding Having a maximum wheel diameter of 400 mm, it is said to provide the capability to provide material removal rates and wheel life of dedicated cylindrical grinding machines The Advantages of Turning and Grinding on One Machine Platform2018年10月20日 Cupwheels are frequently used to grind cermets, a difficulttogrind material An investigation was made into the transient geometry of the cupwheel rim, grit dulling, wheel loading, and wheel Impact of Cutting Speed on Grinding Wheel Wear and
.jpg)
Properties of grinding tool material for doubledisc straight
2021年4月7日 The doubledisc straightgroove (DDSG) grinding method is a new precision machining approach employed for the rolling surface of bearing rollers The friction coefficient and wear resistance of grinding disc materials affect the grinding performance due to the operation on the workpiece However, relevant research on DDSG is rather limited currently Therefore, we 2024年7月17日 Crushers are widely used in ore crushing, aggregate production, construction waste recycling, and natural stone processing Different crushers have various crushing methods, and different stages of crushing require Types of Crushers: Choosing the Right One for Each 2016年12月16日 The use of high pressure grinding rolls (HPGR) is growing in iron ore processing Because of the high technology of this kind of crusher, optimum utilization requires a thorough understanding of The wear pattern in high pressure grinding rolls ResearchGate2024年3月4日 In order to comprehend the abrasive wear mechanism of CBN grinding wheels with varying structural characteristic parameters, the influence of these parameters on abrasive wear was transformed into the impact of undeformed chip thickness on abrasive wear Subsequently, a twodimensional finite element simulation model of single CBN abrasive Research on the Wear of Groove Structured Grinding Wheel
.jpg)
Fundamentals of Double Disk Grinding Metal Cutting Corporation
2019年1月22日 Why grind with two wheels at once? True to its name, double disk grinding uses two opposing abrasive wheels to grind two sides of a material at the same time This makes it a very efficient grinding method for achieving a tight tolerance surface finish, flatness, and parallelism in the right applications2015年3月11日 The generation of the grinding wheel topography is described in many different models and approaches These models do not consider the influence of the dressing process on the wear of the grinding wheel In particular the prediction of this wear dependent on the dressing process parameters is not possible with the currently available models This article describes a Influence of the dressing process on grinding wheel wear2015年1月20日 PCBN offers high potentials in turning or milling of ferrous materials and highly heat resistant materials Due to its thermal stability PCBN achieves a longer tool life than PCD despite its lower hardness These properties currently lead to high production costs of the PCBN inserts Generally, plunge face grinding with diamond grinding cup wheels is the final Significant influence factors on the grinding tool wear and cutting 2017年9月23日 Lowalloy 70KhG chromium–manganese steel is investigated The thermokinetic diagram of supercooledaustenite conversion at cooling rates 003–84°C/s is plotted Appropriate heat treatment is developed for grinding balls of diameter 20–60 mm The microstructure of the steel formed in heat treatment is analyzed The temperature at which martensitic Production of grinding balls resistant to abrasive wear
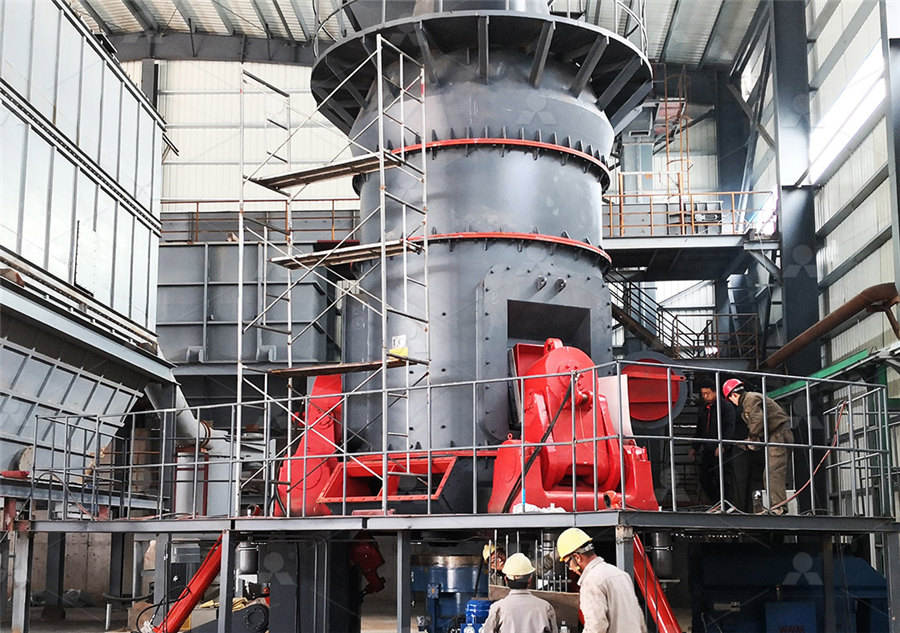
Precision Grinding: What It Is and Why It’s Important
Precision grinding can be performed on a variety of materials, including metals, plastics, and ceramics Types of Precision Grinding There are several different types of precision grinding, including surface grinding, cylindrical grinding, and centerless grinding Each of these methods is used to achieve specific goals and produce specific 2016年10月12日 Compare open circuit grinding and closed circuit grinding Open Circuit Grinding Open circuit grinding consists of one or more grinding mills, either parallel or in series, that discharges a final ground product without classification equipment and no return of coarse discharge back to the millClosed Circuit Grinding VS Open Circuit Grinding