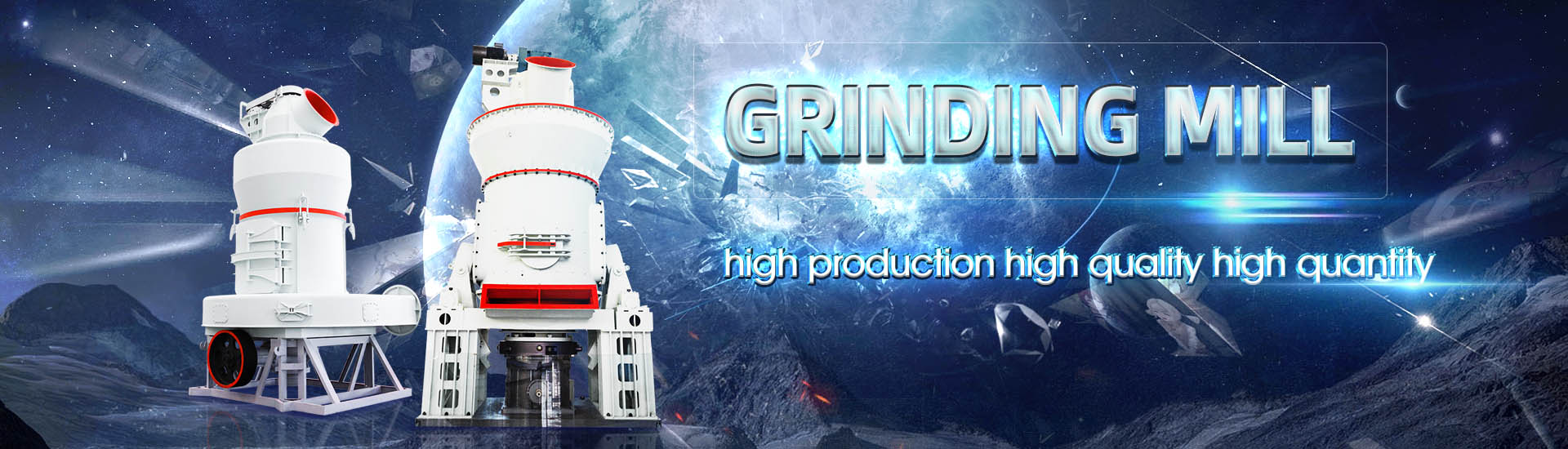
PF graphite silica grinding mill parameters
.jpg)
Analysis of process parameters in surface grinding with graphite
2003年10月1日 This paper deals with the application of Taguchi method for the analysis of process parameters in the new experimental setup in surface grinding with graphite as The results showed that LS−SDS had the best milling performance, the greatest grinding index, and a flowable slurry, indicating the potentiality of this formulation for the environmentally Improvement of Ball Mill Performance in Recycled Ultrafine 2019年3月1日 Orthogonal arrays and signaltonoise ratios are applied to study the performance characteristics of processing parameters The three main parameters applied in this study are Parameter Optimization of Ball Milling Process for Silica2023年12月7日 Bead milling can significantly reduce the production time of ultrafine graphite from graphite scrap from 72 h by ball milling to 10 min Ultrafine graphite scrap prepared from Ultrafine Graphite Scrap and Carbon Blocks Prepared by High
.jpg)
Effect of operational parameters on the breakage mechanism of
2008年4月1日 This paper focuses on the effect of operational parameters such as feed rate, classifier rotational speed and grinding pressure on the breakage mechanism of silica in terms 2021年11月1日 In this study, a novel graphite processing flowsheet based on highpressure grinding roller (HPGR), stirred grinding mill, and micro and nanobubble flotation columns has An innovative flake graphite upgrading process based on HPGR, 2021年2月19日 Taguchibased experimental design technique provides a systematic and efficient mathematical approach to understand complex process of ball mill process Comparative Study on Improving the Ball Mill Process Parameters 2019年1月1日 The basic process parameters in grinding processes are the cutting speed v c, the feed velocity v f, the depth of cut a e, and the width of cut a p (see Fig 1, see also Grinding Parameters SpringerLink
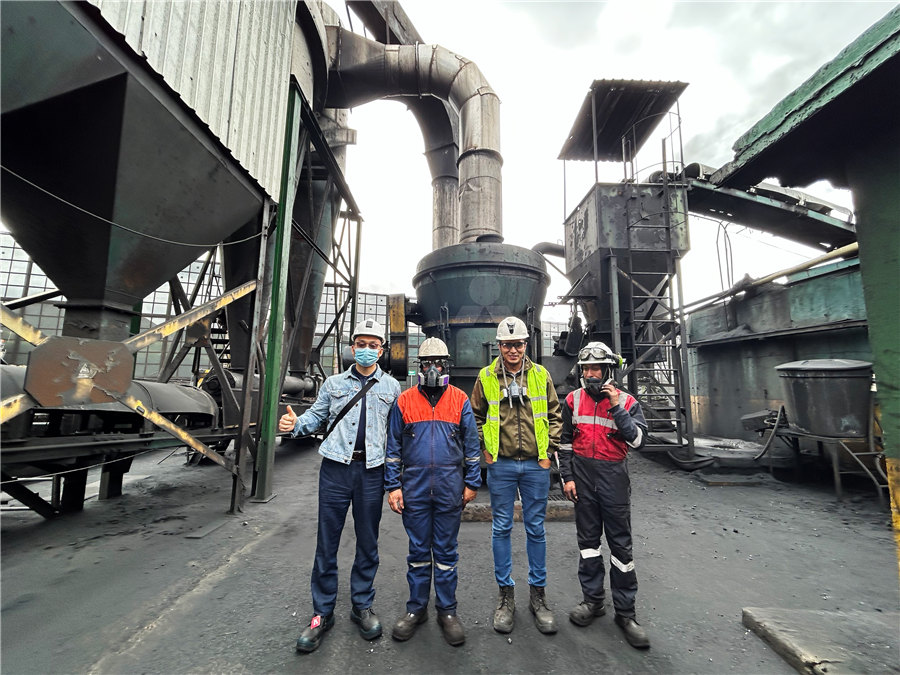
PAPER OPEN ACCESS Parameter Optimization of Ball Milling
2019年12月13日 Parameter Optimization of Ball Milling Process for Silica Sand Tailing To cite this article: Sukanto et al 2019 IOP Conf Ser: Mater Sci Eng 494 View the article Suggested Starting Parameters for Endmilling Graphite Cutting Diameter Machine Speed (rpm) Cutting Speed (sfm) Feed Rate (fpt)(in) Operation 1/64” 20,000 60,000Recommended Parameters for Graphite Machining by End Mills2012年6月1日 As the cylinder starts to rotate, the grinding balls inside the cylinder crush and grind the feed material, generating mechanical energy that aids in breaking bonds, activating the catalyst, and Grinding in Ball Mills: Modeling and Process Control2013年5月1日 Grinding, a complicated machining process which has been extensively studied and documented in order to understand the subtleties of the operation being performed in different methodologies and Influence of Process Parameters on Grinding A Review
.jpg)
Effects of grinding on Particle Shape: Silica and
2019年2月24日 Magnetite particle elongation and flatness parameter values of ball mill products in fraction sizes of 250+212 and 106+75 µm are larger than rod mill products, but roundness and relative width 2010年12月21日 The optimization of the operating parameters of a stirred media mill in the dry grinding of calcite was investigated A threelevel BoxBehnken design was used for the purpose of examining the Optimization of some parameters of stirred mill for ultrafine grinding 2015年5月10日 Generally, breakage rate depends on the material properties and mill parameters The linearity of graph proved the firstorder behaviour of grinding kinetics for the applied silica sand 6 Experimental modelling of breakage rate based on grinding parametersFig 5 Xray diffractogram of silica ground at various grinding period in oscillating mill 199 Fig 6 Change in Xray amorphization degree of silica with grinding period Massive aggregation was observed after 600 s as shown in Fig 4(c) and (d) Small particles in the range of 1 μm had aggregated to form a larger particle about 20 μm(PDF) Study on mechanochemical effect of silica for short grinding
.jpg)
Grinding aids for dry fine grinding processes – Part I: Mechanism
2020年7月1日 This study investigated ultrafine coal grinding performance of four low to moderatecost grinding media in a laboratory stirred mill Kinetic grinding tests showed that silica beads generated 2019年3月1日 The parameters used in the ball mill process are relatively large, however there are several parameters that have a significant effect on the reduction grain size produced This experiment was designed using the Taguchi method to find the optimum parameters in the production process of mircoparticles silica sand tailingParameter Optimization of Ball Milling Process for Silica2015年10月15日 Learn how to calculate the grinding capacity of your ball mill with 911 Metallurgist This guide provides essential formulas, to show the interrelations between treatments using the concepts of specific rateofbreakage/breakage distribution parameters and the more empirical methods A) Calculate Ball Mill Grinding Capacity 911MetallurgistIn this paper, the grinding of dry silica sand in a batch type planetary ball mill is reported The effects of various technical parameters, such as ball size and density of ball material, frequency of revolution of the equipment, volume of balls in the mill etc, on both the grinding rate and grinding limit are systematiThe Mechanism and Grinding Limit of Planetary Ball Millingt J
.jpg)
(PDF) Study on Preparation and Characterization of
2020年12月12日 Flake graphite, aluminum powder, and 304 stainlesssteel grit were used as the preparation materials The preparation parameters and process model were established based on the uniform design method2020年10月1日 The current study investigates the type of ratio for ball mill jars listed in Table 3 and [63,80,168,181,183] Different balltojar ratios can affect the milling kinetics, the size, and Silicon Powder Properties Produced in a Planetary Ball Mill as a 2023年3月21日 A rod mill has a cylindrical body similar to a ball mill, except instead of balls, it uses rods e rod system consumes 35–40% of the mill’s capacity [31]A Mini Review on Flotation Techniques and Reagents 2021年7月1日 Request PDF An innovative flake graphite upgrading process based on HPGR, stirred grinding mill, and nanobubble column flotation Physical upgrading of graphite is typically achieved with many An innovative flake graphite upgrading process based on HPGR,
.jpg)
On the Use of Ball Milling for the Production of Ceramic Powders
2015年4月22日 In the present research work the mixture of boron carbide and graphite ceramic powders with a theoretical composition of 50% each by weight were mechanically alloyed in a laboratory ball mill with 2013年5月9日 Thus, the material removal rate is known to increase with depth of cut Kumar et al [38] stated that the optimal combination of parameters is a wheel speed of 850 min −1 , a table speed of 15 m (PDF) Optimization of Process Parameters in Surface Grinding 2021年2月19日 A series of wet grinding experiments using calcite, pyrophyllite, and talc powder by a vertical type planetary ball mill, in which the size and distribution of grinding balls were varied with the Comparative Study on Improving the Ball Mill Process Parameters 2014年3月1日 The object of the study reported here is the grinding process in a tumbling mill where the mechanism of destruction by crushing is implemented, which is caused by the mechanism of compression loading(PDF) Analysis of ball mill grinding operation using mill power
.jpg)
An innovative flake graphite upgrading process based on
2021年11月1日 In this study, a stirred mill manufactured by Jilin Exploration Machinery Factory in China as well as the ball mill and rod mill manufactured by Wuhan Exploration Machinery Factory in China were evaluated comparatively for their performance in mineral liberation and graphite flake protection during the grinding and regrinding processes (Fig 3)2017年3月20日 Ball mill process parameters for five ground samples with ball load J = 050, particle filling U = 053, mill speed N c = 71% and mill factor F c = 069 Shape and size factors equation and Physicochemical Problems of Mineral Processing Investigation 2012年9月12日 In this work nanoparticle silica was synthesized using silica sand and quartzite by top down approach using ultrafine grinding Silica sand was obtained from Bangka island while quartzite rocks Preparation Of Nanoparticle Silica From Silica Sand 2001年1月15日 The kinetics of batch wet grinding of quartz from a feed of 600×425 μm to a product of 80% less than 8 μm have been determined using sieving and laser diffractometer sizing for size analysisKinetics of Fine Wet Grinding in a Laboratory Ball
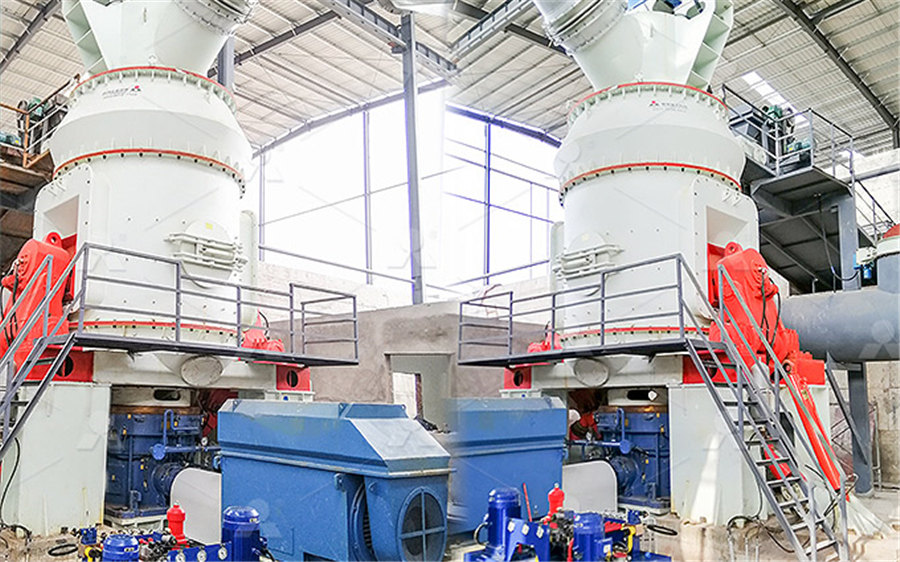
Production of Silicon Carbide via Grinding and Heat
2014年1月1日 Under ambient conditions, silica (SiO2) and graphite (C) were milled in a ring mill at up to 18 000 s, followed by heat treatment at 1000 °C A SiO2–SiC nanocomposite with a ratio of 863:137 Chinese Journalof Engineering T : Parameters optimization experiments results Experiment BPR Jar volume Rotation speed Particle size ( m)Research Article Process Parameters Optimization of Silica Sand 2020年6月15日 Grinding of a metallurgical grade silicon quality provided by Elkem ASA, Silgrain® eSi 410 was studied through a series of laboratoryscale experiments using a stirred media millEffect of operation parameters and formulation on the 2017年1月1日 An increase of over 10% in mill throughput was achieved by removing the ball scats from a single stage SAG mill These scats are non spherical ball fragments resulting from uneven wear of balls (PDF) Performance optimization of an industrial ball mill for
.jpg)
OPTIMIZATION OF MILLING PARAMETERS OF PLANETARY BALL MILL
2018年11月1日 Nano rice husk ash particles were prepared from completely combusted rice husk by ball milling These particles were successfully reinforced in Al6061 metal matrix through ultrasonicatorassisted 2023年4月23日 pending on the process parameters which are fill rate, mill spe ed, ball diameter, ball shape and grinding time [41] In the ball mill, friction is formed due to the difference between surfa ces (PDF) Grinding Media in Ball MillsA Review ResearchGate2017年1月10日 This paper evaluates the effects of operating parameters on fine particle grinding process with a vertically stirred media mill The effects are investigated through size reduction under different Effect of operating parameters on fine particle grinding in a 2013年4月16日 Ultrafine grinding involves a large number of parameters in its operation In this paper, four important parameters of the Drais stirred ball mill, ie, the bead density, slurry density, mill Investigation of some parameters affecting the Ultrafine grinding
.jpg)
Dry grinding in planetary ball mills: Evaluation of a ResearchGate
2017年11月1日 Planetary ball mills at laboratory scale are widely used for grinding and alloying processes However, in contrast to other mill types, no applicable mechanistic model exists to describe the 2020年7月23日 Optimization of stirred mill parameters for fine grinding of PGE bearing chromite ore, Particulate Science and Technology, DOI: 101080/2020 To link to this article: https://doi Optimization of stirred mill parameters for fine 2023年3月8日 PF Impact Crusher uses impact energy to crush the materials The rotor rotates at a high speed under the driving force of motor The materials entering from the inlet impacts the plate hammer on the rotor and would be crushed under PF Impact Crusher SBM Mill CrusherThe new generation of stirred mills like the IsaMill has fundamentally changed the economics of fine grinding This has made them enabling technology for several existing and planned operations, and has opened new fields of processing in hydrometallurgy These opportunities are made possible by the unique combination of features of stirred mills : • Very high intensity Fine Grinding as Enabling Technology – The IsaMill
.jpg)
(PDF) Estimation of Grinding Time for Desired Particle Size
The performance of grinding mills depends on many operating factors among which are the time of grinding, mill speed and low silica low alumina The grinding process for all the three iron the P80 passing percentage was 75 μm, 100 μm, and 140 μm, respectively When compared with mineralogical and grinding parameters, it can be 2 Through microgrinding experiments, this paper explored the relationship between the machining quality of CVD diamondcoated microgrinding tools and grinding parameters when processing fused silica The results showed that the machining quality improved with increasing feed speed and grinding depth but decreased with increasing spindle speedMachining performance and wear mechanism of CVD diamond 2020年8月1日 This study investigated ultrafine coal grinding performance of four low to moderatecost grinding media in a laboratory stirred mill Kinetic grinding tests showed that silica beads generated Evolution of grinding energy and particle size during dry ball 2019年10月1日 Firstly, the conventional ball mill parameters such as mill speed (% of critical speed), material filling ratio (Jb), ball filling ratio (fc), ball size distribution (10203040 mm, %), grinding Wet and dry grinding of coal in a laboratoryscale ball mill: Particle
.jpg)
Effect of grinding media on the milling efficiency of a ball mill
2022年1月1日 The size of grinding media is the primary factor that affects the overall milling efficiency of a ball mill (eg power consumption and particle size breakage)2019年8月1日 Silica was stabilized electrostatically by adding caustic potash at a pH value of 75 Zinc oxide was stabilized The millrelated coefficient is determined from the power consumption of the mill at the given parameters when operated with Fine grinding: how mill type affects particle shape characteristics and mineral Mill, material, and process parameters – A mechanistic model for