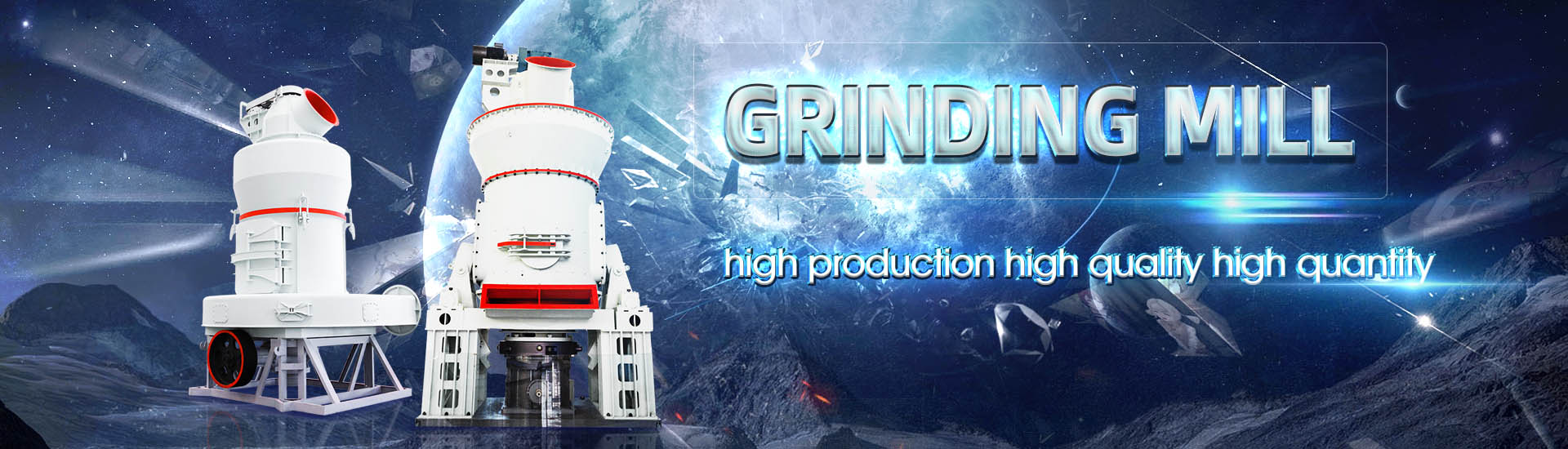
Zhongkong raw material vertical mill operation
.jpg)
Vertical roller mill for raw Application p rocess materials
Vertical roller mills are adopted in 20 cement plants (44 mills) in Japan In the vertical roller mill which is widely used in the raw material grinding process, raw materials input grinding table Process parameters like feed size, moisture content, product fineness, and material properties affect mill operation and performance Common issues and corrective actions are also outlined The document discusses vertical mills VRM Operation and Optimization PDF Mill 2016年9月1日 The results demonstrated that the VRM unit consumes around 81% (975 kWh/t of raw materials), and 36% (58 kWh/t of raw materials) more energy to grind raw material than Operational parameters affecting the vertical roller mill The document discusses optimization and operation of vertical roller mills (VRMs) Key points include: 1) Continuously monitor and adjust process parameters to find the optimum operating conditions of highest capacity and Optimization of Vertical Raw Mill Operation PDF
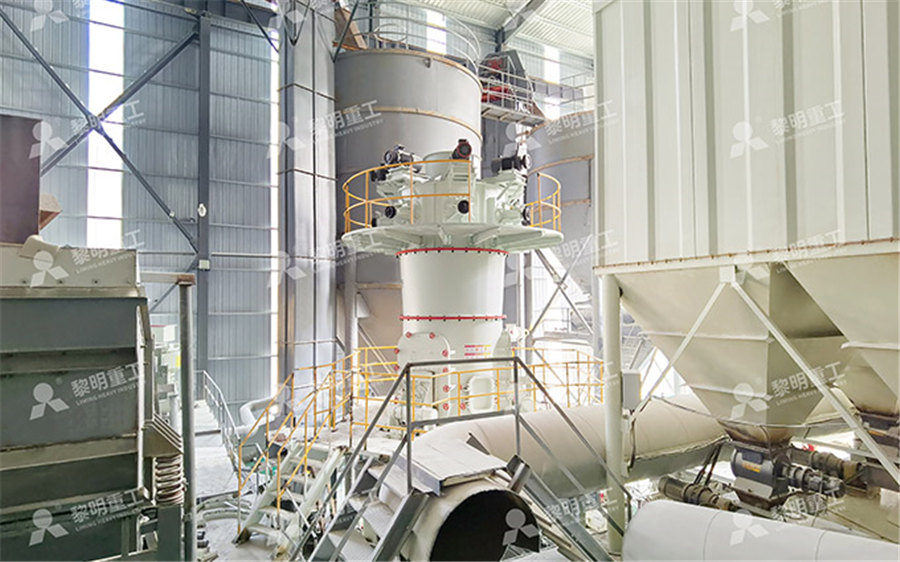
Analysis of vertical roller mill performance with changes in material
2022年5月31日 The vertical roller mill (VRM) is commonly used for secondary and tertiary crushing processes in numerous industries In this study, the discrete element method (DEM) Vertical Roller Mills Pressure Profile Draw Up Curve Influenced by: •Mill Inlet Pressure •Nozzle Ring Coverage •Classifier Speed •Dam Ring Height •Mill Load •Material Blockage in Hot Gas Optimization of VRM Operation RUCEMRU2017年4月1日 Vertical roller mills (VRM) have found applications mostly in cement grinding operations where they were used in raw meal and finish grinding stages and in power plants Operational parameters affecting the vertical roller mill 2024年1月15日 An industrialscale vertical roller mill (M600) was analysed for air flow in this study This led to proposed modifications, which were implemented in a new mill design Optimisation of the performance of a new vertical roller mill by
.jpg)
PROCESS OPTIMISATION FOR LOESCHE GRINDING PLANTS
vertical roller grinding mills for grinding: • Coal • Cement raw material • Clinker / granulated slag • Industrial minerals, and • Ores The core elements of these plants are the Loesche vertical Grinding aids (GAs) are polar chemicals introduced in cement mills in either liquid or powder form to improve on mill grindability efficiency Studies have shown that some GAs not only help in grinding efficiency but also play vital roles in (PDF) CEMENT RAW MATERIAL GRINDING ; VERTICAL Dry Grinding: Open circuit Ball mill, closed circuit Ball mill, vertical roller mill, Roll Press or Roll press in circuit with ball mill However, it would be seen that the most significant process and types used for raw material grinding operations in modern cement industry are: Process: Dry Closed circuit drygrinding Type of mill: Ball and Raw Material DryingGrinding Cement Plant OptimizationOptimizationofVerticalRawMillOperationpdf Free download as PDF File (pdf), Text File (txt) or view presentation slides online The document discusses optimization and operation of vertical roller mills (VRMs) Key points include: Optimization of Vertical Raw Mill Operation PDF
.jpg)
Vertical Raw Mill PENGFEI Group
The vertical raw mill has high grinding efficiency Due to innovative materialgrinding principle, it reduces power consumption by 2030% as compared with ball mills The higher the feeding material moisture content, the more energy 2017年9月11日 Due to the compact design and material transportation system of vertical roller mills (VRM), some important streams (total mill feed and discharge, dynamic separator feed and reject) remain in the (PDF) Performance Evaluation of Vertical Roller Mill inFind your ideal job at Jobsdb with 228 Raw Material jobs found in Hong Kong View all our Raw Material vacancies now with new jobs added daily!Raw Material Jobs in Hong Kong Oct 2024 JobsdbFIGURE 4 Particle size distributions of collected samples (Survey 2) Bond work indices and breakage characteristics under compression were determinedPerformance Evaluation of Vertical Roller Mill in Cement
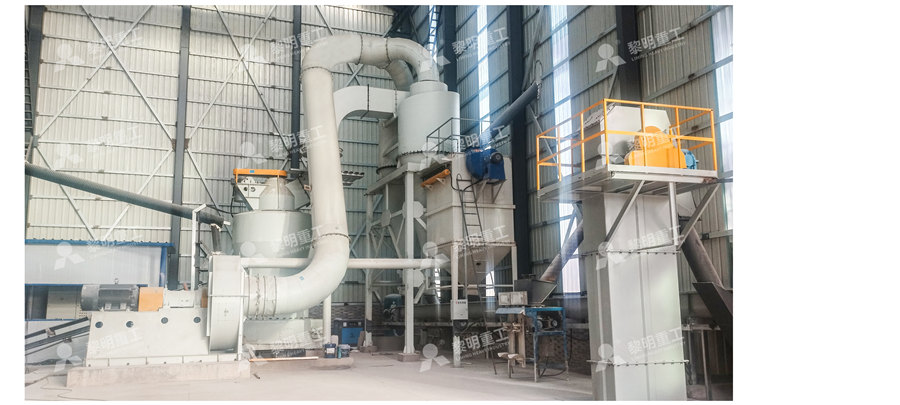
PROCESS OPTIMISATION FOR LOESCHE GRINDING PLANTS
• Cement raw material • Clinker / granulated slag • Industrial minerals, and a vertical roller mill (VRM) ously for realtime optimisation • The key to mill optimisation is stable operation of the plant Only with stable operation can greater performance be achieved and thus added value beCement production globally is estimated at 42 billion tons in 2019, and cement grinding consuming approximately 20 percent of the total available electrical energy (Ghalandari, Majd, Golestanian, 2019; A I Okoji, Anozie, Omoleye, Taiwo, Osuolale, 2022b)Consequently, cement plants consume an average of 100 kWh per ton of cement produced, with twothirds of Assessment of the thermodynamics efficiency of a cement vertical raw The raw vertical mill of CHAENG has stable operation, high output and convenient replacement of parts It has been recognized and purchased by customers in South Asia, Africa and other markets: 1 A 5000t/d cement production line EPC turnkey project in South Africa adopts GRMR5341 raw material vertical mill of CHAENG 2Vertical Raw Mill CHAENG7 // Almost any plant for the grinding of cement raw material is a combination of machines specially adapted to the particular physical properties of the material to be ground As a result, our plants work efficiently without any trouble » Highly efficient grinding, drying, and separating in one unit » Outstanding production capacities exceeding 1,400 t/h in one single millPFEIFFER MILLS FOR THE CEMENT INDUSTRY

Best HLM Vertical Roller Mill Manufacturer and Factory
As the vertical roller mill works, the motor drives the reducer to rotate the dial, the raw material are delivered to the center of the dial from the air lock rotary feeder The material moves to the edge of the dial due to the effect of centrifugal force and than be ground by the force of the roPROCESS TRAINING for operators of Vertical RAW Mills Heating of mill and grinding plant For drying the wet raw material it is necessary that prior to the mill start up the grinding plant isheated for some timeOtherwise the cold PROCESS TRAINING for operators of Vertical RAW Mills2021年1月1日 Stacking Reclaiming of Raw material: Swing type stacker Reclaimer: Limestone other raw material are stored in open area into a longitudinal storage unit called stockpile through Stacker These are then extracted transversely from the stockpile through reclaimer: 3: Raw Meal Grinding Homogenization: Grinding Mill Vertical Roller Mill Review on vertical roller mill in cement industry its The advantages of the modular vertical roller mill technology are evident in the results from a case study about a modular vertical roller mill 5000 – 4 roller raw material mill in operation in Grinding Process Optimization Featuring Case Studies and
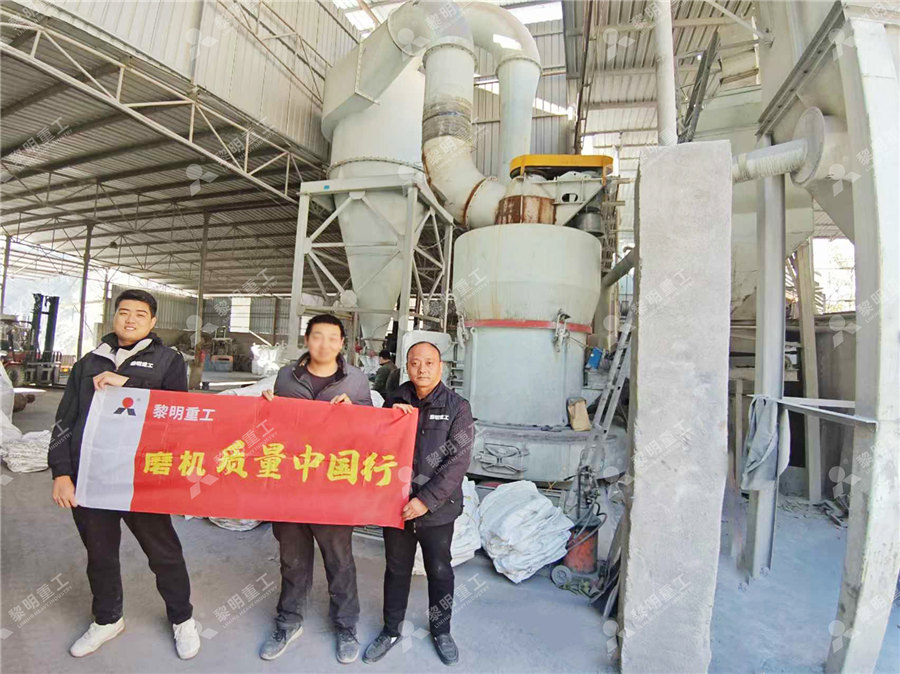
Cement Application Page Vertical Raw Mill Promecon
This is particularly important for consistent control in the dynamic environment of a Vertical Raw Mill Temperature Resistance up to 1000 °C/1800 °F: The ability to withstand high temperatures in a Vertical Raw Mill allows for accurate measurement and control under extreme conditions, contributing to the efficiency of the milling process4 650 kW Even with poor grindability of the raw material this mill is expected to produce an output of 640 t/h at a raw meal fineness corresponding to a residue of about 15 % on a 009 mm sieve The first Loesche mill equipped with six rollers will come into operation in early summer 2007 in a cement works in the USA The development of this Redundancy and interchangeability – large vertical roller mills The vertical mill allows the installation area to be decreased, leading to a reduction of construction cost 3 Easy operation Material feed, grinding force, air volume and separator feed can be adjusted through a remote control system, which makes the operation easier 4 UBE Vertical Mill UBE Machinery Corporation, Ltd2021年1月29日 Vertical roller mills, VRMs, are widely used for grinding raw materials in factories engaged in the extraction and processing of minerals Any machine used for grinding or crushing consumes around Increase productivity of vertical roller mill using seven QC tools
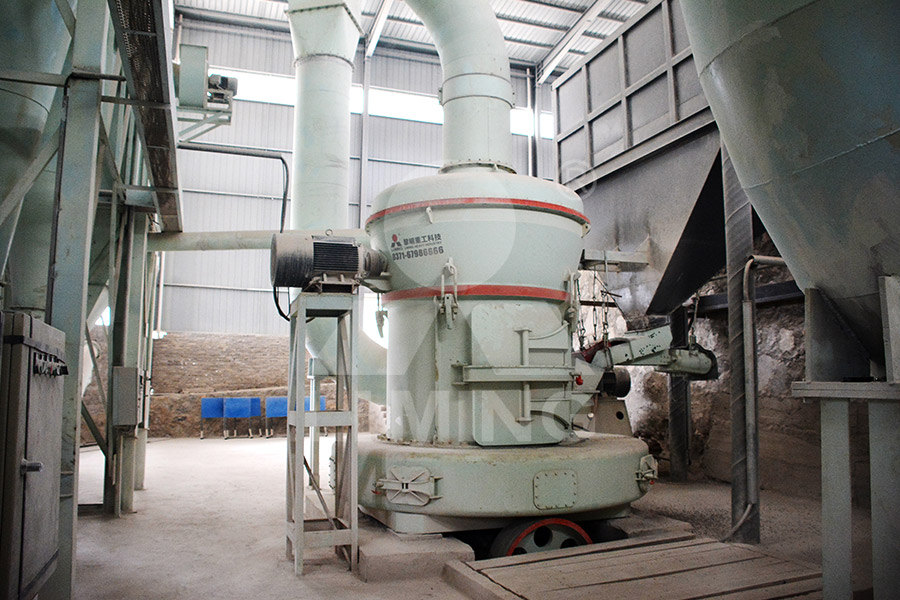
(PDF) The latest innovative technology for vertical roller mills
2014年4月1日 For decades vertical roller mills have been in use in the cement industry for the grinding of cement raw material and coal Since the 1980's this mill type has also been used for combined or The vertical grinding water spray system plays an important role in stabilizing the material bed, especially in the case of more powdery materials or low water content in the raw materials, the effect is more obvious, the toughness and rigidity of the material can be increased, and the material grinding is facilitated, protect the roller surface and the grinding discImportant Operation Tips For Cement Vertical Mill2024年2月23日 The operation of the cement raw mill is a critical step in cement production By grinding the raw materials into a fine powder, these powders can be more easily mixed with other cement ingredients and burn more evenly How Does a Raw Mill Work in a Cement IndustryWorking principle and characteristics of vertical mill Working principle The working principle of a vertical mill involves the rotation of a grinding table with rollers attached to it Raw materials are fed into the table and ground between the rollers and table The ground materials are then blown by hot air through an outlet in the mill's Working principle and characteristics of vertical mill
.jpg)
Modeling and simulation of vertical roller mill using population
The cement raw materials (lime, silica and iron ore) enter the circuit through two apron feeders The raw materials are crushed in a hammer crusher to D 95 of 80mm The raw materials are mixed in a certain proportion and fed into a vertical roller mill (LOESCHE mill) The vertical roller mill grinds the marital to D 85 of 90µm2024年3月17日 Milling is a popular machining process Milling is a machining operation in which a revolving cutter removes material from a workpiece in a controlled manner This method of subtractive manufacturing seeks to give the workpiece the desired shape In milling operations, rotary cutting tools, typically equipped with multiple teeth or edges, are employed to precisely 16 Types of Milling Operations Explained [with PDF] The First vertical mill for cement grinding Gebr // In 1864, company founder Jacob Pfeiffer had a vision of grinding mineral raw materials on a large scale This idea became reality Today the company looks back on a longtime success story of developing the mill in the world in operation 2017 ready2grind – World’s fi rst modular PASSION FOR GRINDING2024年7月16日 From transforming raw materials into desired shapes, milling operation plays Get Quote Services This operation is performed using a face mill, which contains multiple cutting edges on both the end and outside diameter of the tool Common Applications Machines used typically include vertical or horizontal milling setups, 23 Types of Milling Operations: Learn About Milling Processes
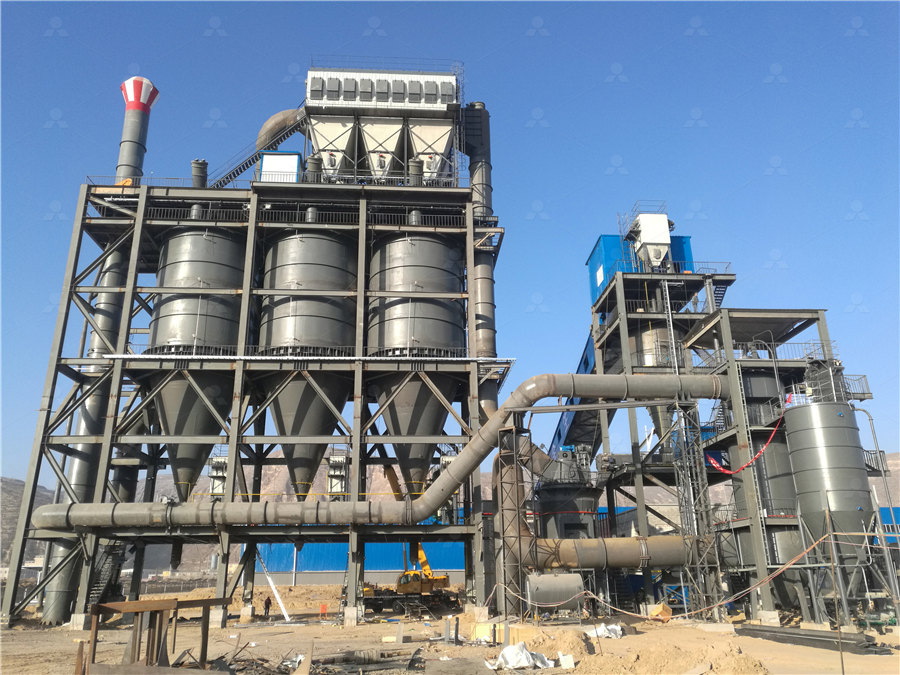
Raw mill Cement Plant
Raw mill is generally called cement raw mill, raw mill in cement plant, it refers to a common type of cement equipment in the cement plantIn the cement manufacturing process, raw mill in cement plant grind cement raw materials into the raw mix, and the raw mix is sent to the cement kiln to make cement clinker, next, clinker and other admixtures will be ground into finished cement by the main raw materials of clay (clay) and limestone (limestone) into clinker which is then added with some corrective materials such as pozzolan, gypsum, fly ash, etc at the final stage (finish EVALUASI KINERJA VERTICAL ROLLER MILL (Cement Mill)This is particularly important for consistent control in the dynamic environment of a Vertical Raw Mill Temperature Resistance up to 1000 °C/1800 °F: The ability to withstand high temperatures in a Vertical Raw Mill allows for accurate measurement and control under extreme conditions, contributing to the efficiency of the milling processCement Application Page Vertical Raw Mill PromeconWe can design and manufacture vertical roller mills of diversified specifications and models for raw meal, cement, and slag comminuation systems in cement clinker production lines with capacity up to 10,000t/d To continuously meet the needs of grinding various materialsVertical Roller Mill (VRM)SinomaLiyang Heavy Machinery Co, Ltd
.jpg)
OK RAW AND CEMENT MILL
available for raw grinding, ensure the ability to meet all possible capacity requirements in a single mill even for the hardest materials The wellknown reputation of the OK mill as a reliable machine that is easy to operate and maintain continues with the OK raw mill In addition to the roller design features, the OK mill retains the abilityFor the preparation of cement raw material, cement, and granulated blastfurnace slag with small to medium output rates, the MVR mill with conventional drive is the right choice This mill type is by the way the core piece of our modular ready2grind systemMVR vertical roller mill with planetary gearbox Gebr PfeifferThe vertical grinding mill grinds materials by the principle of material layer grinding, with low energy consumption The power consumption of the grinding system is 20% to 30% lower than that of the ball mill, and the energy saving effect is more obvious as the moisture of the raw material increasesIndustrial Vertical Grinding Mill2020年5月1日 Vertical roller mill (VRM) is a type of heavyduty and energyintensive grinding equipment for many industries, such as cement, steel and chemical industries It is used to grind slag, nonmetallic ore and other block and granular raw materials into required powder materials The fine powders can be used as raw materials for cement productionA datadriven decisionmaking framework for online control of vertical
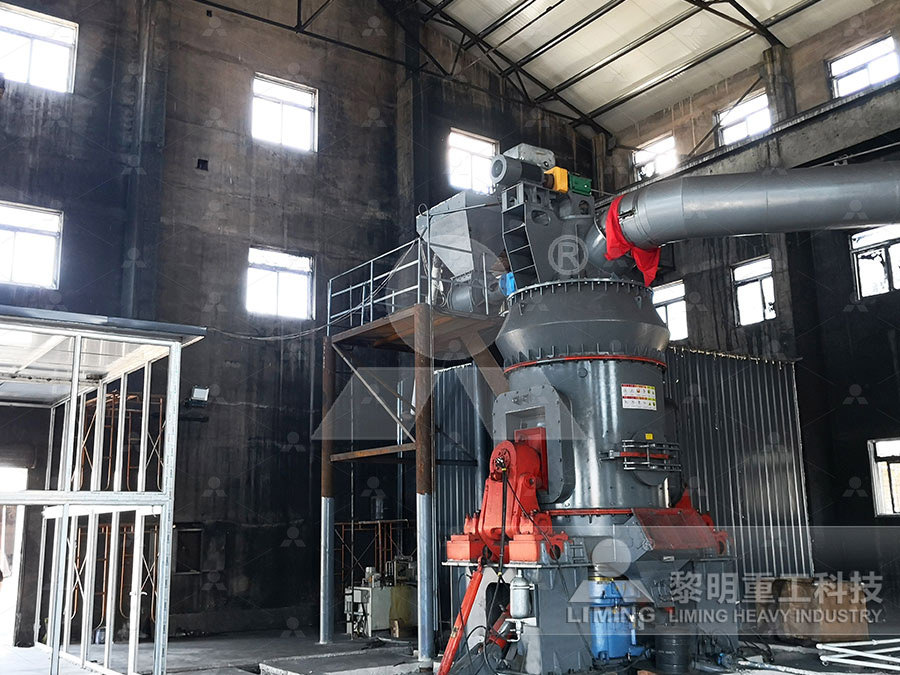
Docslide Net Optimization of Vertical Raw Mill Operation PDF
Vertical roller mills (VRMs) require optimization of key process parameters to achieve maximum grinding capacity at minimum energy consumption Operators should continuously monitor parameters like product fineness, classifier speed, grinding force, air flow, and power usage to maintain optimal performance as feed materials change Relevant parameters that influence vertical planetary gear reducer At the same time, raw material is dried by hot gas induced through the louver ring installed at outer side of the table Construction This Machine is a vertical type roller mill which performs drying grinding classification and pneumatic transportation simultaneously Material is fed at aVERTICAL ROLLER MILLS AMCL2023年1月19日 OptimizationofVerticalRawMillOperationpdf Download as a PDF or view online for free Grindability of Raw Material •Grinding Fineness •Classifier Design •Grinding Bed Height / Variations •Dam Ring Height •Air Flow •Temperature Level •Condition of Grinding Elements Power Consumption Mill Drive 8OptimizationofVerticalRawMillOperationpdf SlideShare2023年6月8日 VRM data from a steady plant process operation, such as raw material output, material moisture, kiln hot gas The vertical raw mill proc ess was mode lled in this study using ASPEN Plus V102 Assessment of the thermodynamics efficiency of a cement vertical raw