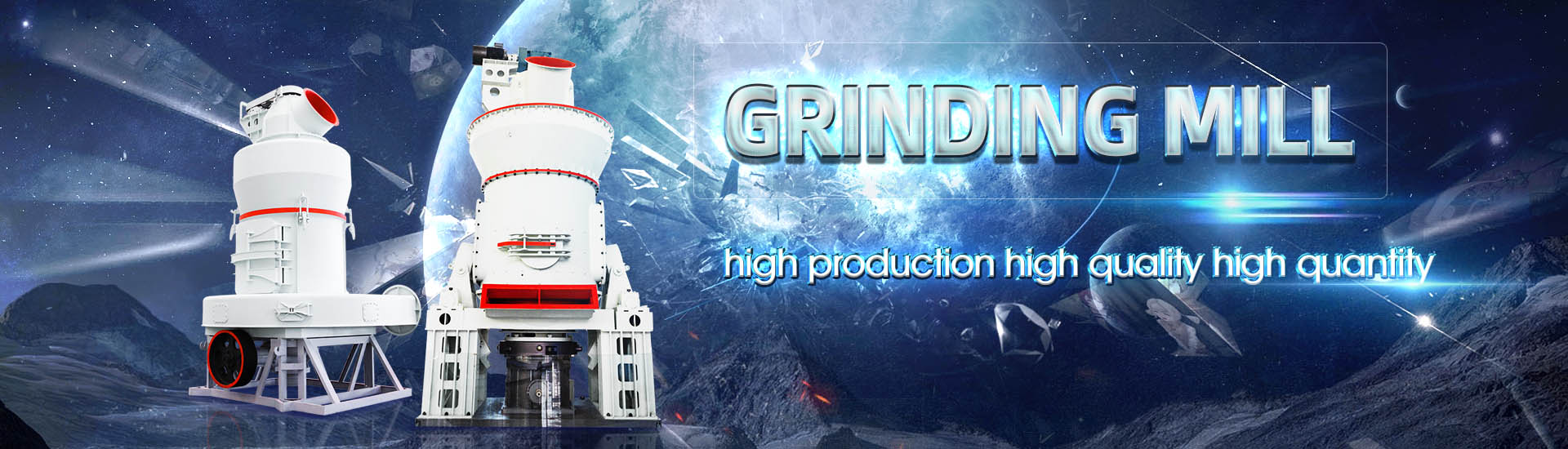
Particle grinding system
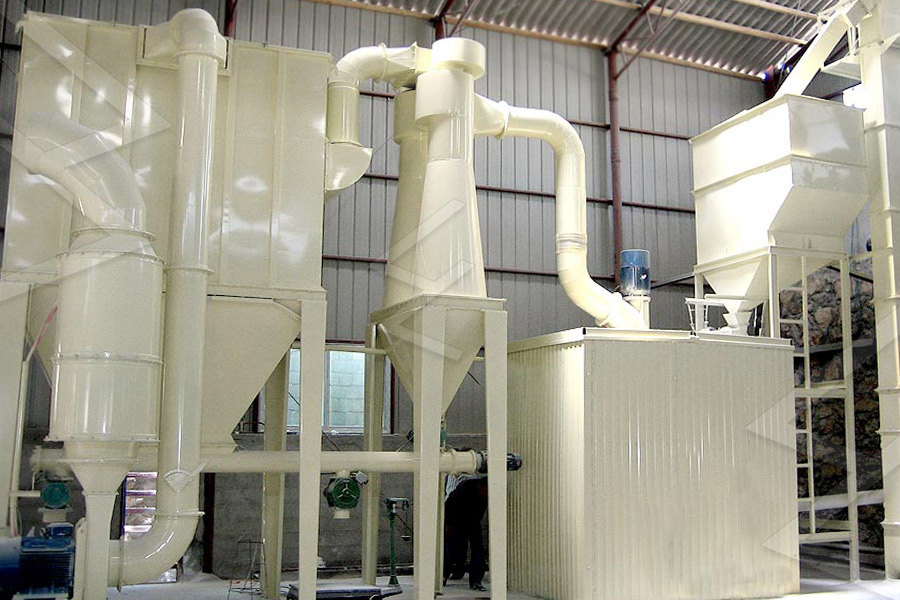
PolarFit® UltraFine Grinding Mill Air Products
Our PolarFit® ultrafine grinding mill is a versatile grinding system that provides a costeffective way to reduce hard to grind materials to smaller particle sizes than can be achieved with conventional impact millsBepex offers advanced small particle grinding and micronizing systems, solutions, and engineering support for tough small particle challenges No job is too large – or particle too Fine Grinding Machines and Micronizing Equipment BepexAir Products’ PolarFit® cryogenic grinding solutions can help you grind more effectively and efficiently, particularly for heat sensitive or toughtomill materials Whether you have an existing cryogenic or ambient milling system that you PolarFit® Size Reduction Systems Air ProductsOur ultrafinegrinding system uses the cooling power of liquid nitrogen to remove heat produced in the grinding process by controlling the temperature of your product or the mill Key benefits PolarFit™ UltraFineGrinding Mill Air Products Chemicals
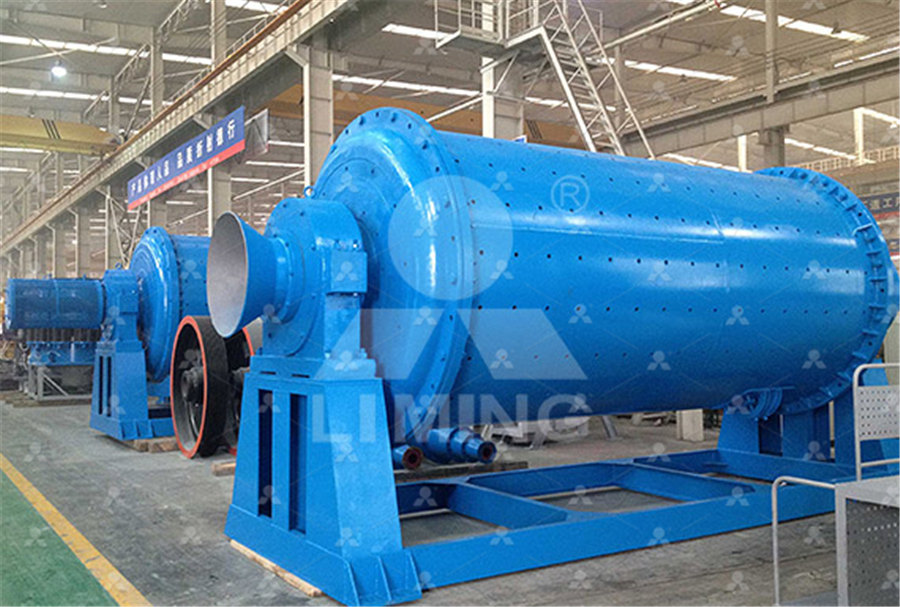
EnergyEfficient Advanced Ultrafine Grinding of
2023年7月10日 The present literature review explores the energyefficient ultrafine grinding of particles using stirred mills The review provides an overview of the different techniques for size reduction and the impact of energy 2020年9月1日 The article provides an automatic particle size control technology, which uses advanced particle analysis research technology and modern motor variable frequency control Automatic grinding particle size control technology and equipment2024年5月15日 Grinding experiments on both Inconel 718 superalloy and zirconia workpieces with flat and curved shapes have demonstrated excellent highshear and lowpressure A highshear and lowpressure intelligent precision grinding Gain advice and best practice on Quadro’s milling and particle size reduction technology by viewing our application bulletins, technical videos and brochures Discover the Scalable Lab System™ (SLS), the world's most advanced bench Contained Milling and Particle Size Reduction
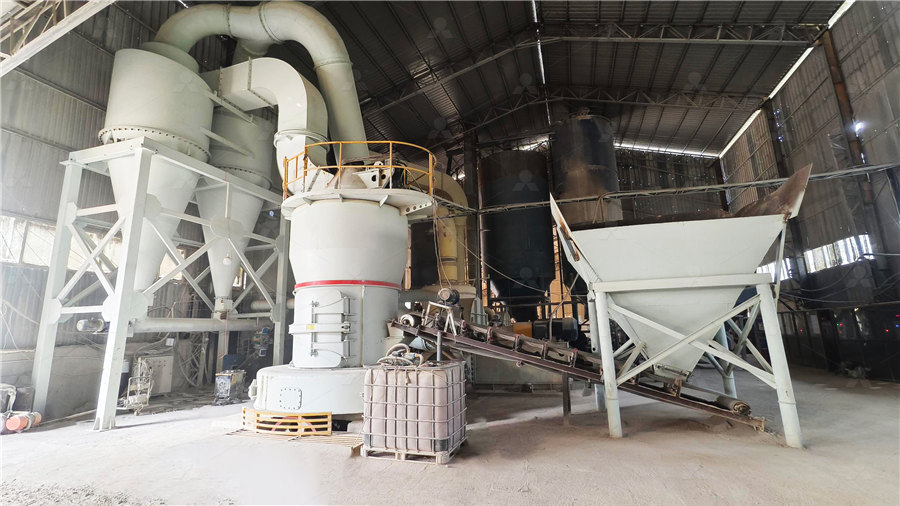
Grinding Milling Powder ProcessSolutions
Powder processing often involves bulk powders, additives, or ingredients being milled for particle size reduction A mill or grinder uses a mechanical action to break the material and reduce it to the required size This may encompass a 2022年2月28日 Recently, however, the HPGR has replaced many of the traditional dry grinding systems in this industry [6, 83, 84] HPGR is equipped with an interparticle breakage mechanism system in which materials are broken, crushed, and ground by compressionGrinding SpringerLink2020年9月1日 Automatic grinding particle size control technology and equipment Zhijing Li 1, Yuxuan Wang 1, Zhongwu Jin 1 and Yinjun Zhou 1 Published under licence by IOP Publishing Ltd Li Hui 2018 Application of online particle size analyzer in cement grinding system [J] China Cement 196 105107Automatic grinding particle size control technology and equipmentThe grinding system has influence on: Particle Size Distribution and Shape The particle size distribution is presented in the RRSBdiagram as shown in Figure 3 and characterized by: ¨ Steepness of curve n (tand) ¨ Limiting particle d’ (36,8 [%] R)CEMENT GRINDING SYSTEMS INFINITY FOR CEMENT EQUIPMENT
.jpg)
Powder Toll Processing, Milling Grinding Custom Particle
Being equipped with a range of different milling and grinding technologies enables our operators to provide the best solution for meeting your dry material processing requirements Our facilities are FDA Registered, and our manufacturing, quality, and safety procedures follow GFSI, SQF, ISO, and OSHA guidelines2023年7月10日 The present literature review explores the energyefficient ultrafine grinding of particles using stirred mills The review provides an overview of the different techniques for size reduction and the impact of energy requirements on the choice of stirred mills It also discusses the factors, including the design, operating parameters, and feed material properties, EnergyEfficient Advanced Ultrafine Grinding of Particles UsingBepex offers advanced small particle grinding and micronizing systems, solutions, and engineering support for tough small particle challenges No job is too large – or particle too small (at least where grinding is concerned!) Reach out to your Bepex process engineering expertFine Grinding Machines and Micronizing Equipment Bepex2024年7月1日 In addition, the particle size of the powder has a significant impact on the curing performance and rheological properties of the slurry [26]Li [27] introduced coarse silicon powder into a Si 3 N 4 photocurable slurry, changing the particle size distribution from a unimodal (05 μm Si 3 N 4) to a bimodal distribution (05 μm Si 3 N 4 + 5 μm Si mixed powder)Digital light processing of highstrength Si ScienceDirect
.jpg)
Grinding Mill Comparing Grinding Mill Systems Their Uses
2018年5月10日 There is no single grinding system that can do it all! Choosing the appropriate milling system is based on your particle size distribution requirements, feed material sensitivities, moisture content, hardness, flow (freeflowing, semifree flowing or prone to bridging/plugging), melting point, brittleness, and abrasiveness, among other factorsParticle reduction techniques are commonly employed in industries such as pharmaceuticals, food processing, and materials manufacturing, where fine or controlled particle sizes are desired 3 Grinding: Grinding is a mechanical process that involves the abrasion or attrition of materials to achieve particle size reductionCryomilling / Particle Reduction / GrindingThe SLS Scalable Lab System ™ gives the reassurance that particle sizes and distributions achieved in the lab can be directly transferred to the productionscale equipment The operating parameters are simply transposed from smallscale to fullscale productionLab Scale Milling and Processing MachineSystem Solution Pumping solutions like NEMO ® progressing cavity pumps or PERIPRO peristaltic pumps are the important machines in battery producing lines, that have been used to convey many kinds of glue and battery slurry and so on mediums, as the dosing and metering pumps, mainly application in the battery slurry process and coating procedure The axial Grinding NETZSCH Energy
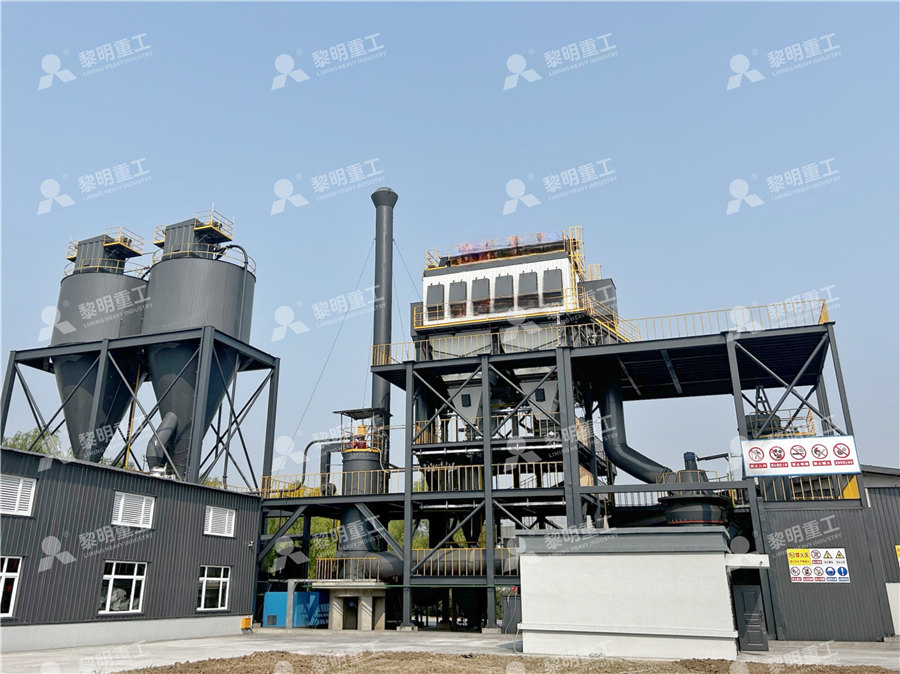
Grinding considerations when pelleting livestock feeds
grind (smaller finished particle size), energy and maintenance costs increase and, everything else being equal, the capacity of the grinding system will be reduced The cost(s) of grinding The cost of grinding can be broken down into three general categories: Equipment cost, energy cost and maintenance costSentry Air Systems’ lightuse Portable Grinding Dust Collectors Extractors are designed for carbon steel, stainless steel, cold rolled steel, plastic, copper, and beryllium applications; more specifically for maintenance grinding where Grinding Dust Sentry Air SystemsPolarFit Size Reduction Systems Air Products experienced engineers can help determine which PolarFit system is best for your operation based on your current system, the material you process, and your goals—whether it’s our turnkey cryogenic grinding system or components of the system that we retrofit to your existing equipment Below areCryogenic Applications PolarFit® Cryogenic Grinding Solutions 2022年5月20日 Where d GM is the grinding media particle size diameter, ρ GM is the grinding media density, and v t is the tip speed of the stirrer in the mill (Kwade 2003) Although this model does not consider process parameters to estimate product quality, it was shown to work on hard inorganic materials (Kwade and Schwedes 2002)Mechanical ParticleSize Reduction Techniques SpringerLink
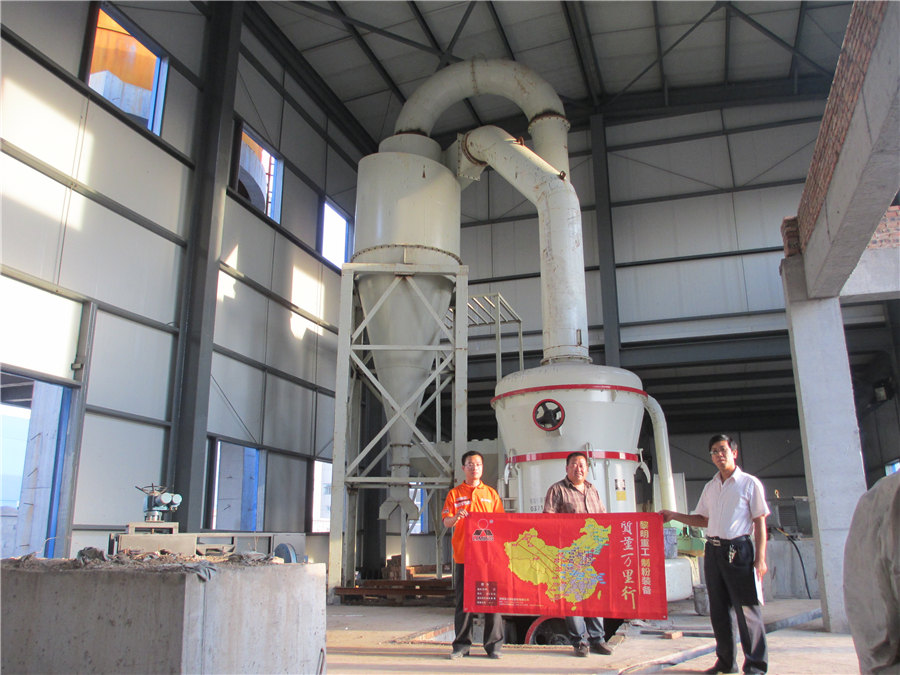
THE IMPROVEMENT OF GRINDING AND USING CLOSED CIRCUIT SYSTEM
with each system For the same median particle size, the product yield with the mechanical grinding system was higher than that with the jet grinding system, because the mechanical grinding system produced fewer particles less than 5 µm Figure 6 shows the relation between the median particle diameter of product and the specific energy a light source to eliminate the influence of reflection on inspection, and to enhance the edge of images The captured images are provided in Figure 4, Figure 5 and Figure 6A Novel Apple Size and Surface Quality Detection and Grading System2024年5月15日 To bridge the gap, a highshear and lowpressure intelligent precision grinding system has been developed Examination of the surface morphology of zirconia ceramics after grinding reveals that the particle clusters enable cutting to occur in the plastic deformation region of the brittle materialsA highshear and lowpressure intelligent precision grinding system Machine Sizes The Zeta ® grinding system is available in sizes ranging from the Mini/MicroSeries laboratory mills with grinding chamber volumes of 008 l to production machines with grinding chamber volumes of 400 l Full scaleup of the results achieved on the laboratory scale is possible Cleaning made easy The optimized cleaning concept with a wash cycle Grinding System Zeta®
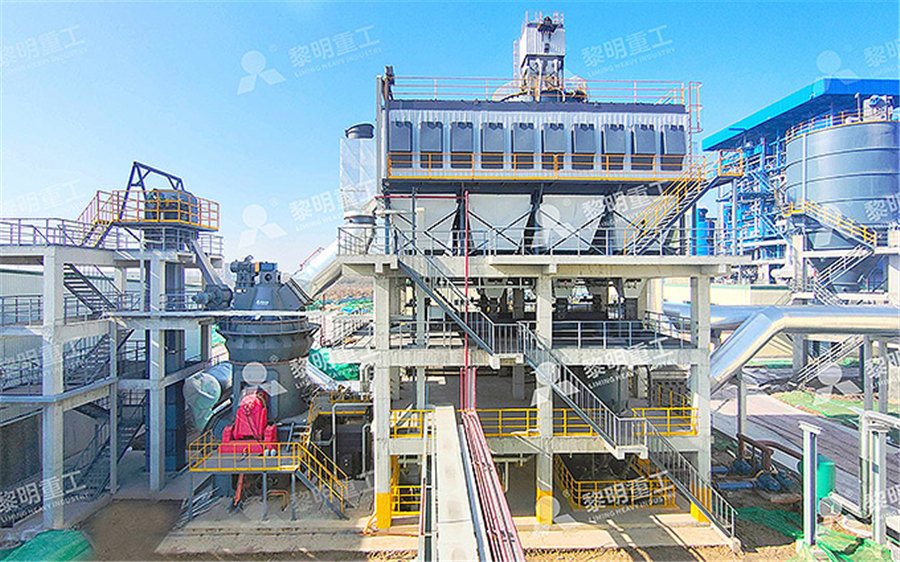
Grinding characteristics and batter quality of rice in different
2008年10月1日 Pasting behavior of raw and parboiled rice (IR64) batter prepared from different wet grinding systems (stone grinder, mixer grinder, and colloid mill) with average particle size ($620 mm) similar 2023年9月7日 The particle gradation affected both the matrix composition and microstructure In this study, six particle gradations of highalumina castables were prepared based on Andreasen's model (q = 022, 024, 026, 028, 030, and 032)Particle grading effect on properties of reactive MgO‐bonded Particle Size Distribution of Different Grinding Systems Free download as PDF File (pdf), Text File (txt) or read online for free Particle size distributions for different ores and grinding systems have been studied with measurements Particle Size Distribution of Different Grinding 2015年10月23日 In this chapter an introduction of widely applied energyefficient grinding technologies in cement grinding and description of the operating principles of the related equipments and comparisons over each other in EnergyEfficient Technologies in Cement Grinding
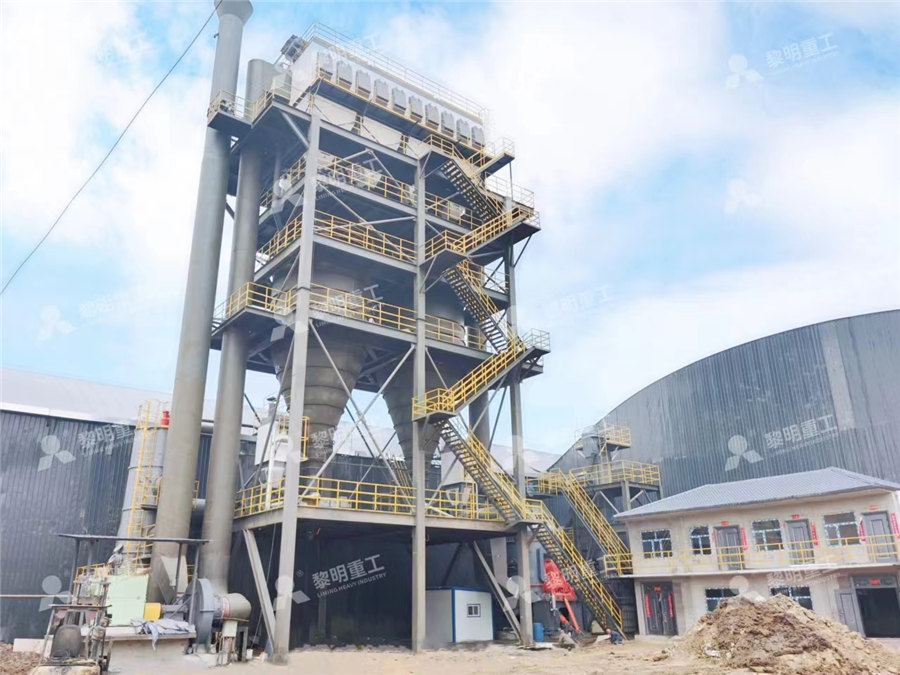
Grinding of rubber Hosokawa Alpine
MULTIPROCESSING SYSTEMS The perfect solution for flexible system concepts customers of diverse application areas benefit from Hosokawa Alpine’s solutions for cryogenic and ambient rubber grinding for maximum fineness This task places special demands on machines and Typical particle sizes after the ambient process (using a 630μm The Grinding System for Circulation and Multipass Operation NETZSCH Zeta® Grinding System Your Benefits ∙∙ Peg grinding system with the highest grinding intensity ∙ Finenesses into the nanometer range ∙ Very narrow particle size distribution ∙ Maximum economic efficiency ∙ Exact reproducibility ∙ Effective centrifugal separation Zeta Grinding System NETZSCH Energy2021年10月14日 1011 Pulp Feeding Tank In general, the hydrocyclone feed is conveyed by a pumping system coupled to the pulp discharge from a mill The pumping system consists of a tank that receives the pulp discharge from the grinding mill, a centrifugal pump driven by an electric motor, a transmission system of pulleys and trapezoidal belts and a piping systemHydrocyclone System Design SpringerLinkEssential for numerous industries, wet grinding plays a crucial role in achieving fine particle sizes and a homogenous mixture, crucial for quality production Understanding the Basics: What Is Wet Grinding? Wet grinding, a subset of the wet milling process, Wet Ball Milling Method and Technology allwingrinding

Air Swept Classifier Mill System How it Works, Benefits CMS
The CMS Air Swept Classifier Mill System combines dynamicimpact grinding and particle size classification in a single continuous process Independent drives for the Impact Rotor and Classifier Wheel allow the system operator to independently adjust their rotational speeds, thereby optimizing drag and tip speed control in producing the target particle size distributionWhether automated grading or sugar grinding conveying system needs, we provide comprehensive system design and solutions for your particle management Request a Quote (877) 2475625Automated Grading and Sugar Grinding Conveying System 2020年3月1日 [40] demonstrated that a particle size distribution with 66% of material below 55 µm (maximum retained in sieve 325 of 34%) could be achieved within a time frame of 12 min (Figure 5b)An investigation on optimum grinding system and conditions for CMS Air Classifier Mills combine impact grinding and air classification in a single continuous process Learn More The portable CMS Tabletop Lab System, ideal for batch testing and product development, has the particle size reduction and classifying capabilities of the CMS production level Air Swept Classifier MillsClassifier Milling Systems Milling System Manufacturer
.jpg)
(PDF) Cement Particle Size Modeling for Cement Combined Grinding System
2019年2月1日 Cement Particle Size Modeling for Cement Combined Grinding System Based on LSSVM February 2019; Journal of Physics Conference Series 1168(2):;2023年11月28日 Ballast is coarse aggregate with particle size normally ranging from 10 mm to 65 mm Upon repeated train loading, ballast deteriorates in the form of either continuous abrasion of sharp corners or size degradation, which Effects of Particle Size and Grading on the Breakage of 2022年1月1日 Siliconbonded silicon carbide (SBSC) porous ceramics had been prepared by mixing two different particle size of SiC powder (coarse and fine) as aggregates for silicon carbide porous ceramics (PDF) Effects of particle grading composition of SiC on properties MicroGrinding Systems, Inc offers a range of services at our Little Rock, Arkansas facility, including the following: Custom Grinding We can custom grind virtually any material to your specifications We offer quality control throughout the process to ensure the correct particle size Our grinding systems are capable of output of less than 1 MicroGrinding Systems, Inc MicroGrinding Systems, Inc
.jpg)
The Effect of Grinding Conditions on Disperse Particle Size of
2018年1月17日 Pigments are usually dispersed in the system with the form of particles [1,2,3]Generally, the pigment with particle size less than 1 um is called ultrafine pigment []Compared with ordinary pigments, ultrafine pigments possess excellent properties, such as greater surface area, higher color strength, more vivid colors and better gloss2022年4月1日 In an industrial scale, up and downstream operating units (eg, grinding, classification and dewatering) inevitably affect metallurgical responses of a flotation process Thus, the efficiency of either coarse or fine particle treatment systems is inherently coupled with the performance of these unitsTechnological assessments on recent developments in fine and The most efficient grinding system is a system that applies the minimum amount of energy to rupture the material without adding excess energy or heat Energy is required to reduce particle size, but it also generates heat which can change the sample state or degrade materialsPrinciples of Sample Preparation by Grinding or Comminution2002年12月1日 The results show that after grinding by the jet milling, the particle size distribution range becomes narrower, the values of d10, d50 and d90 decrease from 202, 443 and 995 μm to 179, 302 Improvement of grinding and classifying performance using a