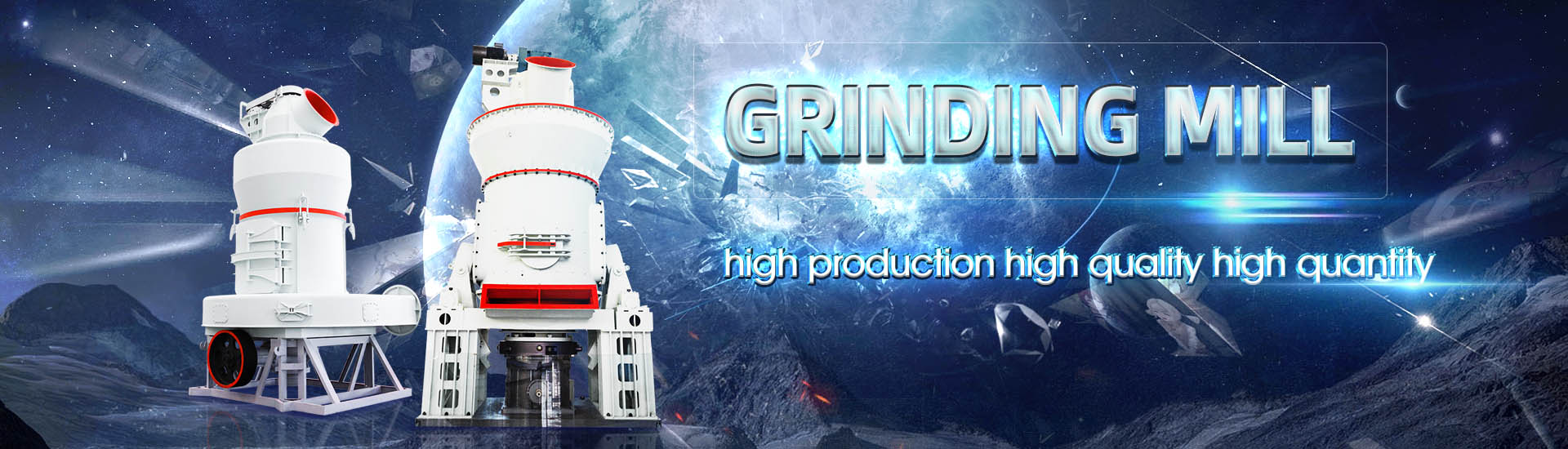
S mill ball material ratio
.jpg)
(PDF) Grinding Media in Ball MillsA Review
2023年4月23日 One of the most used tumbling mills is the ball mill This paper reviews different types of grinding media that have been developed and improved over the years and their properties Also2015年1月31日 As a thumb rule powder to be milled should be taken as 25% of total ball weight If the quantity of charge is very less then milling balls will start to collide with each other and no How can one select ball size in ball milling and how much material 2021年2月19日 The optimum process parameters setting concluded that balls to powder weight ratio are 20:1, the optimum ball mill working capacity is 2 L while the optimum speed of the ball Comparative Study on Improving the Ball Mill Process Parameters 2023年10月27日 The performance of grinding media in a ball mill is measured in terms of wear rate, which is a function of the media composition, hardness, phase structure, and A Review of the Grinding Media in Ball Mills for Mineral Processing
.jpg)
An innovative approach for determining the grinding media
2021年1月22日 The ball mill (Φ460mm × 600 mm) was used for wet grinding to conduct the optimization experiment of spacefilling factor and material ball ratio The grinding time 5 min Ball mills and grinding tools Cement ball mills are typically twochamber mills (Figure 2), where the first chamber has larger media with lifting liners installed, providing the coarse grinding BALL MILLS Ball mill optimisation Holzinger ConsultingIn a dry grinding process, the balls should be at least a factor of 3 larger than the largest particle of the sample material The jar filling situation should follow the 1/3 rule, to protect the grinding Three rules for the optimum ball mill setup RETSCH2024年6月3日 It is generally believed that higher ball milling speed, longer ball milling time, and larger balltomaterial ratio mean that more energy is delivered to the material particles toResearch progress on synthesis mechanism and performance
.jpg)
Effect of Milling Parameters on Size, Morphology, and Structure of
2022年9月20日 Changing the balltopowder ratio from 2:1 to 5:1 at highintensity vibration milling resulted in a change in particle morphology from granular to flake These results can be 2023年12月28日 10 Balltomaterial ratio The balltomaterial ratio is the ratio between the grinding body’s mass and the material’s mass If the balltomaterial ratio is too large, it will increase the wasted work loss due to impact friction Factors Affect The Output and Quality of Ball Mills And 2021年11月1日 The filling ratio, ratio of particle to ball and mineral weight were varied to control the mill load The initial ratio of grading ball was 30 mm: 40 mm: 50 mm: 70 mm = 30: 20: 30: 20 It should be noted that the diameter of instrumented grinding media is 70 mm Rotation speed of cement ball mill was set to 80%Assessing load in ball mill using instrumented grinding media2018年11月1日 As a typical MA, high energy ball milling process is a very complex dynamic process that possesses a lot of variables, such as the ball to powder ratio (BPR), milling speed, number and type of milling ball, the amount of process control agent, etc High energy ball milling is a mechanical alloying process that can be used to fabricate nanocrystalline powder and The ball to powder ratio (BPR) dependent morphology and microstructure
.jpg)
How do you calculate ball mill grinding media?
2023年6月16日 Choose the Appropriate Grinding Media Size: Select grinding media balls that are suitable for your mill and desired particle size Keep in mind factors such as ball diameter, balltomaterial ratio, and mill speed, as these can affect the grinding kinetics and efficiency2013年8月3日 In Grinding, selecting (calculate) the correct or optimum ball size that allows for the best and optimum/ideal or target grind size to be achieved by your ball mill is an important thing for a Mineral Processing Engineer AKA Metallurgist to do Often, the ball used in ball mills is oversize “just in case” Well, this safety factor can cost you much in recovery and/or mill liner Calculate and Select Ball Mill Ball Size for Optimum Grinding2022年1月1日 Planetary ball mill is extensively used for fine grinding, mechanical activation, planetary ball mill is suitable for generating mechanochemical reactions and developing a wide range of new technical materials from powder mixture [8] Poisson's ratio of ball and vial v b:Effects of balltopowder diameter ratio and powder particle 2021年7月12日 Ball milling process was conducted in a planetary ball milling machine (QM3SP04, Nanjing University Instrument Factory) equipped with four nylon ball mill tanks with an internal volume of 50 mL The stainless steel grinding balls with the diameter of 6 mm, 8 mm, and 10 mm were used during ball millingEffect of BalltoPowder Ratio on Morphology, Structure, and
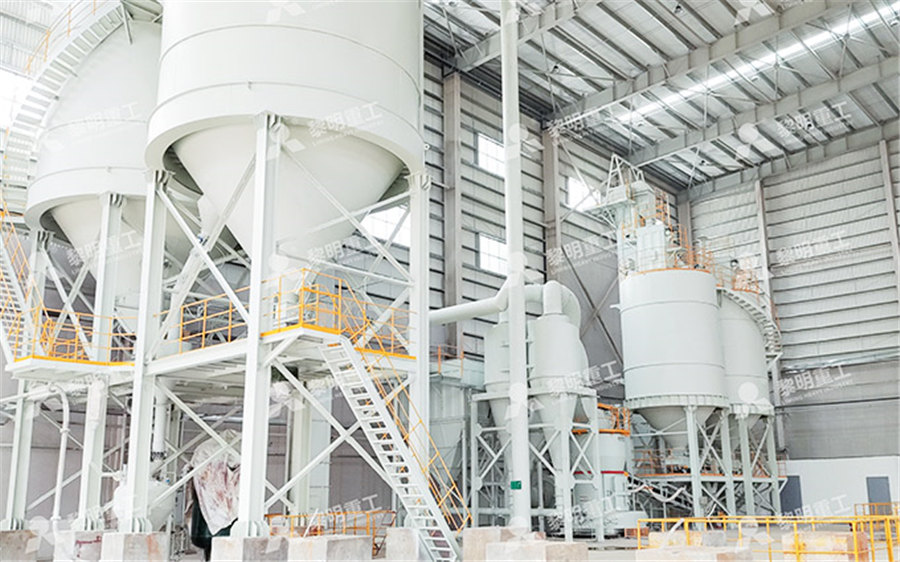
Ball Mill Success: A StepbyStep Guide to Choosing the Right
2024年8月8日 Choosing the right grinding media for ball milling involves a strategic assessment to align with operational goals, material characteristics, and cost constraints Here’s a stepbystep guide to facilitate this critical decisionmaking process: Step 1 Assessing Milling Requirements: The first step is a thorough analysis of the material to be 2022年12月1日 The ball material ratio affects the ore's speed in the grinding cylinder; consequently, selecting a suitable ball material ratio is a crucial condition for improving the grinding efficiency of the ball mill; a ball material ratio that is too large or too small will reduce the ball mill's capacity and grinding efficiency [21]Efficient preparation and characterization of graphene based on ball The history and necessity of mechanical alloying M Sherif ElEskandarany, in Mechanical Alloying (Second Edition), 2015 2515 Planetary ball mills The Planetary ball mills are the most popular mills used in MM, MA, and MD scientific researches for synthesizing almost all of the materials presented in Figure 11 In this type of mill, the milling media have considerably high Ball Mill an overview ScienceDirect Topics2023年10月27日 The ball mill is a rotating cylindrical vessel with grinding media inside, which is responsible for breaking the ore particles Grinding media play an important role in the comminution of mineral ores in these mills This work reviews the application of balls in mineral processing as a function of the materials used to manufacture them and the mass loss, as A Review of the Grinding Media in Ball Mills for Mineral
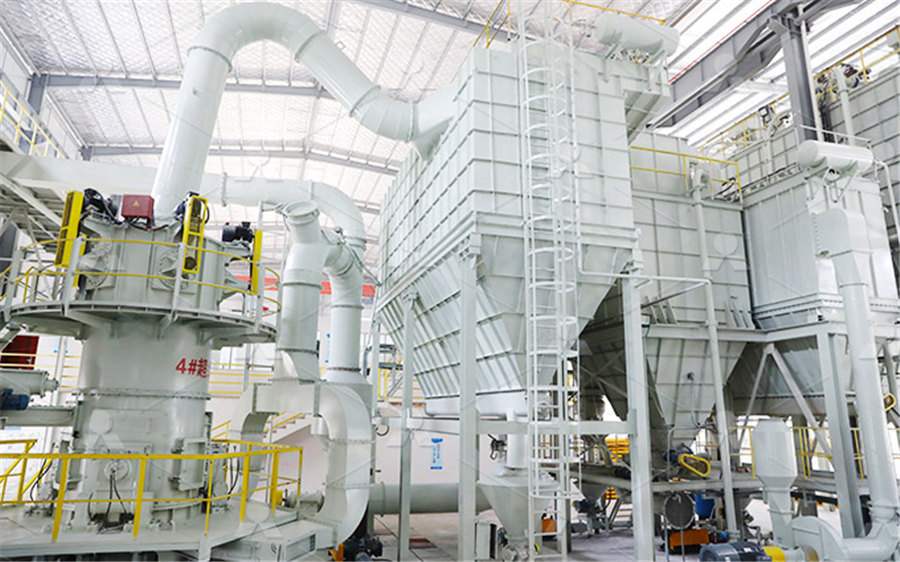
(PDF) Effects of Ball Size Distribution and Mill Speed and Their
2020年7月2日 A comprehensive investigation was conducted to delineate the effect of ball size distribution, mill speed, and their interactions on power draw, charge motion, and balls segregation in a Ball material Heavier balls allow grinding of harder materials, Larger balls are heavier and will be able to crush harder materials, but with less strikes per revolution, they will mill slower Particle size Ball milling has been used to grind materials to Ball Milling Guide InoxiaFor colloidal milling and most other applications, the ratio between the speed of the sun wheel and the speed of the grinding jar is 1: 2 This means that during one rotation of the sun wheel, the grinding jar rotates twice in the opposite direction This speed ratio is very common for Planetary Ball Mills in generalPlanetary Ball Mills RETSCH fine grinding of materials2012年6月1日 ratio “length to diameter” and this ratio mo st frequently varies from 05 to 35 Grinding Rate Constant of Solid Materials by a Ball Mill – Effect of Ball Diameter and Fe ed SizeGrinding in Ball Mills: Modeling and Process Control
.jpg)
The Ultimate Guide to Ball Mills Miningpedia
2019年8月14日 The gravel ball mill adopts porcelain material or granite as the lining board, which is widely used in the field of colored cement, white cement and ceramics 3 According to the discharging method of ball mill: In short, the number and ratio of ball mill steel balls is a relatively complicated technical problemThe fill rate, or the ratio of the volume of grinding media to the volume of the mill drum, influences the milling efficiency Optimal fill rates ensure proper balltoball and balltowall collisions, promoting efficient material breakdown and mixing 4 Ball Size and DensityExploring ball milling theory: A comprehensive guideThe big ball can break the material by impact, improve the impact ability and impact times of the mill, which accords with the functional characteristics of the grinding body; while the small ball can fill the gap between the big balls, increase the accumulation density of the grinding body, so as to control the material flow rate; in addition, the coarse particles in the gap can be squeezed How to choose the ball loading and loading ratio of ball mill?2015年2月21日 For example your ball mill is in closed circuit with a set of cyclones The grinding mill receives crushed ore feed The pulp densities around your cyclone are sampled and known over an 8hour shift, allowing to calculate corresponding to circulating load ratios and circulating load tonnage on tons/day or tons/hourCirculating Load Calculation Formula 911Metallurgist
.jpg)
The working principle of ball mill Meetyou Carbide
2019年5月22日 The larger the ball to material ratio, the higher the grinding efficiency But too high a ball ratio is unhelpful Because the amount of charge is reduced when the filling factor is constant, it is bound to reduce the productivity of the set, and sometimes reduce the alloy properties (Figure 82) The ball ratio is usually selected from 2:1 to • Speed ratio (speed sun wheel : grinding jar) Laarmann Group BV Op het Schoor 6 6041 AV The Netherlands info@laarmann laarmann webshoplaarmann +31 6 23 40 00 33 LM PBM PLANETARY BALL MILL Counter weight with 1 jar can be expanded for 14 positions PBM Planetary ball mill closed 1 Movement planetary millPLANETARY BALL MILL Laarmann2023年3月29日 Milling machine/grinding ball/source material/environmental properties, milling media and time, and balltomaterial ratio need to be considered along with cost and safety for mass production Continuous Recent Advances in BallMillingBased Silicon Anodes Ball Mill Ball Mills are mainly used in metallurgy, chemical industry, electric power, cement and other industrial and mining business to make all kinds of ores and other grindable materials by virtue of such characteristics as strong adaptability to raw materials, excellence in continuous production, high crushing ratio and easy to adjust the fineness of the finished productBall Mill
.jpg)
Research progress on synthesis mechanism and performance
2024年6月3日 The pretreatment of ball milled biochariron based materials includes: (1) impregnating iron salt solution; and (2) direct mixing The former initially immerses the original biomass in an iron 2024年2月19日 2 The grinding force of the steel ball During the ball mill’s operation, the steel ball’s surface area is mainly relied on to make the material contact with the steel ball’s surface to improve the ball mill’s grinding efficiency In particular, the fine grinding chamber that relies on the grinding action to stop grinding is criticalBall Mill Steel Balls: Quality And Gradation JXSC Mineral2023年4月30日 According to the ratio of cylinder length (L) to diameter (D), the ball mill can be divided into short cylinder ball mill, L/D ≤ 1; long barrel ball mill, L/D ≥ 1–15 or even 2–3; and tube mill, L/D ≥ 3–5 According to the cylinder shape of the ball mill, it can be divided into cylindrical ball mill and cone ball millBall Mill SpringerLinkThe ball impact energy on grain is proportional to the ball diameter to the third power: 3 E K 1 d b (3) The coefficient of proportionality K 1 directly depends on the mill diameter, ball mill loading, milling rate and the type of grinding (wet/dry) None of the characteristics of the material being ground have any influence on K 1THE OPTIMAL BALL DIAMETER IN A MILL 911 Metallurgist
.jpg)
What is the Ball Ratio for Ball Milling? (3035% Optimal Filling
This ratio is crucial for maintaining the efficiency and productivity of the ball mill Explanation of the Ball Ratio 1 Optimal Filling Level The ball ratio in ball milling is primarily about the proportion of the mill's volume that should be occupied by the milling balls This is typically expressed as a percentage For efficient operation 2022年1月1日 The effects of the balltopowder diameter ratio (BPDR) and the shape of the powder particles on EDEM simulation results and time in the planetary ball mill was investigated BPDR was varied from 1 to 40/3 by changing the powder particle diameter from 8 to 06 mm The size and shape of the powder particles do not give a significant change in both the ball motion Effects of balltopowder diameter ratio and powder particle The Planetary Ball Mill PM 100 is a powerful benchtop model with a single grinding station and an easytouse Planetary Ball Mill PM 100 Typical Sample Materials RETSCH planetary ball mills are perfectly suitable for size The Planetary Ball Mill PM 100 RETSCH highest fineness2023年10月23日 The Ratio of Grinding Ball Mass to Material Mass:Ideally, the mass ratio of grinding balls to material should be above 5:1 The volume filled with grinding balls and material should not exceed 80% of the ball mill's volume, with a How to Determine the Ratio of Grinding Balls in a Ball Mill (Material
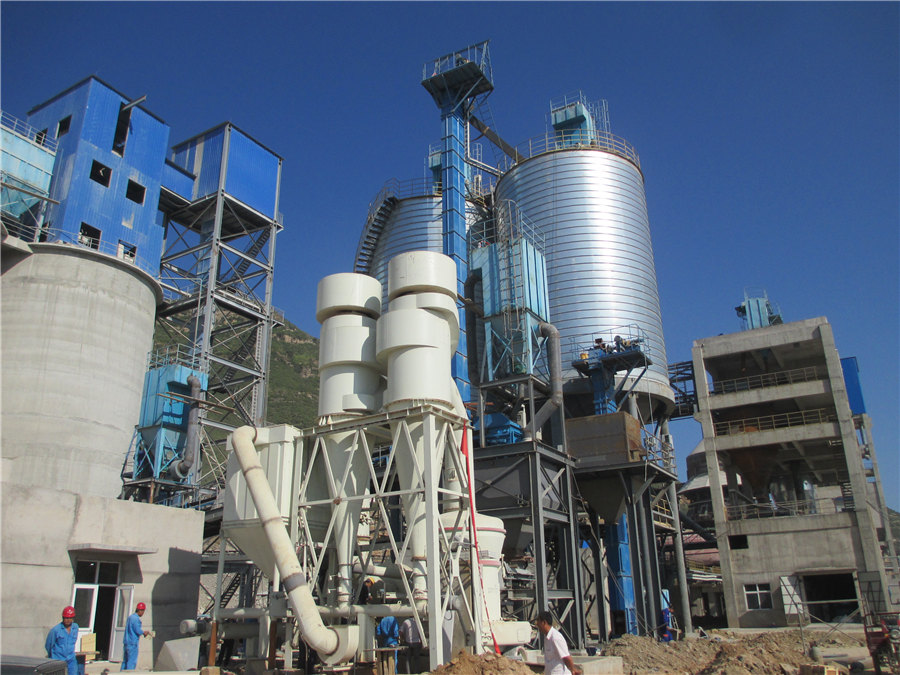
Investigating the Influence of Medium Size and Ratio
2024年8月27日 Grinding media plays a crucial role in the energy transfer during the mineral particle size reduction process []The energy carried by these media, along with its distribution and conversion, significantly impacts the mill’s Stone loading amount = 314X the square radius of the ball mill X the specific gravity of the ball X the length of the ball mill X25%*1000 Regarding the gradation of the high alumina ceramic ball of the ball mill: Due to the different grinding aids added to How to choose the size, filling amount and ratio of alumina The material and thickness of the liners, as well as the mill shell's diameter and length, are essential specifications that impact the mill's durability and grinding efficiency 6 Fill Ratio:Understanding ball mill specifications for optimal performanceThe ball and material – mass ratio is generally kept at 2:1 d Ball mill is crucial to numerous industries as an equipment for producing extremely crushed materials, eg cement, refractory materials, fertilizers, glass ceramic, ore dressing of ferrous as well as nonferrous metals, Ballmilling – Nanoscience and Nanotechnology I INFLIBNET
.jpg)
Three rules for the optimum ball mill setup RETSCH
OPTIMUM BALL MILL SETUP The success of a ball milling application depends on the correct selection of accessories and process parameters related to the reaction achieved Here, the ball to material weight ratio is often greater than 1, with the consequent increase in wear of the grinding tools Wet grinding: 2021年2月19日 In these results, the main effects plot for S/N ratio indicates that the balls to powder weight ratio process factor, having (20:1) has the value of SN ratio as (9272) indicating that this process factor has the largest effect on the signaltonoise ratio Ball mill working capacity with (2 Liters) has the value of SN ratio as (12915) and Comparative Study on Improving the Ball Mill Process Parameters The grinding jars are arranged eccentrically on the sun wheel of the planetary ball mill The direction of movement of the sun wheel is opposite to that of the grinding jars in the ratio 1:2 (or 1:25 or 1:3) The grinding balls in the grinding jars are subjected to superimposed rotational movements, the socalled Coriolis forcesPlanetary Ball Mill PM 400 RETSCH powerful and quick grinding