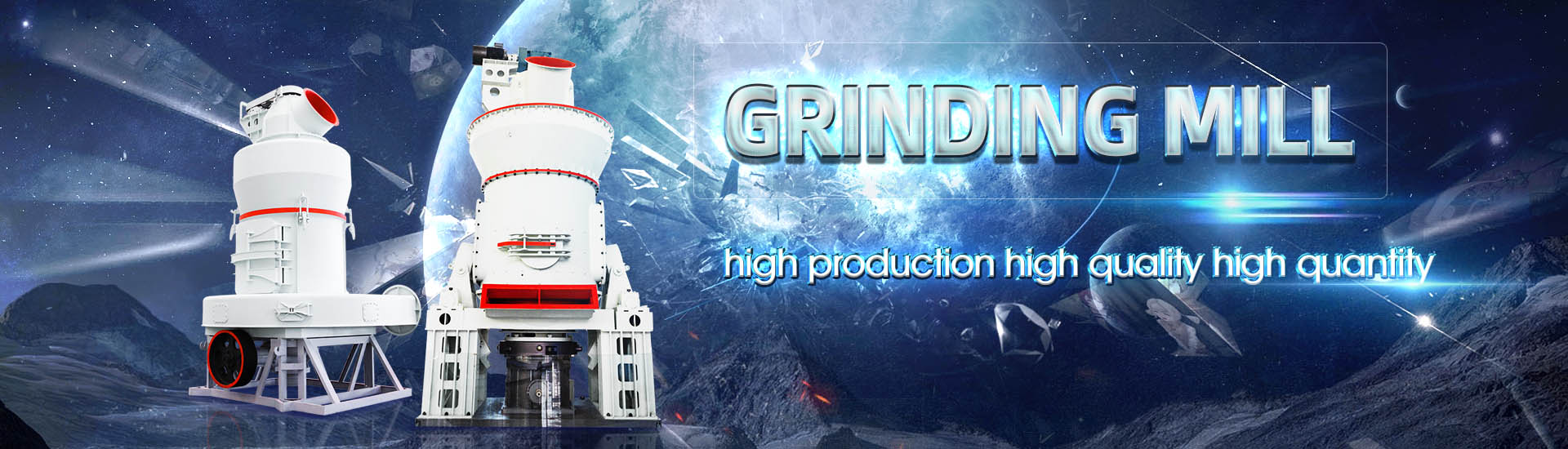
Consumption of ball mill lining for processing one ton of calcite ore
.jpg)
Consumption of steel grinding media in mills – A review
2013年8月1日 The consumption of grinding media has been studied extensively in the mineral process industries, where steel balls and rods are mostly used to reduce rock fragments and 2023年10月27日 Grinding media play an important role in the comminution of mineral ores in these mills This work reviews the application of balls in mineral processing as a function of the A Review of the Grinding Media in Ball Mills for Mineral Processing 2004年11月1日 When significant ball breakage is to be expected—as in semiautogenous grinding (SAG) applications—an expanded, conceptual model, based on pilot Drop Ball Methodologies for the evaluation of grinding media consumption 2023年10月27日 Grinding media play an important role in the comminution of mineral ores in these mills This work reviews the application of balls in mineral processing as a function of the A Review of the Grinding Media in Ball Mills for Mineral Processing
R)8OC`6F[ZIB.jpg)
Three factors that determine the wear life and performance of mill
Ball mill Most ball mills, even in primary applications, have a finer ore feed size; this requires some impact but not enough to increase the media consumption or even break the liners 2020年5月1日 Taking a Φ549 × 883 m ball mill as the research object, the reason for the low processing capacity of the ball mill was explored via process mineralogy, physicochemical Enhancing the capacity of largescale ball mill through process Steel balls and rods are frequently used in tumbling mills as grinding media to assist in ore breakage Fresh media are regularly fed into these mills to replace the media that are Energy Curve Enhancement Blog 7: Including grinding media 2012年12月1日 With compromise optimized values of 29% ball load volume and 75% slurry solids, the response surface models yielded specific energy consumption of 1054 kW h/t and (PDF) Optimization of inmill ball loading and slurry solids
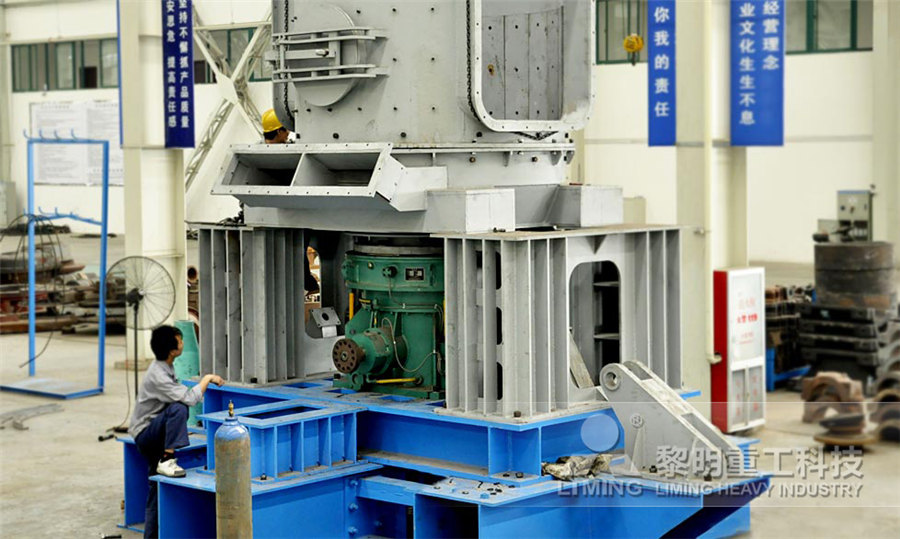
Ball Mill Design/Power Calculation 911Metallurgist
2015年6月19日 Use this online calculators for Motor Sizing and Mill sizing as well as mill capacity determinators In extracting from Nordberg Process Machinery Reference Manual I The power consumption of the grinding mill is a critical parameter in the economics of the chromite beneficiation process The ball mill consumes about 25–30% of the total energy in the beneficiation plant, and hence any improvement will improve the overall economics of the plant The power consumption of the ball mill was monitored forPerformance optimization of an industrial ball mill for chromite processing2023年10月27日 The ball mill is a rotating cylindrical vessel with grinding media inside, which is responsible for breaking the ore particles Grinding media play an important role in the comminution of mineral ores in these mills This work reviews the application of balls in mineral processing as a function of the materials used to manufacture them and the mass loss, as A Review of the Grinding Media in Ball Mills for Mineral Processing Request PDF On Nov 24, 2022, Ivan Minin and others published Effect of Drum Ball Mill Lining Shape on Specific Energy Consumption Find, read and cite all the research you need on ResearchGateEffect of Drum Ball Mill Lining Shape on Specific Energy Consumption
.jpg)
Control of ball mill operation depending on ball load and ore
water consumption required for the mill, u2– ore arrival speed, u3 – percentage of the critical speed of the mill, u4 – pulp water consumption and u5– mill incoming pulp consumption Output parameters can be controlled by these variable values[3,5]: x1 the mass fraction of the product whose particle size2020年7月2日 The relevance Ball mills are widely used in industry for grinding bulk materials, as well as in the last stages of ore crushing, where the required optimal particle sizes are achieved for enrichment(PDF) Effects of Ball Size Distribution and Mill Speed and Their 2023年12月12日 Ball mills are used for the second stage of ore grinding in mining operations by proportioning ore piles Controlling the operating conditions of ball mills is one of the key factors for optimal (PDF) Control of ball mill operation depending on ball load and ore 2024年4月26日 Iron ore processing is a crucial step in the production of steel, one of the most essential materials in modern society Iron ore, a naturally occurring mineral composed primarily of iron oxides, is mined and processed to extract iron for various industrial applicationsIron Ore Processing: From Extraction to Manufacturing
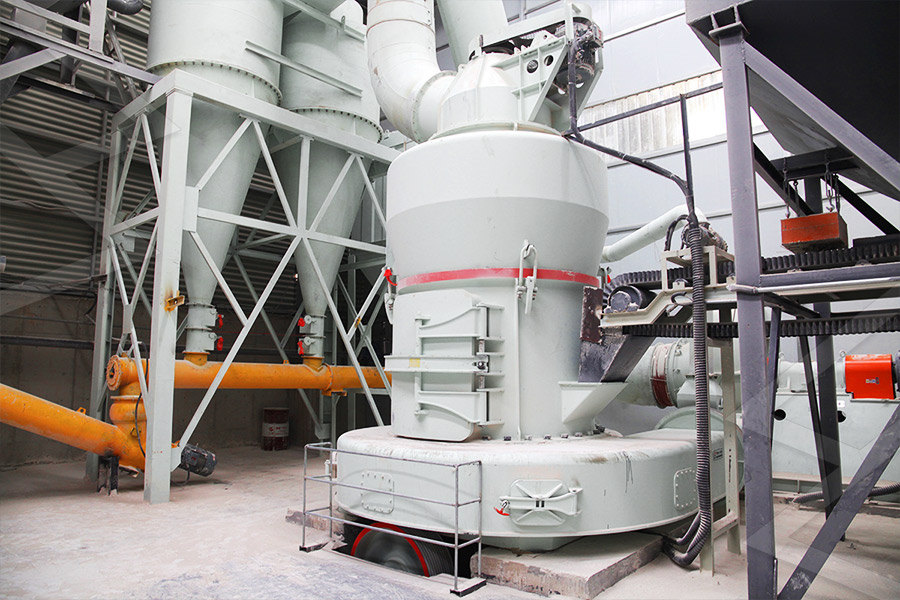
(PDF) Effect of wet ball milling on copper ore flotation by fractal
2023年3月15日 One of the important parameters in mineral processing is particles morphology, which is a function of the comminution mechanism Particles morphology has considerable impacts in flotation process2022年1月12日 During the period 20142016, several industrial tests were conducted at Ukrainian mining and processing plants Omitting all intermediate calculations, we observe the following: For balls with a diameter of 2550mm, the cost of grinding one ton of ore varies from 0317 UE to 0347 UE The average cost of grinding one ton of ore is 0330 UEMINING AND PROCESSING PLANTS SELECT STEEL GRINDING BALLS2012年12月1日 Optimization of inmill ball loading and slurry solids concentration in grinding of UG2 ores: A statistical experimental design approach(PDF) Optimization of inmill ball loading and slurry solids heavy minerals preservation in the process of their release from ore in ball mills [6] We have developed a new design of a ball mill with spiral groove for timely removing and preservation of the commercial component, which is shown in Figure 1 [7] Fig1 Ball mill with continuous unloading of the commercial component: 1 drum; 2 riffles; 3 Development of a new lining ball mill model for commercial
.jpg)
How Ball Mill Ore Feed Size Affects Tonnage Capacity
2017年7月26日 We will consider an ore with a ball mill work index varying between 16 and 13, feeding into a single stage ball mill operation with one million kilowatts per day consumed power For the particular mill configuration, a performance graph, Fig (21), has been constructed according to Bond’s methods2021年3月23日 New ball mill drive system with the prototype energysaving SMH motor [37] Energy Efficiency Analysis of Copper Ore Ball Mill Drive Systems2002年11月1日 Unfortunately, the energy efficiency is extremely low in mining operations For instance, the energy efficiency is about 10% in percussive rock drilling (Carrol 1985), 35% in rock crushing The energy efficiency of ball milling in comminution2013年5月1日 In both cases, the specific comminution energy increased with the size reduction ratio Similar relationships were observed for other types of grinders used for granular materials, such as ball (PDF) Effect of ball mill grinding parameters of hydrated lime
.jpg)
The effect of processing parameters on energy consumption of ball mill
2013年9月1日 The effect of processing parameters on energy consumption of ball mill refiner for chocolatepdf Available via license: CC BY 40 Content may be subject to copyrightAnalysis of the efficiency of the grinding process in closed circuit ball mills Valery I Telichenko1, Rashid R Sharapov1*, Svetlana YLozovaya2 and Vladimir ISkel1 1Moscow State University of Civil Engineering, Moscow, Russia 2Belgorod State Technological University named after VG Shukhov, Belgorod, Russia Abstract Ball mills for fine grinding cement clinker and additives areAnalysis of the efficiency of the process in closed circuit ball mills2023年2月15日 What should we do to solve those problems? 1 First of all, it is necessary to do analyses including changes of nature of the ore, whether the amount of ore, water, sand and overflow size are normal Then do the measures to deal with them 2 Reduce the amount of feed to the mill until the working state of the ball mill returns to normal; 3 Appropriately reduce the 17 Signs of Problems with Ball Mills: Quickly Remove Hidden Troubles2013年8月1日 Apart from these cost factors, one of the major unsolved problems in the optimal design of ball mills concerns the equilibrium media size distribution in the mill, which is determined by the rate at which makeup media is added to the mill, as well as the rate at which these grinding media are consumed (Austin and Klimpel, 1985)Reliable prediction of grinding media Consumption of steel grinding media in mills – A review
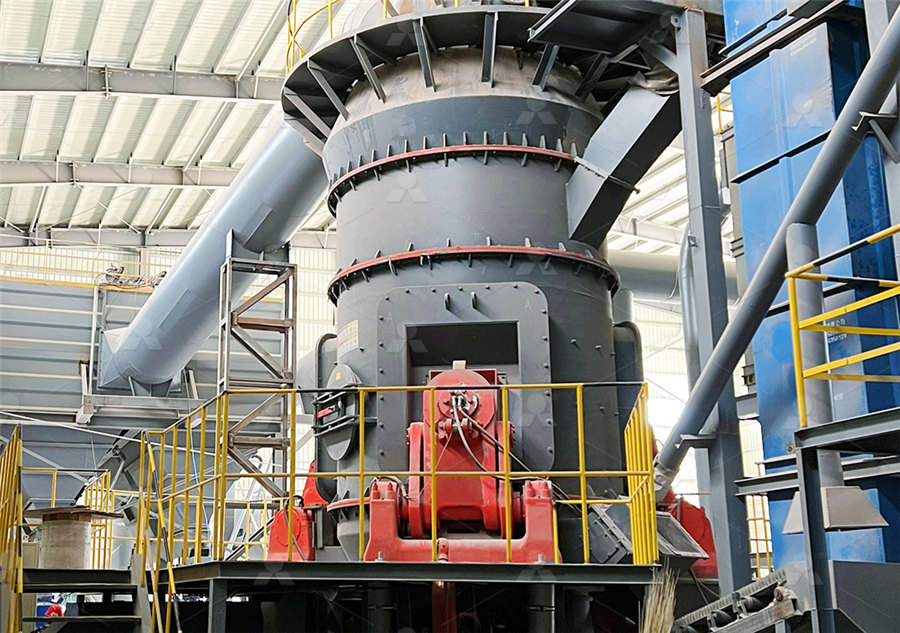
Energy Efficiency Analysis of Copper Ore Ball Mill Drive Systems
3 Analysis of Variant Ball Mill Drive Systems The basic element of a ball mill is the drum, in which the milling process takes place (Figure1) The length of the drum in the analyzed mill (without the lining) is 36 m, and the internal diameter is 34 m The mass of the drum without the grinding media is 84 Mg2016年1月1日 PDF The aim of this study was to determine the effect of main milling variables, ie agitator shaft speed (50%, 75%, and 100%, which is 25 rpm, 375 Find, read and cite all the research (PDF) Optimization of the ball mill processing Assessment of effect of lining material on energy efficiency of starting up ball mills Khakim Muratov1*, Oybek Ishnazarov1, Abdusaid Isakov1, 2, and Ikrom Nuritov2 1Institute of Energy Problems of the Academy of Sciences of the Republic of Uzbekistan, Tashkent, Uzbekistan 2“Tashkent Institute of Irrigation and Agricultural Mechanization Engineers” National ResearchAssessment of effect of lining material on energy efficiency of 2020年7月24日 The energy consumption of grinding is the subject of many studies, especially in the case of ball mills for grinding clinkers [8, 9], fuels [10], iron ore [11], hematite ore [12], sulfide ore [13 Determination of granulometrical composition of
.jpg)
Grinding Media Wear Rate Calculation in Ball Mill
2017年4月29日 In the previous discussion the fact was established that the work done by a ball when it strikes at the end of its parabolic path is proportional to its weight and velocity; then, since the velocity may be considered as constant for all the balls in the mill, the work done by a ball is proportional to its weight Since the amount of ore crushed varies as the work done upon it, it Assessment of effect of lining material on energy efficiency of starting up ball mills Khakim Muratov1*, Oybek Ishnazarov1, Abdusaid Isakov1, 2, and Ikrom Nuritov2 1Institute of Energy Problems of the Academy of Sciences of the Republic of Uzbekistan, Tashkent, Uzbekistan 2“Tashkent Institute of Irrigation and Agricultural Mechanization Engineers” National ResearchAssessment of effect of lining material on energy efficiency of 2021年11月1日 A mineralogy, rheology, and energy consumptionbased experimental characterization of chalcopyrite ball mill grinding processes, in both batch and continuous flow processing modes, is carried out Experimental characterization of chalcopyrite ball mill grinding The energy consumption in the ball mill was found to be 65 kWh/t of ore with a targeted product size below 1 mm The BWI of the ores varied from 58 to 78 kWh/t to reduce the particle size below 100 μ m, but in real time, the energy consumption is very high compared with the reported value of 65 kWh/tPerformance optimization of an industrial ball mill for chromite processing
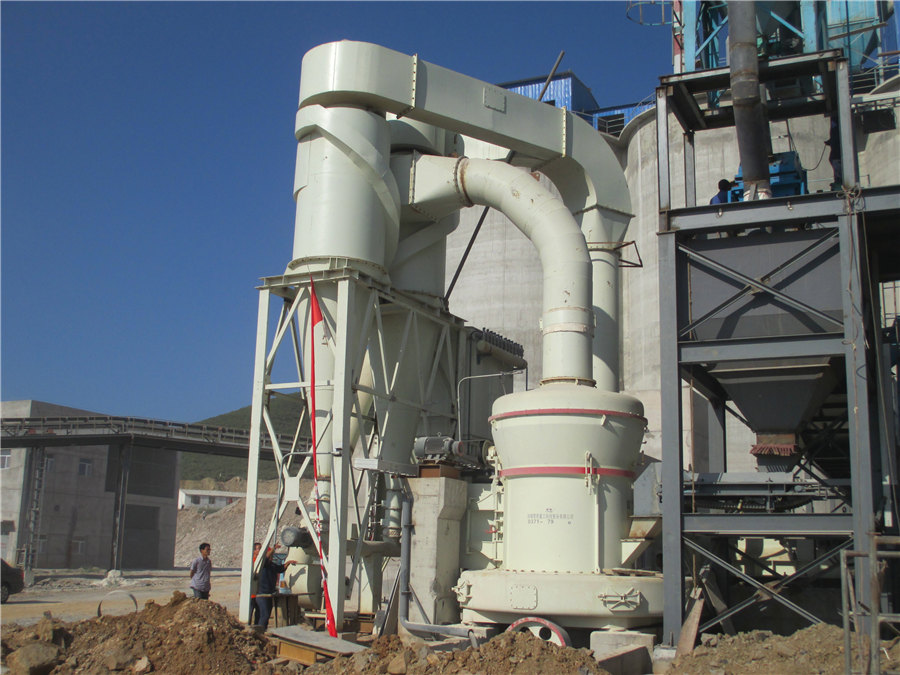
Mill Lining Systems FluidHandling Trelleborg
Trelleborg has been providing mill lining systems since 1920 The focus is on working with our customers to provide incremental improvement to enhance mill availability, increasing efficiency and reducing energy consumption Full lining kits are designed and supplied including Lifter bars, shell plates, pulp lifters, fasteners and discharge grates2016年3月21日 Concentration and Recovery Formulas These are used to compute the production of concentrate in a mill or in a particular circuit The formulas are based on assays of samples, and the results of the calculations are generally accurate— as accurate as the sampling, assaying, and crude ore (or other) tonnage on which they mon Basic Formulas for Mineral Processing Calculations2013年8月3日 In Grinding, selecting (calculate) the correct or optimum ball size that allows for the best and optimum/ideal or target grind size to be achieved by your ball mill is an important thing for a Mineral Processing Engineer AKA Metallurgist to do Often, the ball used in ball mills is oversize “just in case” Well, this safety factor can cost you much in recovery and/or mill liner Calculate and Select Ball Mill Ball Size for Optimum GrindingTable 1 Chemical composition of typical grinding media (% wt) Adapted from [24] 211 Cast Iron Cast iron can be grey cast iron or white cast iron, but white cast irons are commonly used in Grinding Media in Ball MillsA Review ResearchGate
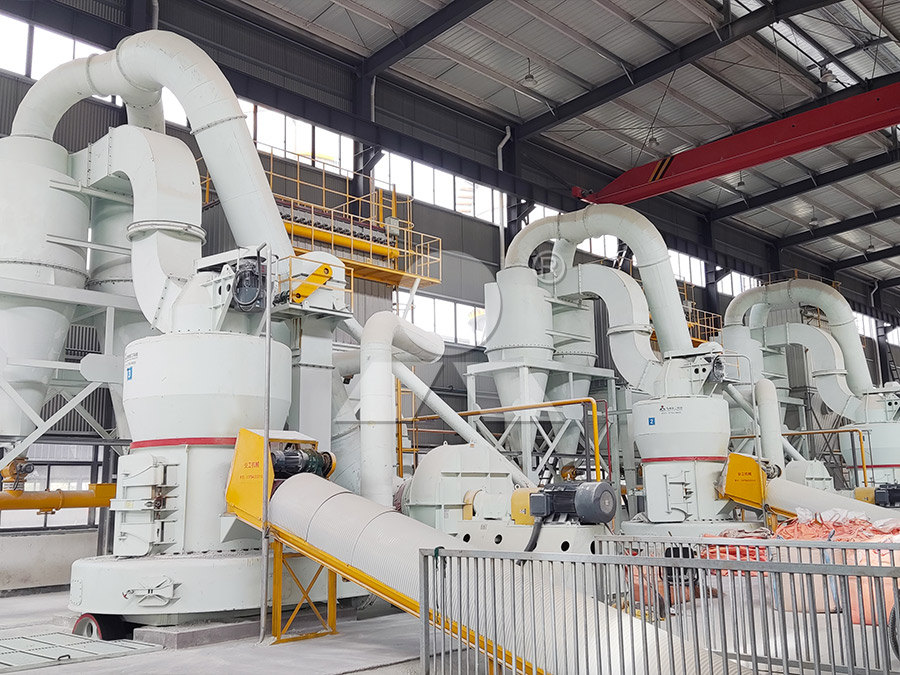
Top 10 tips to improve the grinding efficiency of ball
2020年3月21日 Ball mill's low grinding efficiency, low processing capacity, high production energy consumption, unstable product fineness, etc are problems that many customers will encounter How to effectively improve the grinding The mill liner is installed inside the ball mill barrel to protect the inner wall of the barrel from the impact of materials and grinding media (steel balls, steel sylpebs, steel rods, etc) to avoid premature damage to the barrelAs an important part Mill Linings for Sale, Types of Ball Mill LinersA Review of the Grinding Media in Ball Mills for Mineral Processing, 2023 The ball mill is a rotating cylindrical vessel with grinding media inside, which is responsible for breaking the ore particles Grinding media play an important role in the comminution of mineral ores in these mills(PDF) Methodologies for the evaluation of grinding media consumption 2013年7月15日 The sample was received crushed appropriately for the ball mill test Ball Mill Grindability Test was conducted by standard practice using 100mesh (150 pm) closing screens The ball mill work index is shown below BM Wi (kWhr/st) = 1797 ; Bond Work Index FormulaEquation 911Metallurgist
.jpg)
Optimization of continuous ball mills used for finishgrinding of
2004年12月1日 During the last decade, semifinishgrinding plants have been used more and more for the energy efficient grinding of highquality cement In 1999, it was found that by decreasing the ball charge 2016年4月25日 the mill speed, ball load, ball diameter and particle load, from the energy consumption point of view[1] As for the grinding operation, it is a continuation of crushing operation and it is the lastDesign and Fabrication of Mini Ball Mill (edited) ResearchGate2022年1月1日 The effect of ball load composition, by varying the grinding media size distribution (eg alternatively by mixing four groups of 195, 38 mm; 195, 50 mm; 38, 50 mm and 195, 38, 50 mm), on the Effect of grinding media on the milling efficiency of a ball mill2014年10月20日 Santos Júnior et al (2011) also reported lower consumption of grinding bodies in the Vertical Mill 69 g/kWh versus 80 g/kWh observed in the ball mill The specific energy consumption measured Regrind of metallic ores with vertical mills: An overview of the
.jpg)
Hardinge Conical Mill – Grinding Efficiency Compared
2017年3月8日 For the particular installation mentioned the consumption of balls and lining is given as less than 1 lb per ton of ore ground The material fed to the ballmill, some of which exceeds 2 in in diameter, is taken directly from a rockcrusher