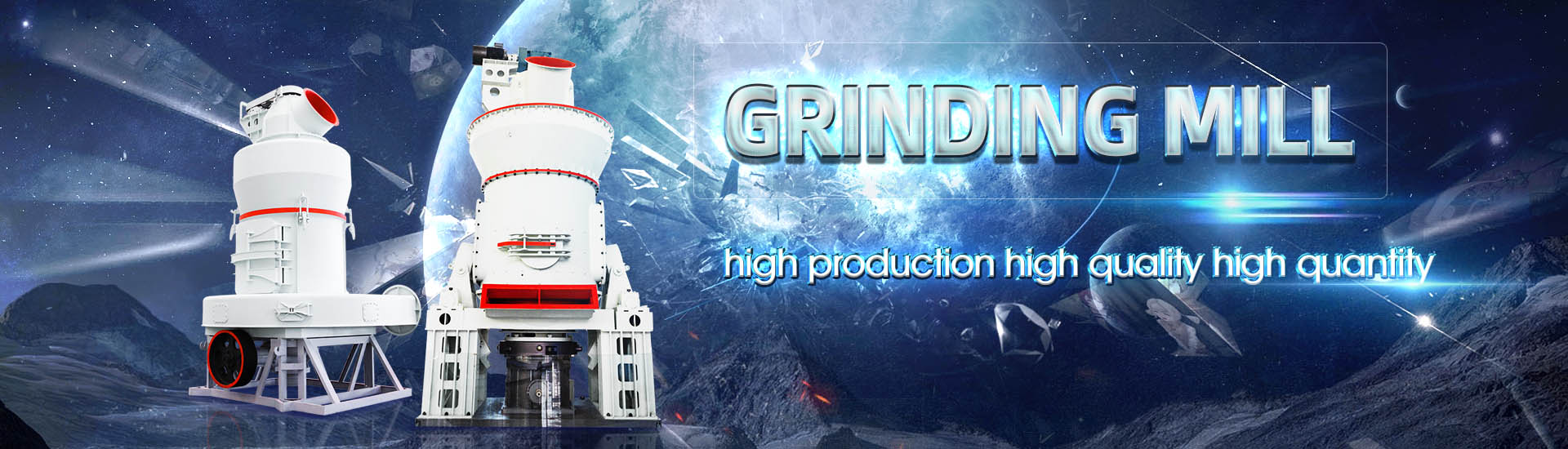
Coal ash grinding equipment process flow
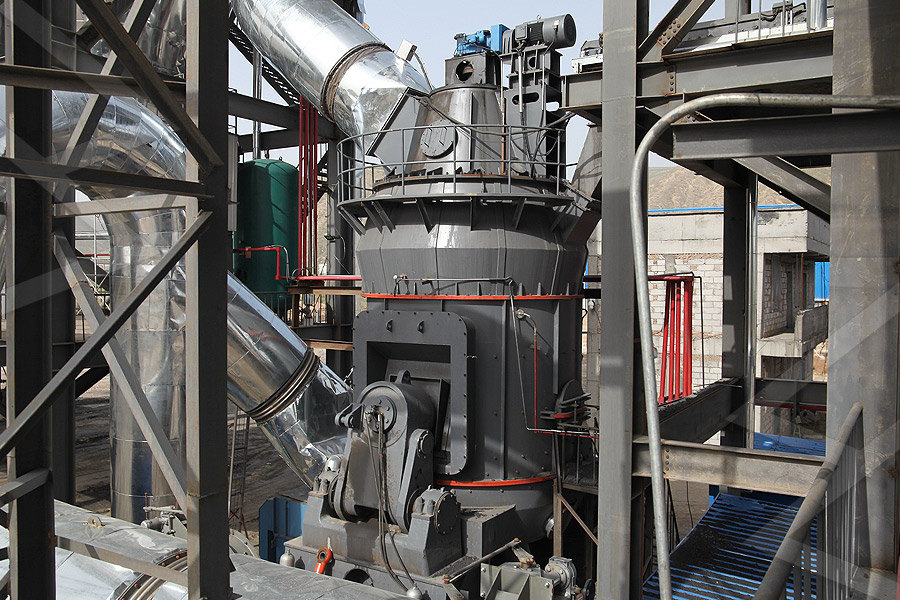
Flowsheet of a modern coal preparation plant incorporating four
typical coal processing plant flowsheet integrates three or four cleaning circuits to separately clean coarse (plus 12 mm), intermediate (12 × 1 mm) and2019年8月23日 Coal processing description from its geology mineral property to how to extract coal, and how to increase coal heating, related processing plant flow chart and layout designCoal Processing Equipment, Process Flow, CasesTwo conceptual flow sheets and major equipment lists are also presented for handling ash or granulated slag and other solid wastes produced by nine leading coal conversion processes Conceptual flow sheets development for coal conversion plant 2023年1月1日 This chapter discusses research that has contributed to improved understanding of pulverized fuel (PF) technology The processes studied are the grinding of PF in power Advances in pulverised fuel technology: understanding coal
.jpg)
A review of stateoftheart processing operations in coal
2015年7月1日 This approach typically includes the following steps: (1) characterization of feed coal properties to establish particle distributions for size, density, and floatability, (2) simulation Complex investigations of raw coal include the study of an inmine sample, a coal sample after grinding and sludge formation in the washing process Typically, design institutes use the data Design of coal preparation plants: problems and solutionsCoal grinding machine Coal grinding process flow Coal grinding is an essential process in the coal preparation process, energy industry, and cement manufacturing Coal grinding machines are used to achieve particle size reduction and surface area increase, which is crucial for burning efficiency and overall process effectiveness Here's an Coal grinding machine Coal grinding process flow NEWS2014年1月1日 Two mill systems are employed for most coal grinding applications in the cement industry These are, on the one hand, vertical roller mills (VRM) that have achieved a share of almost 90% and, on (PDF) MPS mills for coal grinding ResearchGate
.jpg)
Flowsheet of a modern coal preparation plant incorporating four
Download scientific diagram Flowsheet of a modern coal preparation plant incorporating four parallel circuits from publication: Genetic algorithms — A novel technique to optimize coal Coal processing or coal beneficiation uses physical (mechanical) and/or chemical methods to remove rocks, dirt, ash, sulphur and other contaminants and unwanted materials to produce highquality coal for energy in both local and export markets Multotec manufactures a complete range of equipment for coal processing plants, from the Run of Mine (ROM) stockpile to the tailings Coal Processing Multotec• Only gives value of total flow rate supplied by Hopper By Means of Correlative Flow Rate Measurement Device in Coal Conveying Line: • Direct determining of relative flow rate value in coal conveying line • Gives relative values [mA] • Requires second level weighing system for turning relative values [mA] into absolute values [kg/s]Pulverized Coal Injection Paul WurthSummary:The fly ash processing system is composed of dryer, elevator, silo, grinding mill, fan, powder concentrator, dust collector, pipeline device, etc How to Process Fly Ash and What Is It Used for Fly ash is the fine ash collected from the flue gas after coal combustion Fly ash is the main solid waste discharged from coalfired power plantsHow to Process Fly Ash and What Is It Used for sbmchina

(a) Fly ash ultrafine grinding equipment flow diagram, (b)
Download scientific diagram (a) Fly ash ultrafine grinding equipment flow diagram, (b) Illustration of the preparation of coreshell structured LWA from publication: Highly effective chromium 41 Commercially available coal flow measurement and control equipment 32 411 GreenBank’s PFMaster 33 412 Mistras Products Systems’ Coal Flow Monitoring Systems (CFM) 33 413 PROMECON’s MECONTROL Coal (in USA licensed to Air Monitor Power as PF FLO III) 34 414 MIC’s Coal Flow Analyser 35Optimising fuel flow in pulverised coal and biomassfired boilers2023年1月9日 Process flow The fly ash grinding process can be divided into open circuit and closed circuit systems Open circuit grinding process The system takes the ash from the coarse ash silo, and after it is measured by the spiral electronic scale, the coarse ash is continuously and stably fed into the grinding mill by the elevatorHow to Process Fly Ash and What Is It Used for2022年2月24日 Improving the efficiency of the coal grinding process in ball drum mills at thermal power plants February 2022 EasternEuropean Journal of Enterprise Technologies 1(1 (115)):93105Improving the efficiency of the coal grinding process in ball drum
.jpg)
Coal Grinding and Firing Systems – HAZOP Analysis
Equipment lists Process flow sheets and Process and Instrument Diagrams List of Process control loops and Process and Safety Interlocks List of Instrumentation and Alarms and Process variables with all limits Operating procedures and work instructions for various modes of operation Maintenance procedures and work instructions2021年5月11日 During the combustion of coals in thermal power plants, a residual mass generates, the quantity of generation of this residue depends upon the ash content of the coal, and this residue is called coal ash (Das et al 2019) or coal combustion residuals (CCRs)A schematic diagram has been provided in Fig 192 detailing the generation of these coal ashesCharacterization and Utilization of Coal Ash for Synthesis2018年9月28日 However, during the process of blasting, Ttype fracture generates at the point of blast and it propagates through the weak structures like cleats present in the mineralcoal barrier by breaking Generation of low ash fine clean coal powder by autogenous grinding process2023年4月20日 It has been confirmed that the surface morphology of particles has an important effect on flotation [21], [22], [23], and the surface pores of particles can prolong the adhesion time of bubbles on the particle surface, increasing the dosage of flotation reagents [6], [24], [25]Atesok and Celik [26] proposed using high viscosity asphalt to seal the porous and coal slime that is Improving flotation decarbonization efficiency of coal gasification
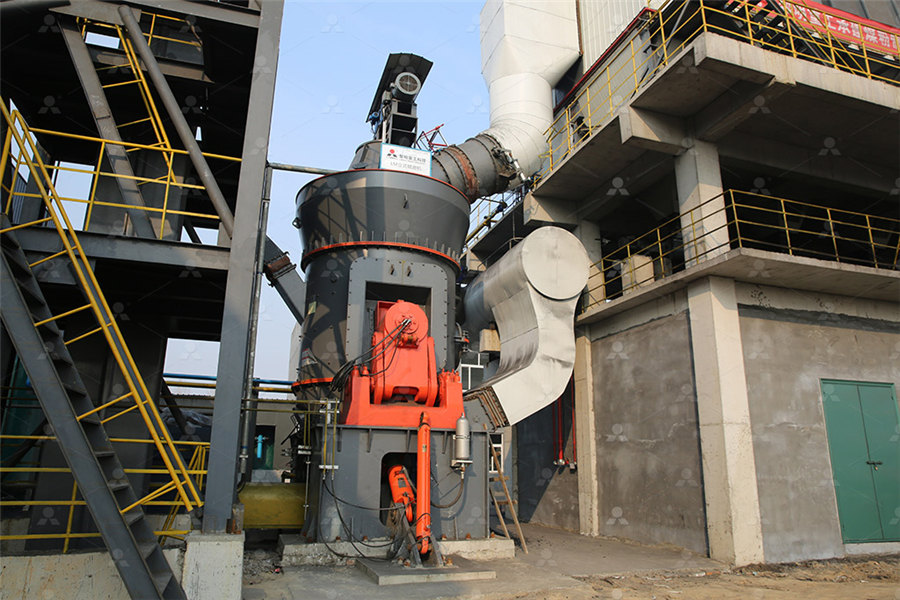
Multiscale analysis of fine slag from pulverized coal gasification in
2024年2月3日 Fine slag (FS) is an unavoidable byproduct of coal gasification FS, which is a simple heap of solid waste left in the open air, easily causes environmental pollution and has a low resource utilization rate, thereby restricting the development of energysaving coal gasification technologies The multiscale analysis of FS performed in this study indicates typical grain size 1110 Coal Cleaning 11101 Process Description12,9 Coal cleaning is a process by which impurities such as sulfur, ash, and rock are removed from coal to upgrade its value Coal cleaning processes are categorized as either physical cleaning or chemical cleaning Physical coal cleaning processes, the mechanical separation of coal from its1110 Coal Cleaning US EPA• Hot air temperature and flow path through the grinding zones have been designed carefully so that it dries out coal without affecting the throughput ball race mill can handle moisture up to 15% • Mill can handle high ash abrasive coal Ash percentage does Raymond mill Schenck Process Holding GmbH vertical / for coal grinding2020年8月12日 As one of the three major forces of coal mills, the grinding force exerts a significant impact on the working process of coal mills and parameters like mill current and outlet temperatureAn investigation of performance characteristics and energetic
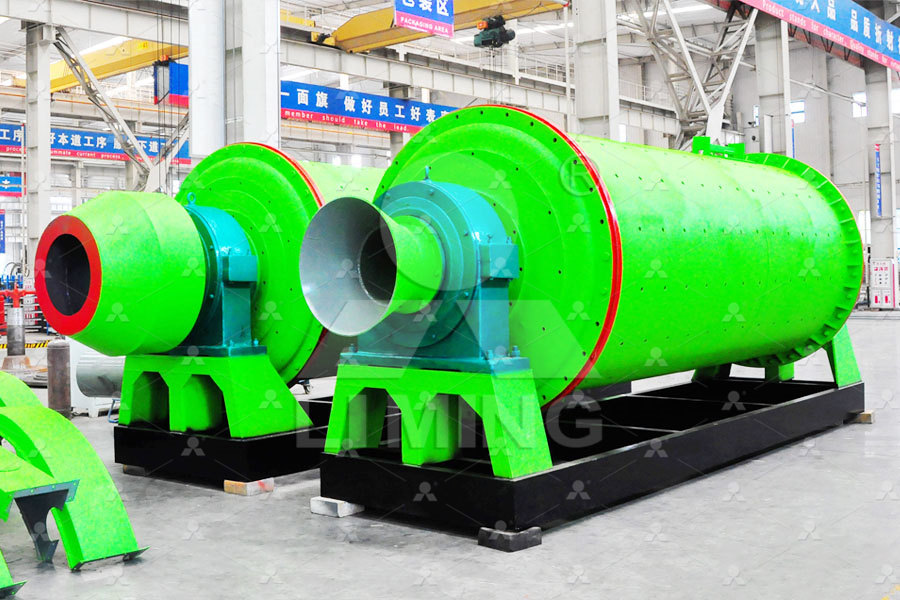
Cement Manufacturing Process INFINITY FOR CEMENT EQUIPMENT
The vertical roller mill fulfills four main functions in one compact piece of equipment: Grinding; Drying; Separation; Transportation; The process is called a drying /grinding process, where most of the material/product is transported pneumatically by drying gases Coal ash is also analyzed chemically which is very vital for raw mix design2014年11月14日 2 Dead storage or outdoor storage • In this storage the coal received at the power plant is stored in dead storage in the form of piles laid directly on the ground the coal stored has the tendency to combine with oxygen of air and during this process coal loss some of its heating value and ignition quality • Due to oxidation the coal may ignite spontaneouslyCoal and ash handling systems PPT Free Download SlideShareIn this work, the chemical demineralization process is explored at a pilot scale to produce the low ash clean coal from different washery rejects 446%–678% demineralization is achieved with Process flow sheet of chemical leaching processstream of ashcarbonsodium carbonate mixture is continuously with drawn from the gasifier and flows to ash removal where it is pro cessed to separate the ash from the melt A simplified flow sheet for this ash removal is presented as Figure 2 The melt stream isI KELLOGG COAL GASIFICATION PROCESS FischerTropsch
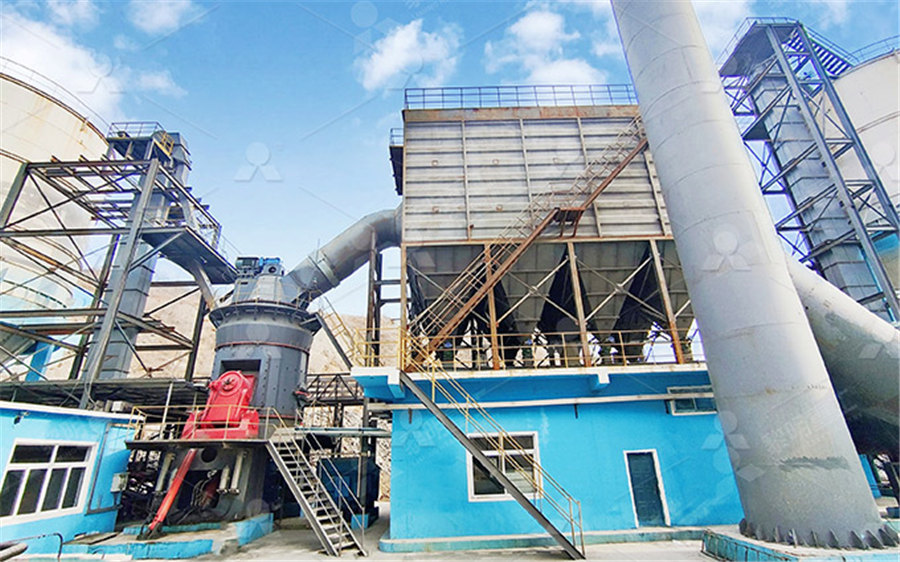
Coal Ash Production Processing Analysis PEC Consulting Group
Coal Ash Processing Selection of process equipment CapEx and OpEx verification Procurement expediting assistance Coal Grinding and Firing Systems HAZOP Analysis A Process Hazard Analysis (PHA) is a key element of a 2023年1月1日 Coal gasification is one of the core technologies for the clean and efficient utilization of coal It is also the basis for process industries such as synthetic coal–based chemicals, synthetic liquid fuels, and integrated coal gasification combined cycle power generation systems (IGCCs) [3]In entrained flow gasifiers, coal is generally gasified at high Recent advances and conceptualizations in process intensification 2020年8月21日 CO2 emissions from coal power generation could be reduced by maximizing the amount of torrefied biomass that can be used in pulverizedcoalfired power plants(PDF) Effect of Biomass Carbonization on the Grinding of Coalcoal substance, and only small quantities are held by the associated mineral matter In contrast, inherent moisture depends on its humidity and thermal history, as well as on coal type 22 Process of drying The process of drying includes the evaporation of surface moisture and, subsequently, the loss of inherent moistureFundamentals of pulverised coal combustion ICSC
.jpg)
COAL GRINDING AND FIRING SYSTEMS HAZOP ANALYSIS
• Process flow sheets and Process and Instrument Diagrams • List of Process control loops and Process and Safety Interlocks • List of Instrumentation and Alarms and Process variables with all limits Equipment: Coal grinding mill Author: Jagrut Upadhyay Created Date:2020年4月25日 Fly ash (FA) from lignite coal combusted in different Thermal Power Plants (TPPs) was used for the synthesis of zeolites (FAZs) of the NaX type by alkaline activation via three laboratory procedures FAZs were characterized with respect to their morphology, phase composition and surface properties, which predetermine their suitability for applications as Progress in the Utilization of Coal Fly Ash by Conversion to MDPIIn coal combustion, the efficiency and safety of the process are paramount Indirect firing coal grinding systems play a critical role in optimizing these aspects, especially in industrial applications such as power plants and cement manufacturing This article explores the components, advantages, and operational considerations of indirect firing cIndirect Firing Coal Grinding Systems: Enhancing Efficiency and These flow sheets are based on converting 50,000 tons per day of clean coal representative of the Pittsburgh and Kentucky No 9 coal seams Flow sheets were used by Union Carbide Corporation, Oak Ridge National Laboratory, in a survey of coal handling/preparation equipment requirements for future coal conversion plants Operations covered in Conceptual flow sheets development for coal conversion plant coal
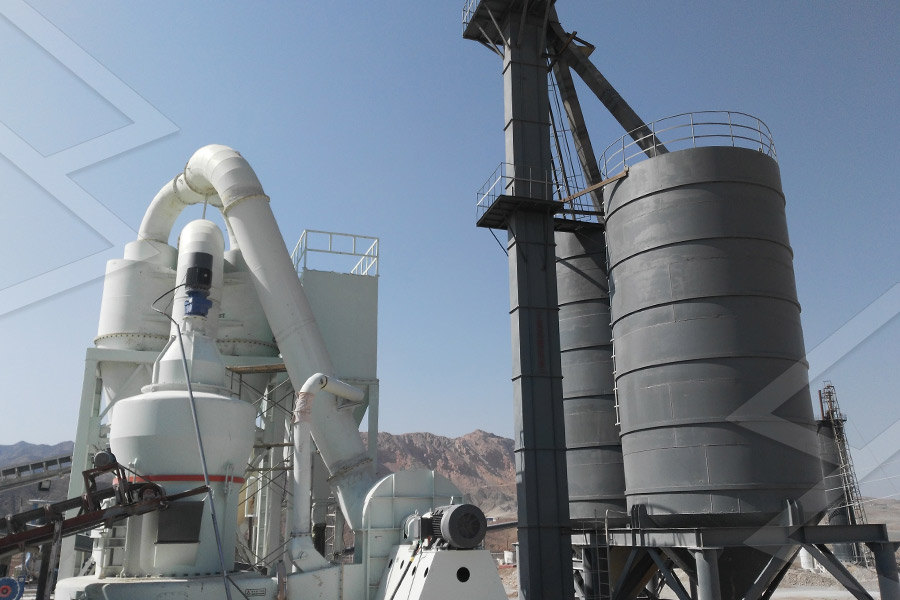
Coal Fly Ash Utilisation and Environmental Impact
2021年5月11日 Fly ash is used as a cementitious material as well as a partial cement replacement It also serves as a fine aggregate in concrete (Khan et al 2017; Xu and Shi 2018)According to American Coal Ash Association 2020, around 37% of 38 million tons of fly ash produced in the USA are used in concreteThe use of fly ash in construction as cementitious 2024年9月27日 In the context of the mounting crisis of waste management and environmental sustainability, coal bottom ash (CBA) emerges as a pioneering solution in the field of construction This study, which is a pioneering investigation, delves into the transformative impact of integrating CBA into the fabric of various concrete compositions, which range from traditional mortar to Coal bottom ash and its applications in cement and concrete assumed that the coal grinding and firing system is operated at least at minimum design capacity The HAZOP Study of coal grinding and firing systems addresses the following aspects: 1 The hazards of the coal grinding and firing process 2 Engineering and administrative controls applicable to the hazards and their interrelationships 3COALIn order to produce 49,192 kg/h of hydrochar from coHTC of coal waste and food waste, Mazumder et al (2022) also developed a process flow diagram that took into account seven reactors, six pumps Simplified process flow diagram of hydrochar production from co
.jpg)
(PDF) Development of Coal Mine Filling Paste with Certain Early
2021年1月31日 Development of Coal Mine Filling Paste with Certain Early Strength and Its Flow Characteristics2021年3月12日 Depending on this high feed moisture the mill rating is determined by the drying process whereas for anthracite, hard coal and petcoke the rating of the mill is determined by the grinding process The great variety of solid fuel properties, such as grindability, ash content, volatiles as well as the required product fineness, calls for a wide range of operating statesMPS mills for coal grinding AYS EngineeringAfter removing the coal from the ground, the miners may send it to a preparation plant near the mining site The plant cleans and processes coal to remove rocks, dirt, ash, sulfur, and other unwanted materials This process increases the heating value of the coalCoal Mining Processing Equipment Flow Chart Cases JXSCCoal is the second largest fuel in the global energy mix, and it accounted for 27% of the global energy consumption in 2018 (BP, 2019)China remains to be the world’s largest energy consumer, and it contributed 34% to the growth of the global energy demand in 2018 (BP, 2019)In addition, coal is still China’s dominant fuelSynthesis of Zeolites from Coal Fly Ash for the Removal of
.jpg)
process flow diagram of coal based power plant Grinding Mill
After coal comes out of the ground, it typically goes on a conveyor belt to a preparation plant that is located at the mining site The plant cleans and processes coal to remove dirt, rock, ash, sulfur, increasing the heating value of the coal During this coal processing, the used industrial equipment can be called coal processing equipmentsName: Coal Preparation Vertical Coal Mill For Coal Chemical Industry Type: Coal Grinding Capacity: 10~90 T/h Motor Power: 1101120kwQuality Vertical Coal Mill, Limestone Vertical Mill factory, Vertical