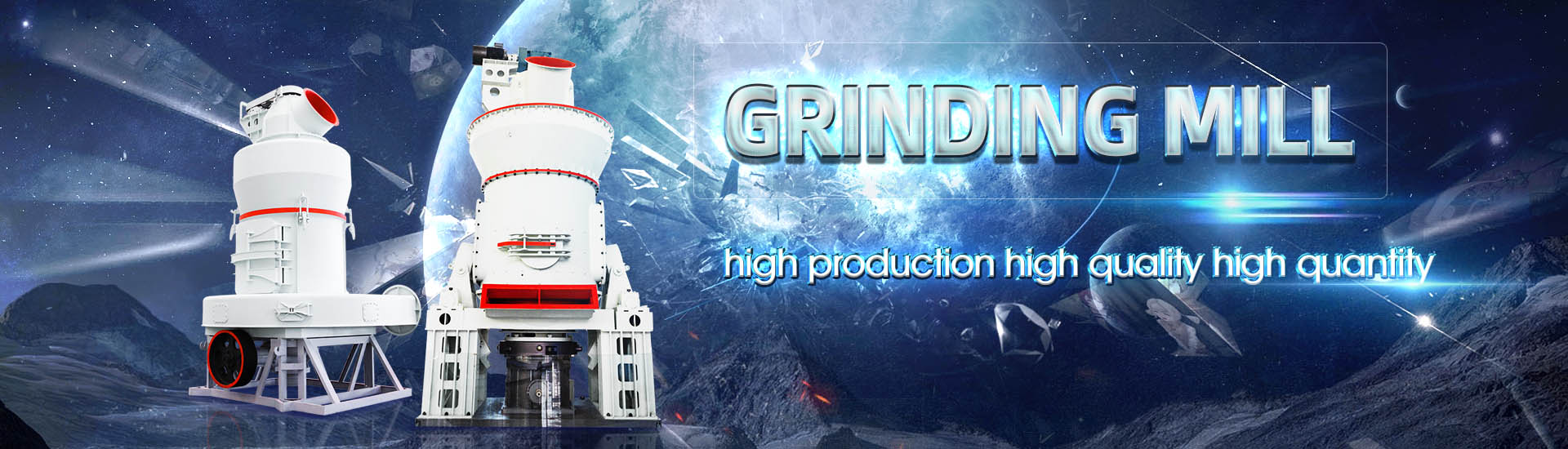
Safety of township milling workshop
.jpg)
Milling machine risk assessment Dyson University of Cambridge
Operator Safety and Personal Protective Equipment Only one person at a time may operate the machine, unless training is being given The operators must wear eye protection when on the Safeguarding of workshop machinery is covered in various ways by the following: • The Health and Safety at Work etc Act 1974 • The Supply of Machinery (Safety) Regulations 2008Machine workshop safetyThe information in this booklet is provided as a guide for the minimum safety training that shall be provided to personnel prior to being authorized to use of any of the following machining tools STANDARD OPERATING PROCEDURES for COMMON TOOL Using machine shop equipment and tools may be hazardous EHS teaches you about personal protective equipment, machine guarding, and recommended safety policiesMachine Shop Safety EHS Harvard University

Safety and health in the use of machinery
certain safety and health risks in a large number of workplaces all over the world Many new types of machinery are also introduced into the market each year This code of practice sets out Any workshop must be considered as a potentially dangerous place where minor and fatal accidents can and must be avoided Foolishness, carelessness and malpractice must be HAZARDS IN THE WORKSHOP Safety at Work SpringerThe vertical mill is a safe machine, but only if the worker is aware of the hazards involved You must always keep your mind on your work in order to avoid accidents Distractions should be MILLING MACHINE TRAIN THE TRAINER (SAFETY, PARTSEngineering Workshop Safety Guidelines (a) Never adopt a casual attitude in the workshop and always be conscious of the potential hazards (b) Ensure that personal clothing is suitable to ENGINEERING WORKSHOP SAFETY MANUAL University of
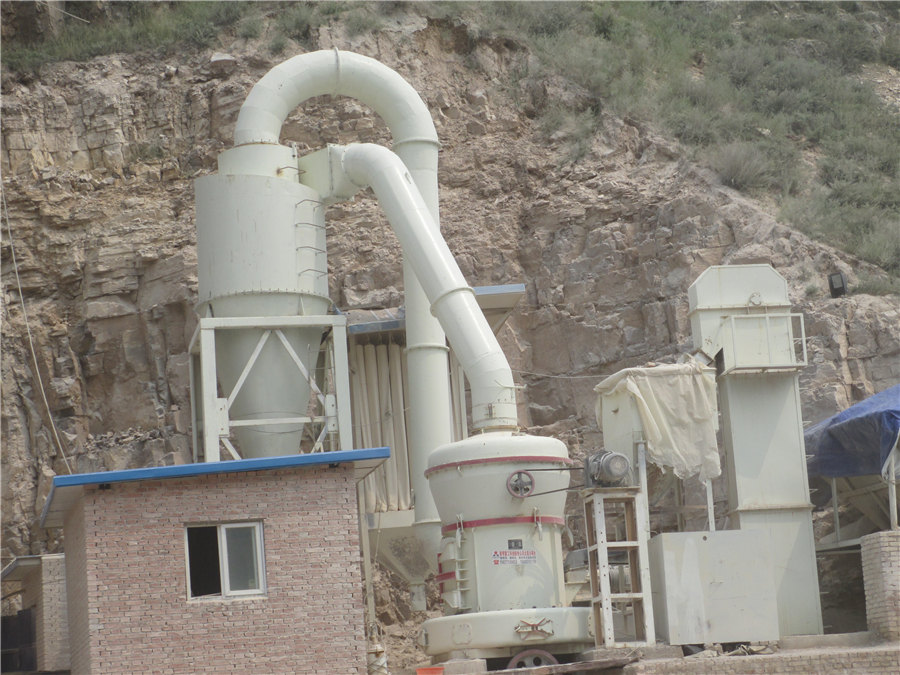
Workshop safety
Category 1: Excellence in work health and safety systems; Category 2: Excellence in implementing a work health and safety solution; Category 3: Excellence in work health and safety culture; Category 4: Excellence in contributions to work health and safety; Category 5: Excellence achieved by a health and safety representativeSafety in Further Education: chapter 5 Workshops Health and Safety at Work, Booklet No 20, Drilling Machines Guarding of Spindles and Attachments Health and Safety at Work, Booklet No 33, in the Use of Guillotines and Shears Health and Safety at Work, Booklet No 42, Guarding of Cutters of Horizontal Milling MachinesHAZARDS IN THE WORKSHOP Safety at Work Springer2023年11月20日 Developing a Comprehensive Safety Plan Crafting a Safety Blueprint A safety plan is a dynamic entity, evolving and adapting to the unique needs and challenges of each workshop It encompasses risk assessment, Machine Shop Safety 101: Tactics for HazardFree University Health and Safety Risk assessments Code of Practice for Student Workshops Risk Assessment Milling Machine (Horizontal and Vertical) 17 February 2016 1 of 4 Ref; Health Safety Executive Engineering in Workshops Risk Assessment MM01: Milling Machines ESTABLISHMENT University of Cambridge, Dept of Engineering,Milling machine risk assessment Dyson University of Cambridge
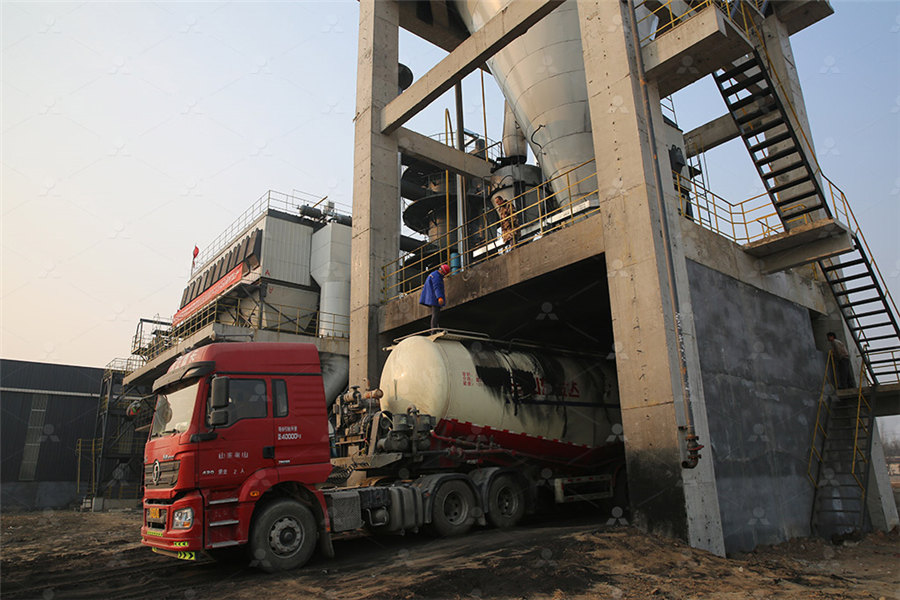
Mechanical Workshop Risk Assessment EntirelySafe
2023年3月19日 Implement a hot work permit system and conduct regular safety audits Fabrication: Provide PPE, such as safety glasses, gloves, and hearing protection Enclose or guard machinery to prevent access to moving parts Conduct regular safety audits and ensure proper training for all workers Casting: Provide PPE, including heatresistant gloves and Work Health and Safety Act (2011) has requirements for Person Conducting Business or Undertaking (PCBU) to manage risks associated with the use of plant The Guide to Machine Safety provides information to help you to manage risks with using machinery (plant) in your workplace The guide uses a range of examples and will help you to:GUIDE TO MACHINE SAFETY2023年3月1日 Operators should keep these milling machine safety principles in mind to avoid serious injury in the workshop Machine guards can only do so much! If your shop has different milling machines , ensure your operators are used to each machine’s unique design and are aware of their surroundingsMilling Machine Safety Tips You Must Always Follow! Lathe milling machines Eli hitney is most often mentioned as the first to design and construct a milling machine that was dependable, and which served as a prototype for later, improved cutting machines 14 In 1936, Rudolph Bannow conceived of the Bridgeport milling machine, which is still in production today It was lighter, cheaper, and easierMILLING MACHINE TRAIN THE TRAINER (SAFETY, PARTS
.jpg)
8 Advanced Safety Protocols Every CNC Machinist Must Know
2024年1月27日 CNC machinists must adhere to eight critical safety protocols to ensure a secure working environment These include: wearing appropriate personal protective equipment (PPE) such as safety glasses, hearing protection, and steeltoed boots; maintaining a clean and organized workspace to prevent trips and falls; properly securing workpieces to avoid flying 2023年8月2日 A noise detection conducted in a machinery factory’s forging workshop showed results ranging from 83100, 2dB (A), with an average of 9208dB (A) Punching machines and shearing machines can also produce highintensity noise, but the intensity is typically lower than that of forging hammersProtect Yourself from These 5 Machining Hazards MachineMFG2023年6月20日 Safety Features of CNC Machines Understanding the hazards associated with their equipment, manufacturers of CNC machines implement safeguards to reduce the chances of accidents and health issues The CNC CNC Machine Safety: Preventing Accidents in the 2022年2月25日 Safety Operation Rules of CNC Milling Machine 1 The operator must wear the labor protection supplies correctly according to the regulations The operator with long hair must wear a working cap and tuck the hair in the A Safety Guide to CNC Milling Machine
.jpg)
Workshop Practice: Lesson 1 INTRODUCTION TO WORKSHOP PRACTICE, SAFETY
Workshop safety The safety in For example, the belt drive and motor in a lathe or milling machine are enclosed, the back gears in a lathe are either enclosed or provided with cast iron guards or covers Lubricating points are provided on the outer surfaces so that the interior parts are not required to be opened every timeHorizontal Milling Machines: The spindle is horizontal, suited for larger workpieces CNC Milling Machines: These are computercontrolled, offering high precision and automation Understanding the type of milling machine you are working with is crucial for applying the right safety measures General Safety Precautions Read the ManualSafety Tips for Operating Milling Machines: A Comprehensive 2013年9月16日 The first is entitled ‘Workshop Safety research laboratories or other workplaces where drilling machines, milling machines, lathes and similar machine tools are used Under the Provision and Use of Work Equipment Regulations 1998 (PUWER 98), Free Publications Aid Compliance with Workshop Safety Regulations2023年10月11日 Grinding Safety Tips Control measures must be put in place to manage the risks posed by grinding to the health and safety of workers The following list outlines some health and safety control measures that can be put in place in your workplace to reduce workers’ exposure to grinding hazards and keep them safe at work Employee TrainingGrinding Safety Precautions Hazards Control Measures
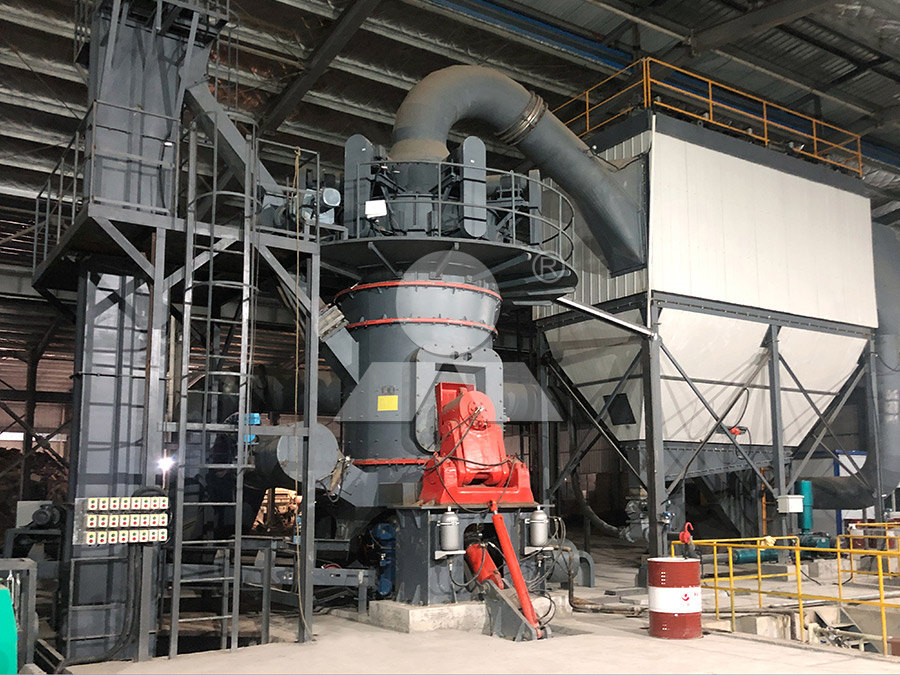
CO DMA 1132 Workshop Safety and Management
2 CO DMA 1132 Workshop Safety And Management Free download as Word Doc (doc / docx), PDF File (pdf), Text File (txt) or view presentation slides online This document provides information on a course titled "Workshop Safety and Management" offered at Kolej Vokasional Sungai Petani 1 The course aims to develop students' knowledge and skills in assisting with Titan discusses the importance of following safety rules and guidelines in the workshop Related Files (1) Mill Setup Checklist Tags: safety tips ALL CONTENT on this site is the intellectual property of TITANS of CNC: Academy You have the right to copy and share all materials herein in any medium or formatSafety Rules and Guidelines TITANS of CNC: Academy(7) The approved layout plan of the workshop should be on display in the workshop Prior approval should be sought from the Education Bureau if changes or alterations are to be made to the layout of the workshop 3 Electrical Safety (1) All electrical wiring installation should comply with the Electricity (wiring) RegulationSAFETY IN SCHOOL WORKSHOPS Education BureauMilling Machine Safety Rules Work must be clamped securely in a vise and vise clamped tightly to the table, or, work must be clamped securely to the table Do not take climb milling cuts on the shop’s mills unless instructed to do so Make sure cutter is rotating in the proper direction before cutting materialSafety Rules LSU Mechanical Industrial Engineering
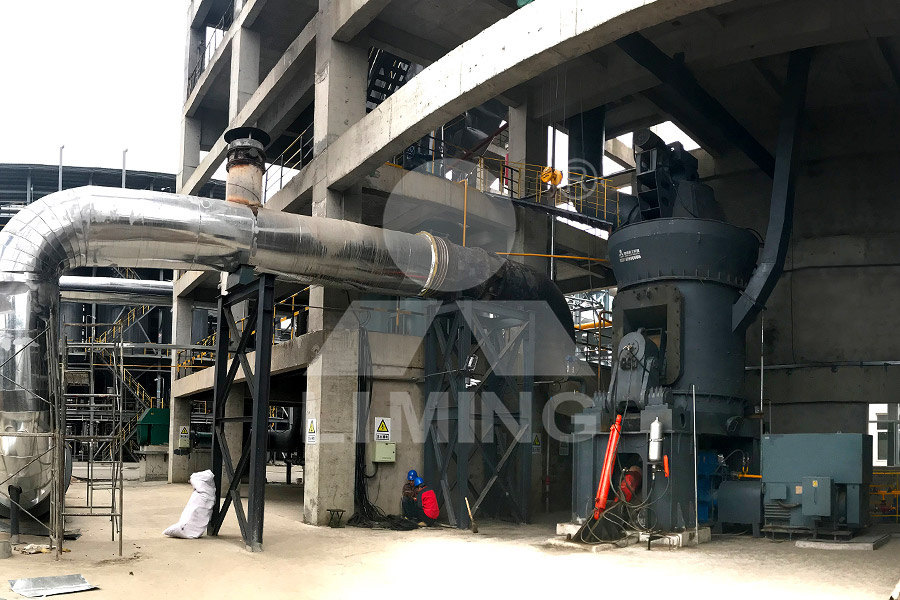
Mill Operators Manual Safety Haas Automation Inc
Basic safety: This machine can cause severe bodily injury This machine is automatically controlled and may start at any time Consult your local safety codes and regulations before you operate the machine Contact your dealer if you have questions about safety issues‘Only a competent trained person should supervise the use of milling machines The trained person should be trained in accordance with the Health and Safety Training Standards in Design and Technology Essential Health Safety for The use of specific machinery and equipment by University Health and Safety Risk assessments Code of Practice for Student Workshops Risk Assessment Milling Machine (Horizontal and Vertical) 17 February 2016 1 of 4 Ref; Health Safety Executive Engineering in Workshops Risk Assessment MM01: Milling Machines ESTABLISHMENT University of Cambridge, Dept of Engineering,Milling machine risk assessment Dyson University of Cambridge2023年11月28日 Creating a culture that encourages continuous improvement will allow all employees to participate in improving safety and efficiency Innovation and suggestions for improvement should be rewarded Regular safety meetings should be organized to discuss safety issues, incident situations, and how to improve work processes and equipment useSafety Practices in CNC Machining: Protecting Workers and
-2.jpg)
11 tips for effective workplace housekeeping Safety+Health
2015年7月1日 Eliminate fire hazards Employees are responsible for keeping unnecessary combustible materials from accumulating in the work area Combustible waste should be “stored in covered metal receptacles and disposed of daily,” according to OSHA’s Hazardous Materials Standard (1910106) The National Safety Council “Supervisors’ Safety Manual” includes Section 6: Promote a Culture of Safety The role of management in fostering a safe working environment Encouraging employee participation and accountability Recognizing and rewarding safetyconscious behavior Section 7: Conclusion:\ In conclusion, ensuring the safety of CNC machine operators and everyone in the workshop is paramountEnsuring Safety in the Workshop: A Comprehensive Guide to 2023年9月11日 List of major machinery, equipment, and allied equipment for ABC Company: 1: Medium size lathe– This is typically used for turning of odd size workpieces, a rough turning of castings or forgings, and any miscellaneous shop items like mandrels for job holding, etc: 2: Compact 5axis CNC lathe– For turning of gear blanks either from raw material or from rough A General Overview of a Good Workshop Layout• Milling machines should be fitted with a space of at least 500 mm between the machine table at the extreme ends of its travel and any fixed object Health and Safety Training in Design and Technology Design and Technology Association Specialist Extension Level S6HS Milling Machines and Machining Centres Milling Machines and Machining Centres 2Health and Safety Training in Design and Technology Milling
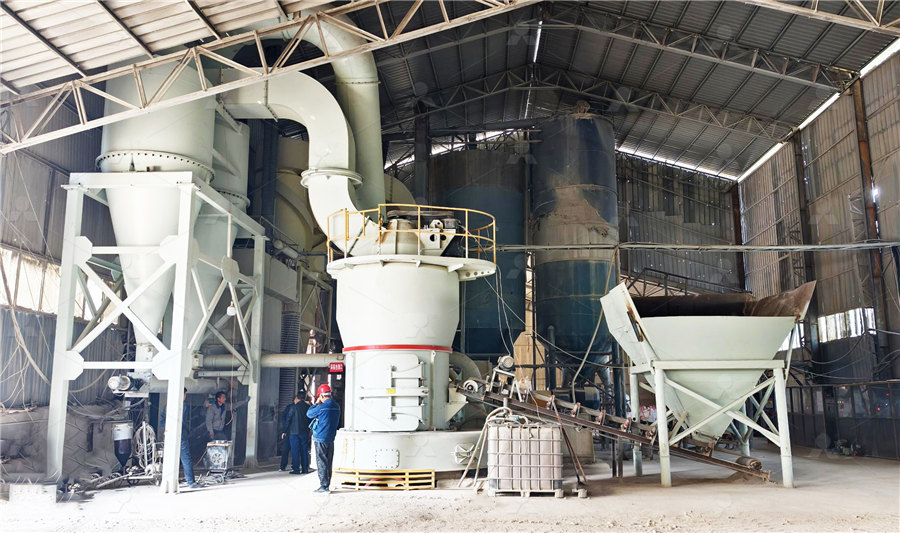
Safety Tips for Operating Milling Machines: A Comprehensive
2024年10月23日 Horizontal Milling Machines: The spindle is horizontal, suited for larger workpieces CNC Milling Machines: These are computercontrolled, offering high precision and automation Understanding the type of milling machine you are working with is crucial for applying the right safety measures General Safety Precautions Read the Manual2019年11月27日 5 Poor guarding techniques — When it comes to heavy machines, a correctly placed guard or barrier can be the difference between safe operation and serious injury, like loss of a limb It goes beyond having machine guards in place, however Sometimes the right system exists but malfunctions, or does not correctly identify hazard situations, such as someone’s 5 Common Machine Shop Injuries, and How to Prevent Them2024年6月10日 The Pennsylvania Department of Transportation (PennDOT) has begun milling the roadway under a safety improvement project at intersections along a 19mile section of Bethlehem Pike in Springfield and Bethlehem Pike Safety Improvement MillingWorkshop and Machine shop practice [18MEL38A/48A] [Department of Mechanical Engineering BIET, Davangere] Page 2 Sl No Topic Page No 1 Demonstration on use of Hand Tools 430 2 Fitting models 3143 3 Introduction to Metal Cutting 4447 4 Lathe 4853 5 Drilling 5457 6 Shaping Machine 5867 7 Milling Machine 6877 8WORKSHOP MACHINESHOP PRACTICE LAB MANUAL Bapuji
.jpg)
(PDF) Selecting the safest CNC machining workshop using
2021年4月2日 The safety of a manufacturing workshop using mostly CNC machine tools as tech nological equipment depends on the way these machines are running One must keep inISO 141223, Safety of machinery — Permanent means of access to machinery — Part 3: Stairs, stepladders and guardrails; ISO 141224, Safety of machinery — Permanent means of access to machinery — Part 4: Fixed ladders; ISO 14738, Safety of machinery — Anthropometric requirements for the design of workstations at machineryMachine tools safety — Machining centres, Milling machines, 2013年9月28日 2 1 GENERAL AND PERSONAL HEALTH AND SAFETY REQUIREMENTS AND PROCEDURES PERSONAL SAFETY PROCEDURES: Has to do with the way in which a person is attired for the workshop or worksite for practical activity Always wear your personal protective equipment (ppe) Do not wear defective ppeSafety in the workshop final PPT Free Download SlideShareLathe/Workshop Safety Guidelines Lathe Safety Guidelines V25 © G Whaling Feb 2013 AttributionNon CommercialShare Alike 30 Unported Page 4 of 4Lathe/Workshop Safety Guidelines
.jpg)
STANDARD OPERATING PROCEDURES for COMMON TOOL
• Any person working in the welding workshop must be familiar with the University Health and Safety Policy • The welding fume extractor must be used during any welding operation • Personal Protective Equipment provided must be used when necessary • Barrier cream, lab coats, safety glasses/goggles and safety shoes are to be used as theThe Supply of Machinery (Safety) Regulations 2008, amended by the Supply of Machinery (Safety) (Amendment) Regulations 2011, forms the cornerstone of machinery safety in the UK These regulations mandate that all machines introduced to the European market bear the CE mark, in compliance with the European Machinery Directive 2006/42/ECMachinery Safety Legislation in the UKOur range of safety guards for machine tools are for when you have older workshop tools and production machinery While modern production machinery is manufactured to meet the requirements of PUWER 98, older machinery that may still be critical to your business might not comply with these standardsWorkshop Machine GuardsCreating a strong safety culture is vital to continuously improve and maintain safe practices This involves fostering open communication between management and employees, encouraging the reporting of nearmisses, and conducting regular safety audits Operator feedback should be valued and used to update risk assessments and enhance safety Ensuring Safety: A Comprehensive Risk Assessment for CNC Milling